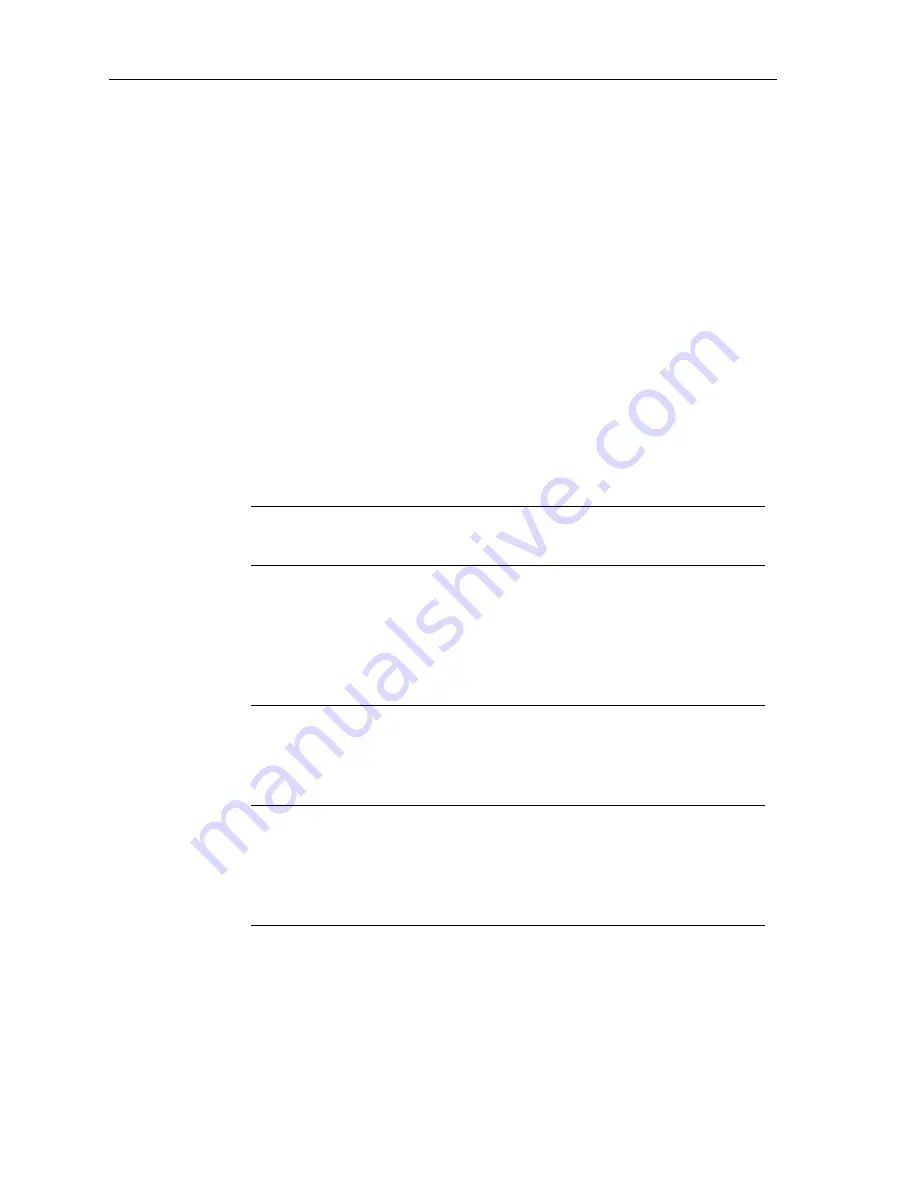
14
Rotary Drive - Installation Guide
Follow these steps to connect the rotary drive to the course computer:
1. Measure the total distance of cable run from the drive unit to the
course computer:
•
use Table 2 to identify the appropriate motor cable size
•
use at least 1.5 mm
2
(16 AWG) copper cable for the clutch
2. Join these cables to the drive cables using appropriate electrical
connectors or junction boxes at the correct power rating.
3. Route the cables back to the course computer, taking into account
the EMC installation guidelines (see page 6).
4. Connect the cables to the course computer (see Figure 8):
•
CLUTCH
terminals: red core to +ve, blue core to -ve.
•
MOTOR
terminals: at this stage you can connect either motor
cable to either terminal. You will check these connections
after installing the rest of the autopilot system.
Table 2: Recommended cable sizes
Cable length
(drive to course computer)
Cable gauge
(AWG)
Copper area
(mm
2
)
Type 1 drive
up to 3m (10ft)
up to 5m (16ft)
up to 7m (23ft)
up to 10m (32ft)
up to 16m (52ft)
14
12
10
8
6
2.5
4
6
10
16
Type 2 drive 12V
up to 5m (16ft)
up to 7m (23ft)
up to 16m (52ft)
10
8
6
6
10
16
Type 2 drive 24V
up to 3m (10ft)
up to 5m (16ft)
up to 10m (32ft)
up to 16m (52ft)
12
10
8
6
4
6
10
16