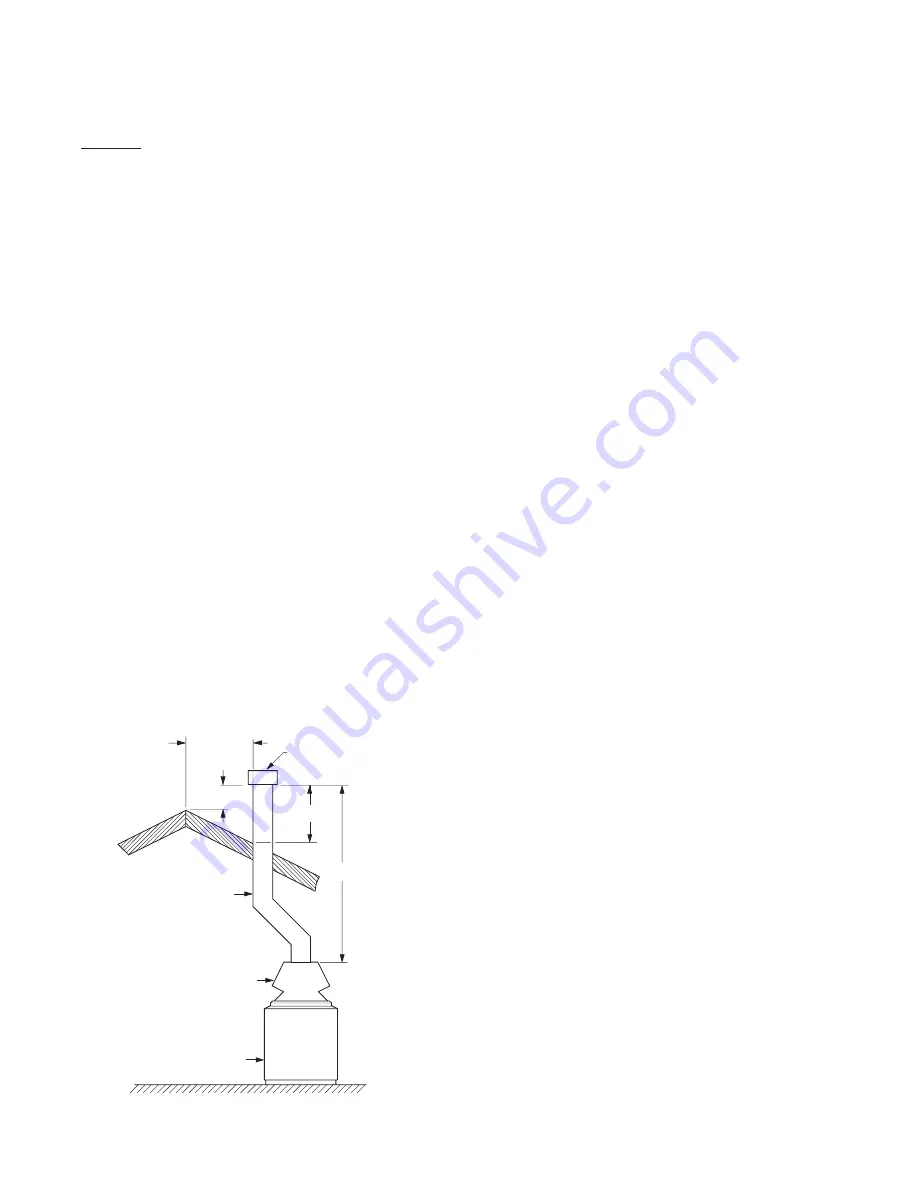
As much as possible avoid long horizontal runs of
vent pipe and too many elbows. If installation requires
horizontal non-vertical runs, the vent pipe must have a
minimum of 1/4 inch per foot rise and should be supported
at not less than five foot intervals. Plumbers tape,
crisscrossed, will serve to space both horizontal and
vertical piping. Gas vents supported only by the flashing
and extending above the roof more than five feet should
be securely guyed or braced to withstand snow and wind
loads. We recommend use of insulated vent pipe spacer
through the roofs and walls.
For protection against rain or blockage by snow, the
vent pipe must terminate with a vent cap which complies
with the local codes or, in the absence of such codes, to
the latest edition of the National Fuel Gas Code,
ANSI Z
223.1.
The discharge opening must be a minimum of two
feet vertically from the roof surface and at least two feet
higher than any part of the building within ten feet. Vent
stack shall be at least five feet in vertical height above the
draft hood outlet. The vent cap location shall have a
minimum clearance of 4 feet horizontally from, and in no
case above or below, unless a 4-foot horizontal distance
is maintained, from electric meters, gas meters, regula-
tors and relief equipment.
The weight of the vent stack or chimney must not rest
on heater draft hood. Support must be provided in
compliance with applicable codes. The heater top and
draft hood must be readily removable for maintenance
and inspection. Vent pipe should be adequately sup-
ported to maintain proper clearances from combustible
constructions.
Type “B” double wall or equivalent vent pipe is
recommended. However single wall metal vent pipe may
be used as specified in the latest edition of the National
Flue Gas Code
ANSI Z 223.1.
At the time of removal of an existing boiler, the
following steps shall be followed with each appliance
remaining connected to the common venting system
placed in operation, while the other appliances remain-
ing connected to the common venting system are not in
operation.
(a) Seal any unused openings in the common
venting system.
(b) Visually inspect the venting system for
proper size and horizontal pitch and deter-
mine there is no blockage or restriction,
leakage, corrosion and other deficiencies
which could cause an unsafe condition.
(c) Insofar as is practical, close all building
doors and windows and all doors between
the space in which the appliance remaining
connected to the common venting system
are located and other spaces of the build-
ing. Turn on clothes dryers and any appli-
ance not connected to the common venting
system. Turn on any exhaust fans, such as
range hoods and bathroom exhausts, so
they will operate at maximum speed. Do not
operate a summer exhaust fan. Close fire
place dampers.
(d) Place in operation the appliance being
inspected. Follow the lighting instructions.
Adjust thermostat so appliance will operate
continuously.
(e) Test for spillage at the draft hood relief
opening after 5 minutes of main burner
operation. Use the flame of a match or
candle, or smoke from a cigarette, cigar or
pipe.
(f) After it has been determined that each
appliance remaining connected to the
common venting system properly vents
when tested as outlined above, return doors,
windows, exhaust fans, fireplace dampers
and any other gas burning appliance to
their previous conditions of use.
(g) Any improper operation of the common
venting system should be corrected so the
installation conforms with the latest edition
of the National Fuel Gas Code,
ANSI Z 223.1
When re-sizing any portion of the common
venting system, the common venting system
should be re-sized to approach the minimum
size as determined using the appropriate tables
in part 11 of national Fuel Gas Code,
ANSI Z 223.1.
For special venting applications that require reduced
vent sizes and through the wall venting, the Type D
Induced Draft Assembly can be used. Consult the
factory or your local Raypak representative.
10
5' MIN
2' MIN
10' OR LESS
2' MIN
VENT CAP
VENT PIPE
DRAFT HOOD
HEATER
Fig. #8119
Summary of Contents for 514-824
Page 15: ...15 ...
Page 16: ...16 151965 824 825 000 BTUH ...
Page 17: ...17 152141 514 724 512 000 THRU 726 000 BTUH 5 ...
Page 18: ...18 152142 824 825 000 BTUH 6 ...
Page 27: ...this page is empty ...
Page 28: ...28 PILOTASSEMBLY ELECTRONICIGNITION PILOTASSEMBLY STANDINGPILOT Fig 9293 Fig 9294 ...
Page 29: ...29 ...
Page 30: ...30 ...
Page 31: ......