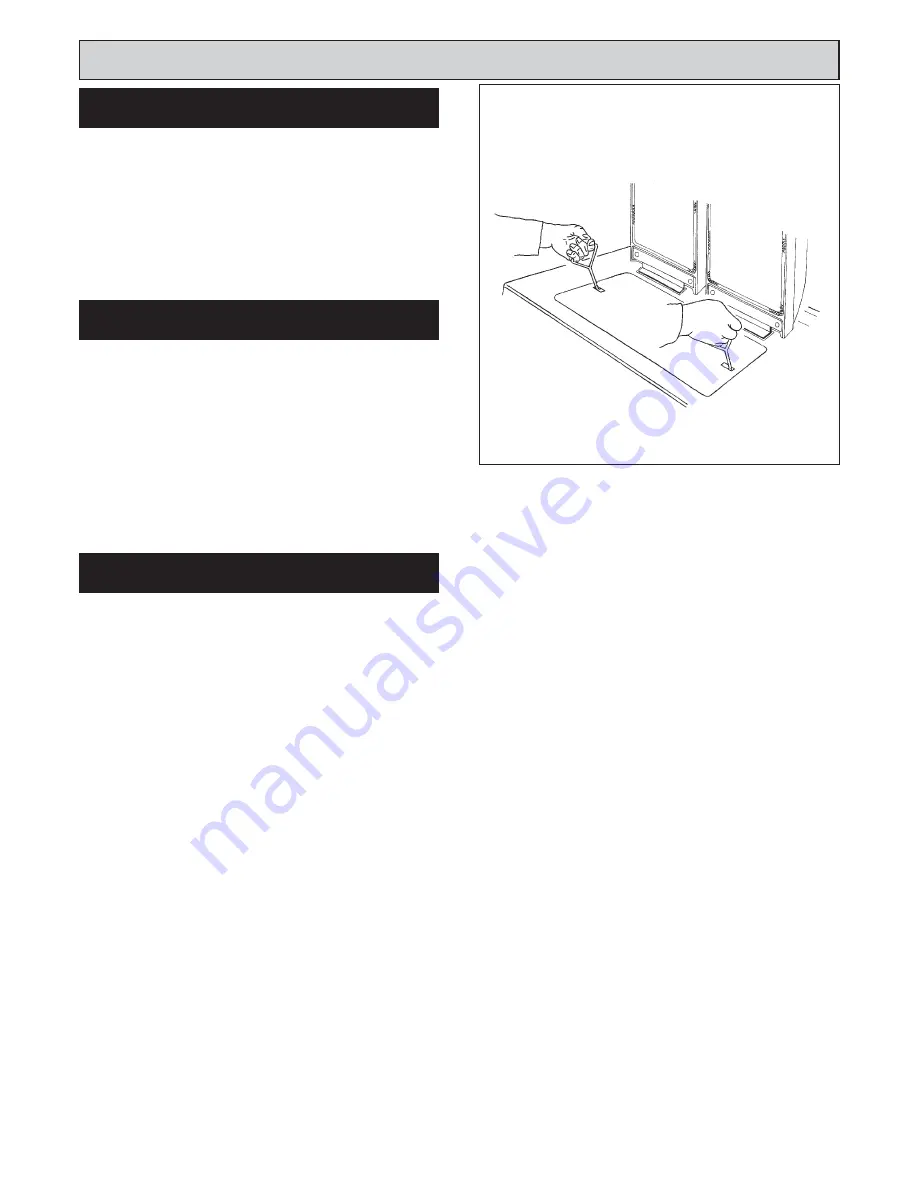
Operate the appliance and system, noting any faults
which may need to be corrected during service.
WARNING: ISOLATE UNIT FROM ELECTRICITY
SUPPLY AND TURN OFF GAS AT SERVICE COCKS
BEFORE SERVICING. AFTER COMPLETING SERVICE
ALWAYS CHECK FOR GAS SOUNDNESS AND CHECK
THIS FUNCTION OF CONTROLS.
Lift out the hotplate using lifting tools provided. Brush the
fins with a wire brush to remove any deposits.
SEE FIG. 7
1.
Open up the bottom burner access door.
2.
Remove the 3 plinth securing screws and remove
plinth.
16
Servicing
PRE-SERVICE CHECK
FIG. 12
HOTPLATE CLEANING
SEE FIG. 12
BURNER ACCESS
DESN 510145 A