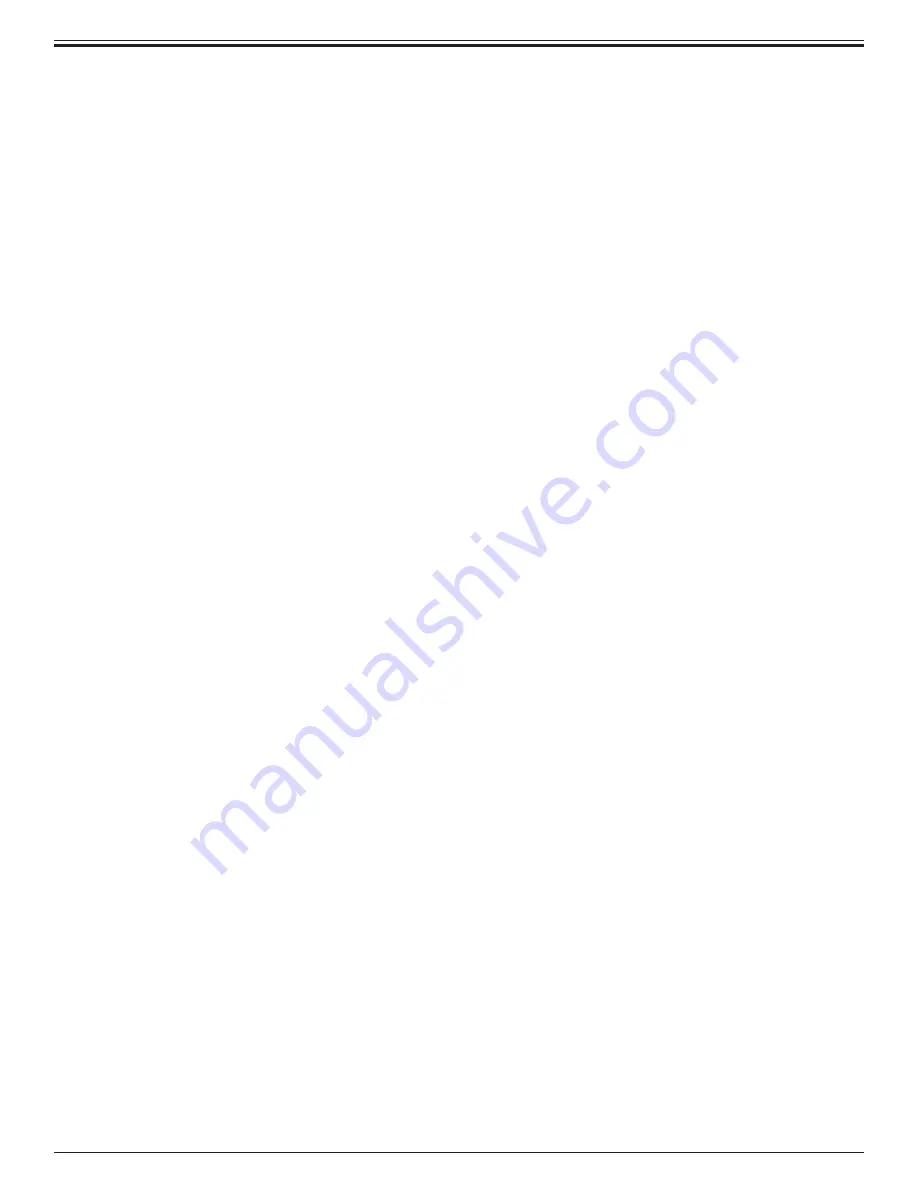
prevent a high pressure drop. Remember,
these tanks can weigh up to 30 pounds when
full of water; a firm, level area is required.
3. RO Manifold Assembly–The manifold can
be installed on either the right or left side of
the under–sink area or a cabinet. The right
side is recommended because the tubing will
be to the back of the cabinet and out of the
way. Installation in the basement is also an
option, one location is near the laundry/
utility sink where cold potable water and
drain access is handy. The mounting location
should allow adequate clearance and
accessibility for cartridge changes.
4. Feed Water Connection–The Feed Water
Saddle Valve should be located as close to the
manifold assembly as possible. USE A
POTABLE COLD WATER SUPPLY ONLY.
Softened water is preferred as it will extend
the life of the RO Membrane.
5. Drain Connection–The waste water must go
to drain through an anti–siphon air gap. The
air gap is provided for in the base of the faucet.
If discharging into a utility sink or standpipe,
an air gap of greater than 1" above the flood
rim must be provided.
Do NOT connect the system drain line to the
dishwasher drain or near the garbage disposal.
Backpressure from these units may cause the
air gap to overflow.
SECTION IV. INSTALLATION STEPS
All plumbing should be done in accordance with
state and local plumbing codes.
NOTE: Some codes may require installation by a
licensed plumber; check with the local plumbing
authority prior to installation.
In restricted under–sink areas, it may be easier to
install the faucet first. Allow adequate tubing lengths
for any final component position.
A. Faucet Installation–The faucet contains an
anti–siphon air gap. While the system is
producing water, the drain water flows from the
RO, through the air gap and then to the
household drain. The purpose of the air gap is
to prevent water in the drain from backing up
into the RO Drinking Water System.
NOTE: For proper installation the Air Gap
Faucet has a critical level line “CL” marked on its
body and should be mounted so that the “CL” line
is at least one (1) inch (26mm) above the flood
rim of the sink.
The easiest installation is to use an existing spray
attachment hole. If the spray faucet hole is not
available, then the sink top must be drilled.
Choose a convenient location as described in
Sec. III, C.1, page 4.
1. Mark the location of the center of the faucet
base.
2a. Drilling a stainless steel sink:
•Center punch the hole to provide a starting
point for the drill.
•Start with a smaller drill as a pilot, and then
drill a ½" diameter hole to accept the bolt of
a 1¼" Greenlee Hole Punch (1¼" chassis
punch).
•Clean away any chips.
•Install the punch and tighten the nut to cut
the hole.
•Deburr any sharp edges.
2b. Drilling a porcelain sink:
It is best to use a special 1¼" diameter cutter
designed for porcelain. A carbide tipped
masonry bit is a second choice.
•Place a piece of tape over the area to be
drilled to help prevent chipping.
•Drill a pilot hole for the porcelain cutter. Use
the pilot drill supplied with the kit or a
carbide tipped drill.
•When drilling the 1¼" hole, drill slowly and
carefully, the porcelain chips easily.
•After drilling, clean the area well. Iron
filings, if left in place, can cause rust stains.
2c. Drilling a counter top:
NOTE: The counter top must be less than
1¼" thick. (See Sec. IV, A.2b, page 5.) Treat
ceramic tile as porcelain until the tile is
penetrated, then use the carbide tipped metal
cutter.
Formica counter tops may be drilled with a
good 1¼" wood bit, drilling a
3
/
32
" pilot hole
will help keep the bit going straight.
5