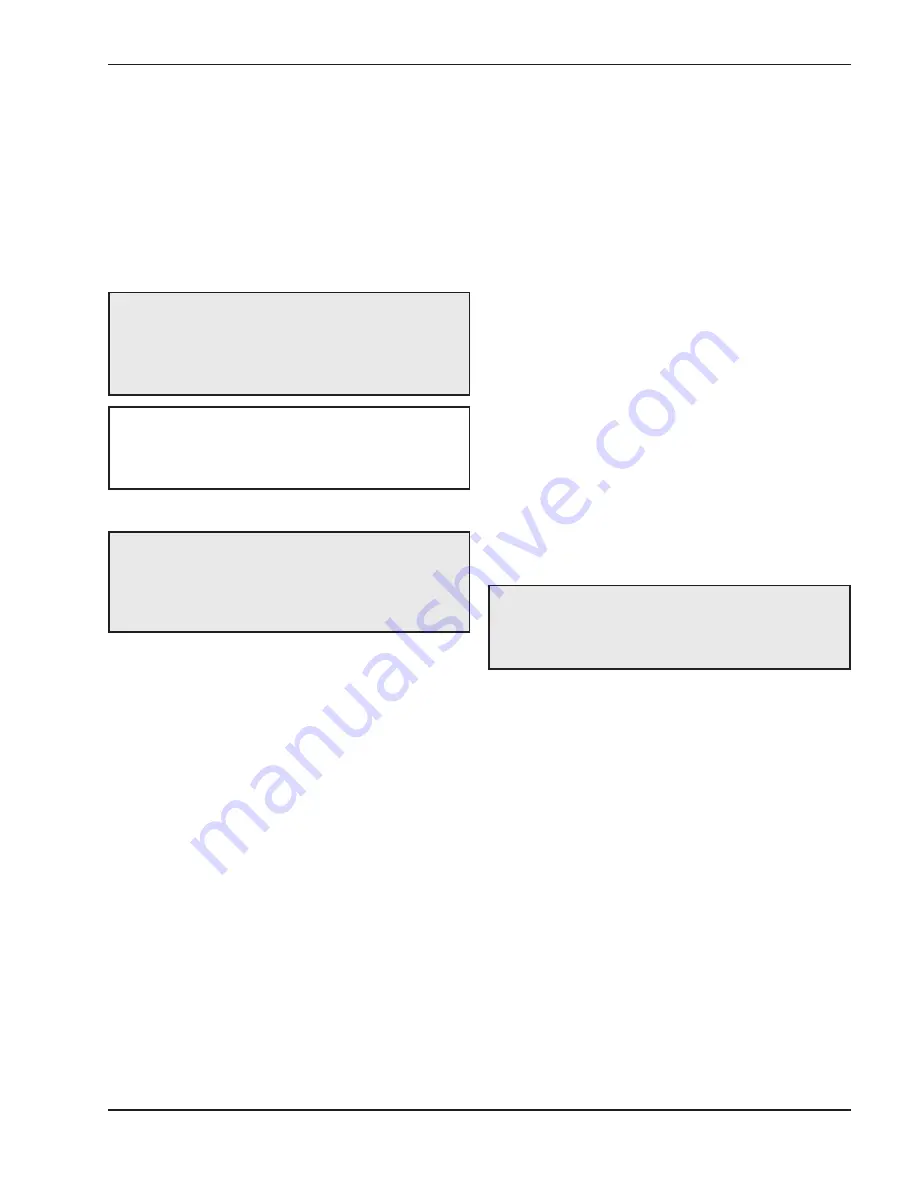
4. Refer to the B149 Installation Code for additional
information
Water Piping
General
The heater should be located so that any water leaks
will not cause damage to the adjacent area or struc-
tures.
Relief Valve Piping
Temperature & Pressure Gauge
The temperature and pressure gauge is shipped loose
for field installation and must be installed within 12
inches of the boiler outlet (if possible) in an easily
readable location. Installation must comply with ASME
Section IV as well as all applicable national, state and
local codes.
Hydrostatic Test
Unlike many types of heaters, this heater does not re-
quire hydrostatic testing prior to being placed in
operation. The heat exchanger has already been fac-
tory-tested and is rated for 160 psi operating pressure.
However, Raypak does recommend hydrostatic test-
ing of the piping connections to the heater and the rest
of the system prior to operation. This is particularly
true for hydronic systems using expensive glycol-
based anti-freeze. Raypak recommends conducting
the hydrostatic test before connecting gas piping or
electrical supply.
13
Leaks must be repaired at once to prevent damage to
the heater. NEVER use petroleum-based stop-leak
compounds.
To perform hydrostatic test:
1. Connect fill water supply. Fill heater with water.
Carefully fill the rest of the system, making sure to
eliminate any entrapped air by using high-point
vents. Close feed valve. Test at standard operating
pressure for at least 24 hours.
2. Make sure constant gauge pressure has been
maintained throughout test.
3. Check for leaks. Repair any that are found.
Flushing/Cleaning of System Piping
Many of the chemicals used to perform this function
will harm the heat exchanger as well as some gaskets
and seals within the unit, causing a non-warrantable
failure. When required, Raypak recommends the boil-
er be isolated from the system piping prior to flushing
or cleaning with any cleaning agent.
Cold Water Operation
This heater is equipped with a proprietary condensate
evaporation system which will evaporate any conden-
sate that may begin to accumulate inside the primary
heat exchanger with water temperatures as low as
120°F (49°C).
Heaters operated with an inlet temperature of less
than 120°F (49°C) MUST have a low-temperature
operation system (Figs. 9, 10 and 11) to prevent prob-
lems with condensation. Inlet water temperatures
below 120°F (49°C) can excessively cool the products
of combustion, resulting in collection of condensate in
the heat exchanger area beyond the capacity of the
condensate evaporation system.
Failure to reach or exceed 120°F (49°C) may damage
or cause failure of the heat exchanger, combustion
chamber, or other parts within the combustion cham-
ber. It can cause operational problems, bad
combustion, sooting, flue gas leakage and reduced
service life of the appliance and the vent system. A
bypass allows part of the heater discharge water to be
mixed with the cooler water returning to the heater
WARNING:
Pressure relief valve discharge piping
must be piped near the floor and close to a drain to
eliminate the potential of severe burns. Do not pipe
to any area where freezing could occur. Refer to
local codes.
CAUTION:
Damage due to internal condensation
may occur if the heater inlet water temperature does
not exceed 120°F (49°C) within 7 minutes of start-
up.
CAUTION:
This heater requires forced water
circulation when the burner is operating. See Table F
and Table G for minimum and maximum flow rates.
The pump must be interlocked with the heater to
prevent heater operation without water circulation.
NOTE:
Minimum pipe size for in/out connections is
2 in. NPT for 504A and 754A models and 2-
1
⁄
2
in NPT
for 1104A–2004A models. Verify proper flow rates
and ∆T as instructed in this manual.
Summary of Contents for MVB 504A
Page 44: ...44 WIRING DIAGRAM Models 504A 2004A ...
Page 58: ...58 ...
Page 62: ...62 ...
Page 63: ...63 ...