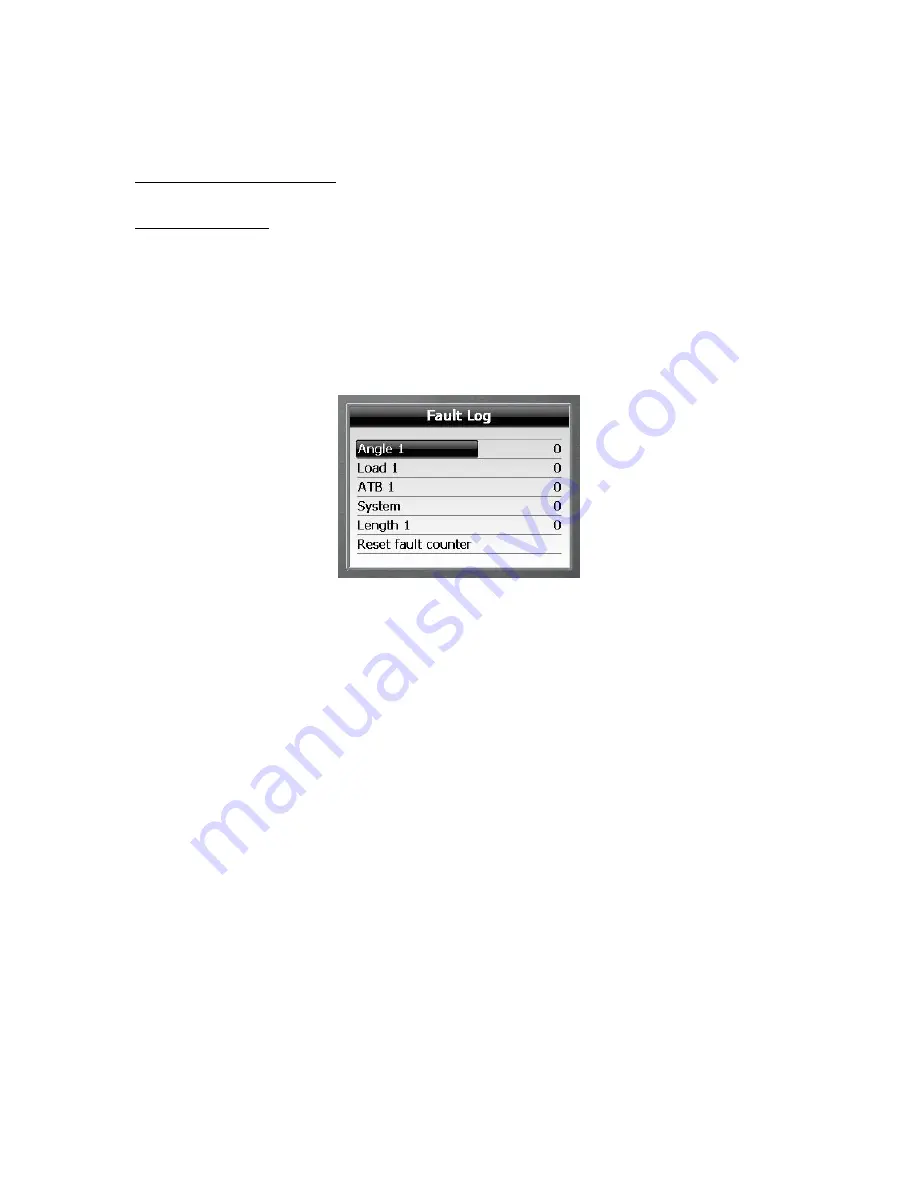
55M4000BCE00 REV A
31
4
AUTOMATIC LOGS
4.1 “Fault log”
The fault log screen is a diagnostic tool used to record intermittent errors detected in
various parts of the system. The numbers on the right hand side of this screen
represent a count of the number of individual faults detected for each component and
can be useful in tracing system faults.
Navigate through the calibration menu using
“
”
or
“
”
to highlight “View Fault Log”
and press
“
”
to enter.
Note the fault status, press
Escape
to return to the main calibration menu or select
“Reset fault counter” and press
“
”
to reset all the counters to zero.