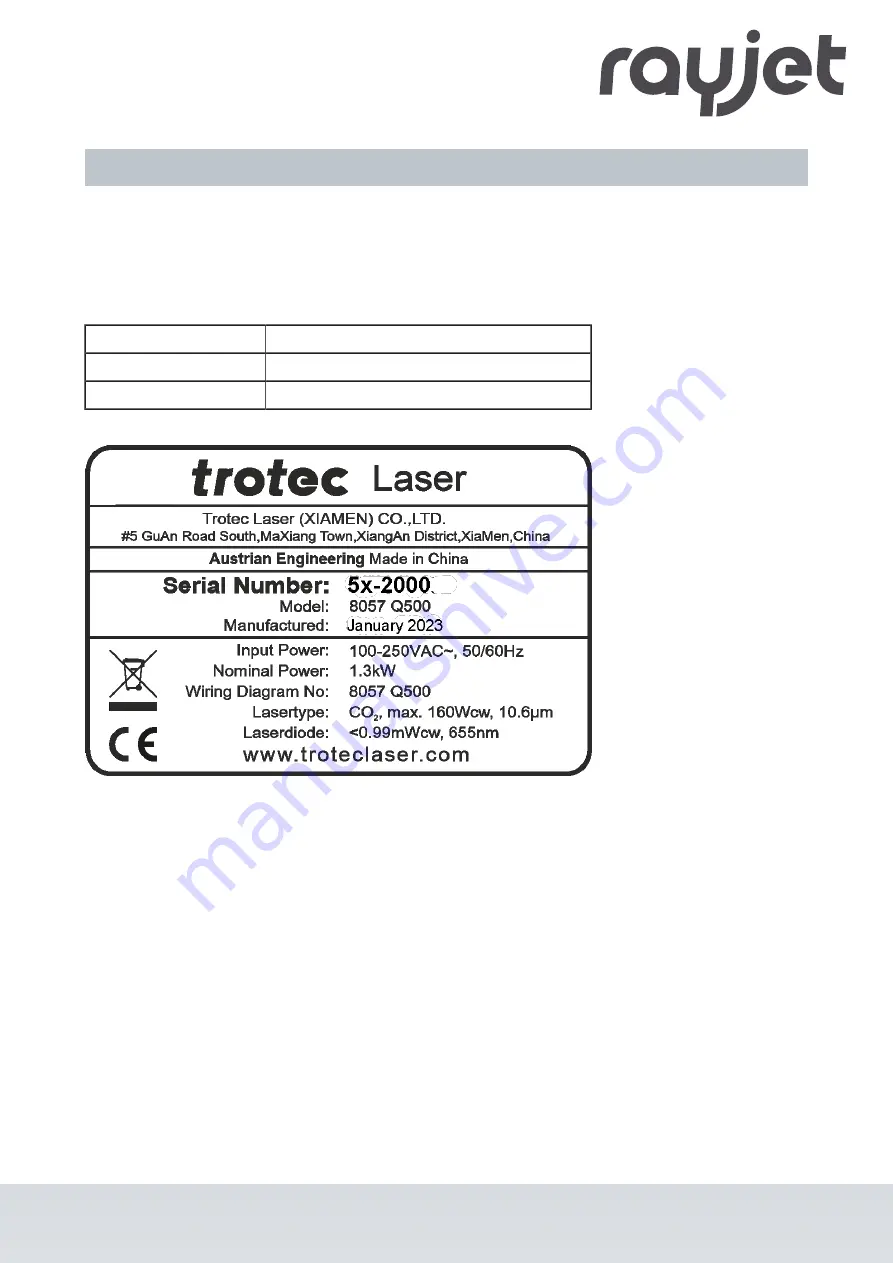
1.5 Type plate
The type plate with the CE mark is located on the rear of the machine.
Enter the serial number, model and year of manufacture into your manual and always refer to them when
contacting us for enquiries, troubleshooting or ordering of replacement parts.
Serial number:
Model:
Year of manufacture:
ENGLISH
ENGLISH
12 / 81
Summary of Contents for R500
Page 1: ...R500 Operation Manual 8057 Operation Manual 8057_4 0_EN 05 2023 ENGLISH...
Page 20: ...1 4 7 10 2 5 8 11 3 6 9 ENGLISH ENGLISH 20 81...
Page 46: ...7 Connect the water cooling system cable to the cooling alarm connection ENGLISH ENGLISH 46 81...
Page 75: ...13 Appendix ENGLISH ENGLISH 75 81...
Page 79: ......