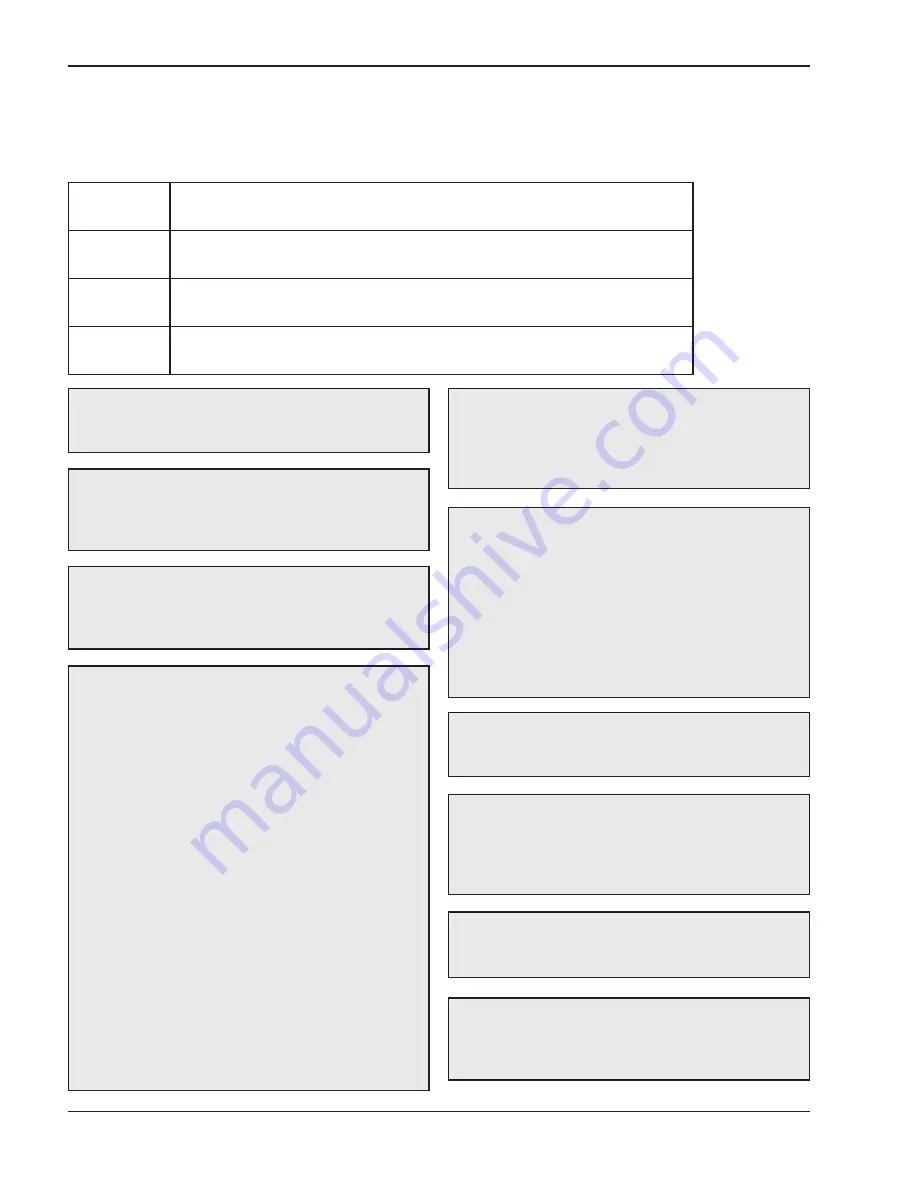
DANGER:
Indicates the presence of immediate hazards which will cause severe
personal injury, death or substantial property damage if ignored.
WARNING:
Indicates the presence of hazards or unsafe practices which could cause
severe personal injury, death or substantial property damage if ignored.
CAUTION:
Indicates the presence of hazards or unsafe practices which could cause
minor personal injury or product or property damage if ignored.
NOTE:
Indicates special instructions on installation, operation, or maintenance which
are important but not related to personal injury hazards.
DANGER:
Make sure the gas on which the heater
will operate is the same type as that specified on the
heater rating plate.
WARNING:
Should overheating occur or the gas
supply valve fail to shut, do not turn off or disconnect
the electrical supply to the heater. Instead, shut off
the gas supply at a location external to the heater.
WARNING:
Do not use this heater if any part has
been under water. Immediately call a qualified
service technician to inspect the heater and to
replace any part of the control system and any gas
control which has been under water.
WARNING:
To minimize the possibility of improper
operation, serious personal injury, fire, or damage to
the heater:
•
Always keep the area around the heater free of
combustible materials, gasoline, and other
flammable liquids and vapors.
•
Heater should never be covered or have any
blockage to the flow of fresh air to the heater.
WARNING - CALIFORNIA PROPOSITION
65:
This product contains chemicals known to the
State of California to cause cancer, birth defects or
other reproductive harm.
WARNING:
Risk of electrical shock. More than one
disconnect switch may be required to deenergize the
equipment before servicing.
CAUTION:
Operation of this heater in low-
temperature systems requires special piping.
Harmful internal condensation will occur if the inlet
water temperature does not exceed 105°F. Warranty
claims will be denied when condensation occurs.
CAUTION:
If this heater is to be installed above
radiation level, it must be provided with a low water
cut-off device at the time of heater installation.
CAUTION:
If this heater is to be installed in a
negative or positive pressure equipment room, there
are special installation requirements. Consult factory
for details.
WARNINGS
Pay Attention to These Terms
4
WARNING:
This unit contains refractory ceramic
fiber (RCF) insulation in the combustion chamber.
RCF, as manufactured, does not contain respirable
crystalline silica. However, following sustained
exposure to very high temperatures (>2192F), the
RCF can transform into crystalline silica
(cristabolite). The International Agency for Research
on Cancer (IARC) has classified the inhalation of
crystalline silica (cristabolite) as carcinogenic to
humans.
When removing the burners or heat exchangers,
take precautions to avoid creating airborne dust and
avoid inhaling airborne fibers. When cleaning spills,
use wet sweeping or High Efficiency Particulate Air
(HEPA) filtered vacuum to minimize airborne dust.
Use feasible engineering controls such as local
exhaust ventilation or dust collecting systems to
minimize airborne dust. Wear appropriate personal
protective equipment including gloves, safety
glasses with side shields, and appropriate NIOSH
certified respiratory protection, to avoid inhalation of
airborne dust and airborne fiber particles.