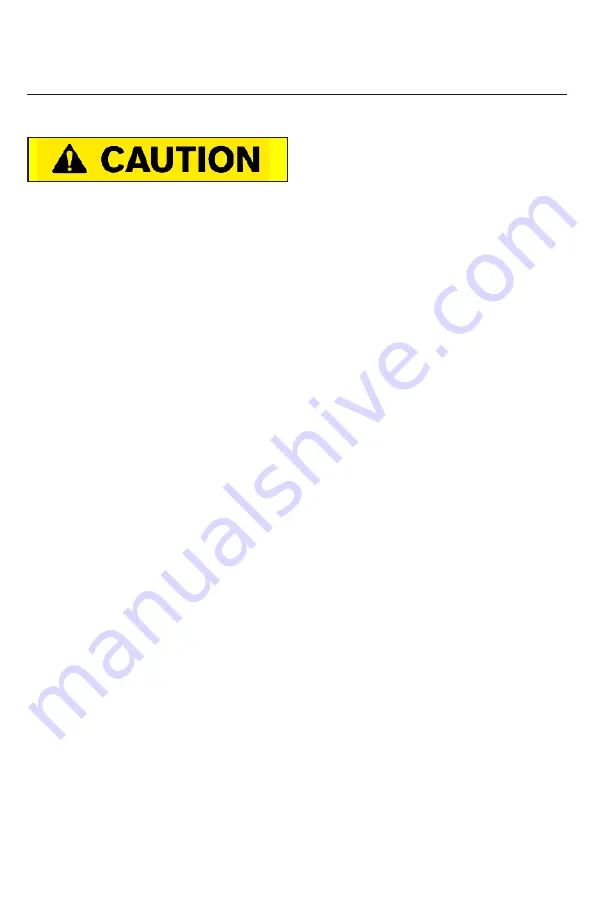
RG13II Operation • Maintenance • Parts
800.392.2686
15
Safety
verified to shut down the engine by the operator prior
to performing any work.
• CAUTION! FLYING DEBRIS!
NEVER stand or allow
anyone else to be directly in front of machine.
• Material being discharged from machine can cause
severe injury, blindness or death.
• Always operate this machine from the operator area.
Never stand directly in front of machine as flying objects
could be thrown during operation.
• Never move this machine, or make adjustments or repairs,
while the engine is running.
While Servicing and Performing
Maintenance on the Machine
• ALWAYS Block the wheels to prevent unintended
movement.
• Adhere to your LOCK-OUT/TAG-OUT procedure when
performing maintenance or repairs to this machine.
Locking and tagging out equipment safeguards
those working on equipment from being injured by its
unexpected energized or releasing stored energy.
• To prevent fires, clean debris and chaff from the engine
and muffler areas.
• Periodically check that all nuts and bolts, hose clamps,
and hydraulic fittings are tight.
• When removing the fuel cap, unscrew it slowly, and
hold it firmly. The cap may otherwise be thrown due to
pressure buildup caused by an increase in temperature.
• For your safety, repair or replace all damaged or worn
parts immediately. Replacement parts which are
authorized by Rayco are the only parts which should be
used for repair or replacement on this machine.
• Altering this equipment, or using this equipment in
such a way as to circumvent its design capabilities and
capacities, could result in serious injury or fatality and
WILL VOID THE WARRANTY.
• Do not alter this machine in any manner. Alterations
such as attaching a rope to the control bar may result
in personal injury or death.
• NEVER remove the cap from the hydraulic tank or
reservoir while the machine is running. Hot oil under
pressure will cause injury.
• Relieve hydraulic system pressure before repairing
or adjusting fittings, hoses, tubing, or other system
components.
Before Starting Engine
Start the engine only from the operator compartment. Never
short across the starter terminate or across the batteries.
Shorting could damage the electrical system by bypassing
the engine neutral start system.
Before you start the engine and before you move the machine,
make sure that no one is underneath the machine, around
the machine, or on the machine. Make sure that the area is
free of personnel.
Visibility Information
Before you start the machine, perform a walk-around
inspection in order to ensure that there are no hazards
around the machine.
While the machine is in operation, constantly survey the area
around the machine in order to identify potential hazards as
hazards become visible around the machine.
It may not be possible to provide direct visibility on large
machines to all areas around the machine. Appropriate job
site organization is required in order to minimize hazards that
are caused by restricted visibility. Job site organization is a
collection of rules and procedures that coordinates machines
and people that work together in the same area. Examples
of job site organization include the following:
• Safety instructions
• Controlled patterns of machine movement and vehicle
movement
• Workers that direct traffic to move when it is safe
• Restricted areas
• Operator training
• Warning symbols or warning signs on machines or
on vehicles
• A system of communication
• Communication between workers and operators prior
to approaching the machine
Modifications of the machine configuration by the user that
result in a restriction of visibility shall be evaluated.