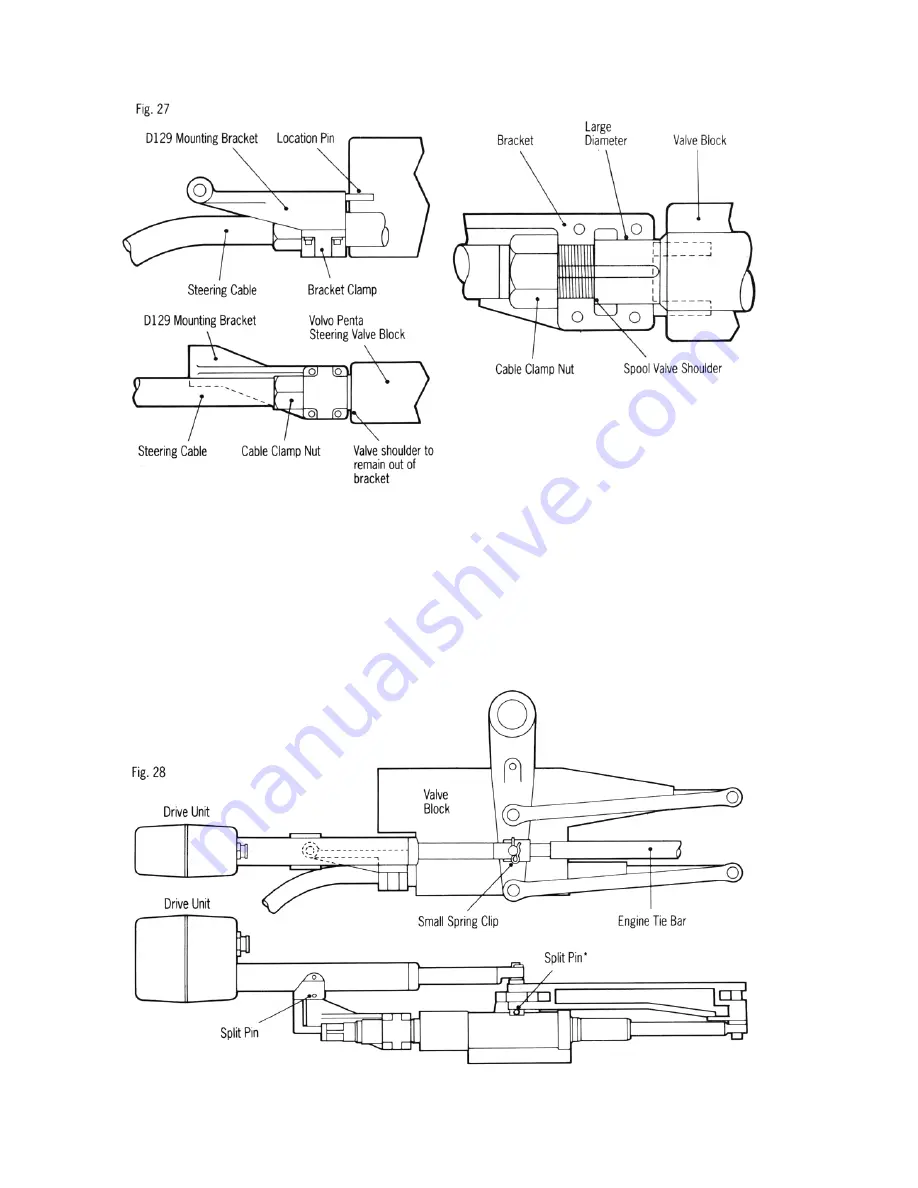
•
Uncouple the engine tie bar from the outdrive
tiller arm by bending back the lock tabs and
removing the cotter pin. This should be
replaced with the multi-engine adaptor pin,
ensuring that it is secured properly with a split
pin* (Fig.28) (on single engine installation, fit
the single engine adaptor pin in the vacant
middle hole in the tiller arm).
•
Attach the drive unit to the bracket using the
long cotter pin and split pin provided. The
small spring clip can then be used to attach
the drive unit to the adaptor pin (Fig. 28).
•
Slowly turn the steering system from hard
over to hard over.
It is most important that
the drive unit and the adaptor pin bracket
do not touch any part of the engine or
steering system.
23
Summary of Contents for ST7000
Page 1: ...ST7000 Installation...
Page 2: ...Autohelm Autohelm Autohelm Autohelm...
Page 3: ......
Page 5: ...1...
Page 13: ...8...
Page 51: ...46...
Page 52: ...47...
Page 53: ...44321 5 48...
Page 54: ......