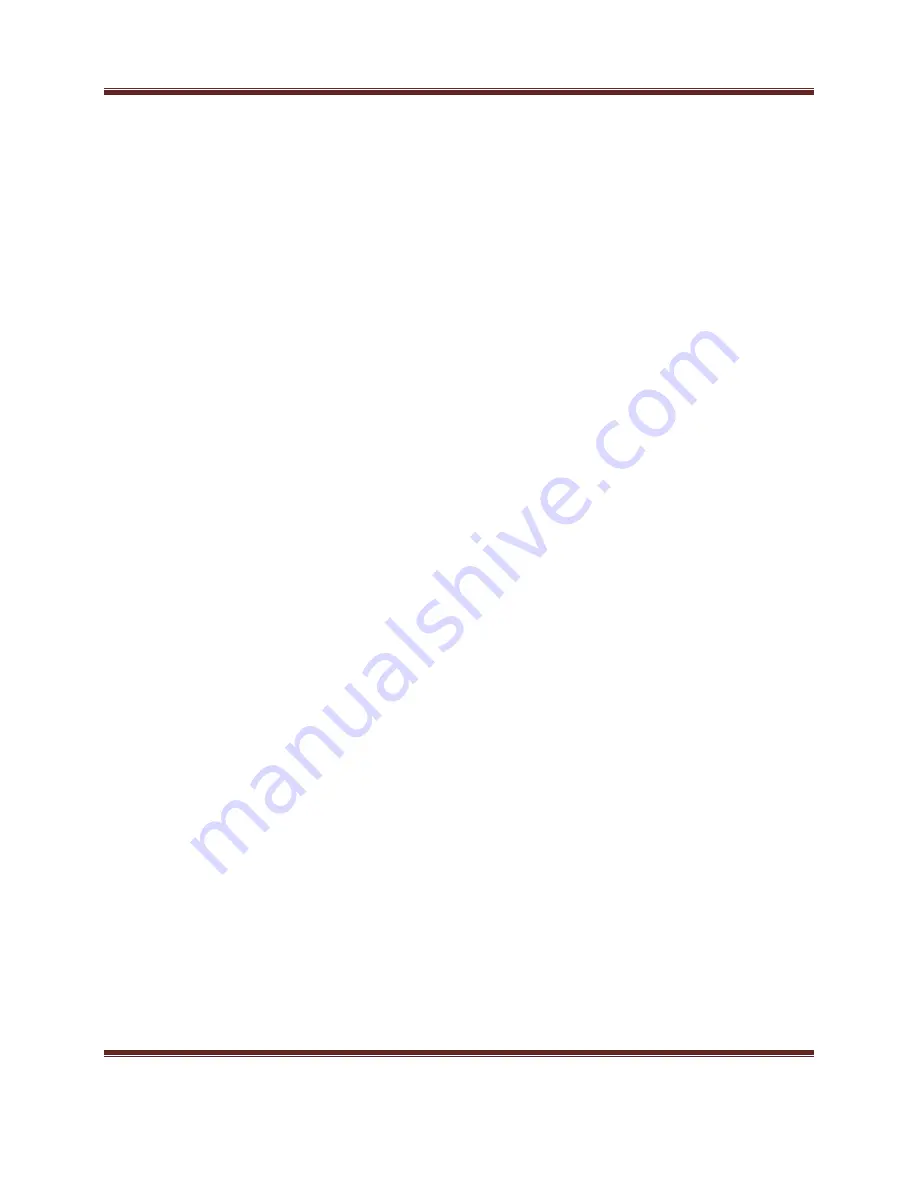
F-84F Thunderstreak 90mm edf
Pagina 2
the weight on each plane to a minimum without sacrificing strength.
The same program that generates the design and plans also drives the cnc cutter, so every part is
reproduced exactly as it was designed. Cnc cutting also allows us to fit more parts on each sheet of
wood, reducing the waste, and lowering the cost to you.
Plastics
Several parts are accurately reproduced high quality Polystyrene, the canopy is made from PETG or
Lexan
General Building Information
The F-84F 90MM can be built by a person with experienced building skills. It is not designed for
someone who has built a trainer or low wing sport plane. No unusual building techniques are required,
although more difficult areas are explained in detail where necessary. Certain steps in the building
process must be followed as depicted, or you might find yourself digging back into the structure to
redo something. These areas are outlined when necessary. Occasionally hints will be included at
certain building steps. These are not required for completion, rather they are tips intended to ease a
particular process. The cnc router does cut through the wood, as a result of this, occasionally there will
be fraying on the surface of the wood. This is normal, and is only a surface problem and does not
affect the wood in any other way. Similarly, the cnc settings are optimized for wood thickness
averages, so occasionally, due to variations even in individual sheets, some areas might not cut
through completely. Simply use care in cutting the parts from the sheets; most of the time, the parts
will break out of the sheets!
Note that due the differences in wood thickness per sheet it is advisable to sand the tabs a bit so they
slide in easy , also sand the openings so parts slide in easy , hard pushing parts have a high risk of
breaking, it is not necessary the rework the corners of the cut-outs , this is done by the cnc machining
Hardware and an edf unit are not included in the kit. There are so many choices for quality hardware
that these choices are left to the individual preferences of the builder, rather than include something
in the kit that you’ll probably throw away anyway.
This aircraft is not a toy. It must be flown in a responsible manner according to the rules set forth by
Law. The builder assumes the responsibility for the proper assembly and operation of this product.
Rbckits shall have no liability whatsoever, implied or expressed, arising out of the intentional or
unintentional neglect, misuse, abuse, or abnormal usage of this product. Rbckits shall have no liability
whatsoever arising from the improper or wrongful assembly of the product nor shall it have any
liability due to the improper or wrongful use of the assembled product. Rbckits shall have no liability
for any and all additions, alterations, and modifications of this product.