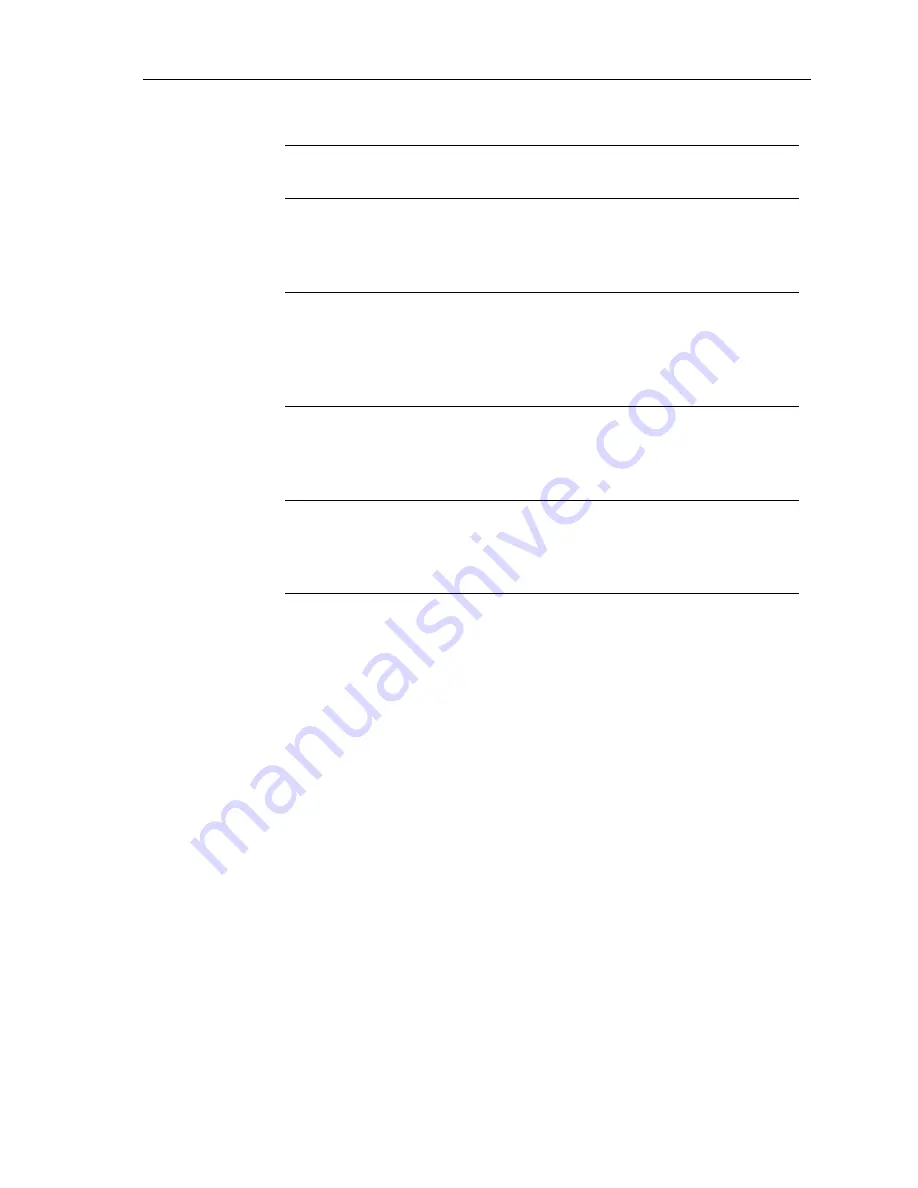
Hydraulic Linear Drive - Installation Guide
13
Connect the pump and ram to the course computer:
1. Measure the distance of cable run from the pump and ram to the
course computer:
•
use Table 2 to identify the appropriate motor cable sizes
•
use at least 1.5 mm
2
(16 AWG) copper cable for the clutch
2. Join these cables to the ones on the pump and ram using
appropriate electrical connectors or junction boxes at the correct
power rating.
Note: To meet current EMC legislation, you must NOT untwist the
pump cables, and you must NOT remove the suppression ferrite.
3. Route the cables back to the course computer, taking into account
the EMC installation guidelines (page 6).
4. Connect:
•
the cables from the pump to the
MOTOR
terminals on the
course computer (see Figure 9): at this stage you can connect
either motor cable to either terminal. You will check these
connections after installing the rest of the autopilot system.
•
the cables from the hydraulic ram to the
CLUTCH
terminals on
the course computer (see Figure 9): brown (+) and blue (-)
Table 2: Recommended cable sizes
Cable length
(pump to course computer)
Cable gauge
(AWG)
Copper area
(mm
2
)
Type 2 drive 12 V
up to 5 m (16 ft)
up to 7 m (23 ft)
up to 16 m (52 ft)
10
8
6
6
10
16
Type 2 drive 24 V
up to 3 m (10 ft)
up to 5 m (16 ft)
up to 10 m (32 ft)
up to 16 m (52 ft)
12
10
8
6
4
6
10
16
Type 3 drive 12 V
up to 5 m (16 ft)
up to 7 m (23 ft)
up to 16 m (52 ft)
8
6
4
10
16
25
Type 3 drive 24 V
up to 5 m (16 ft)
up to 7 m (23 ft)
up to 16 m (52 ft)
10
8
6
6
10
16