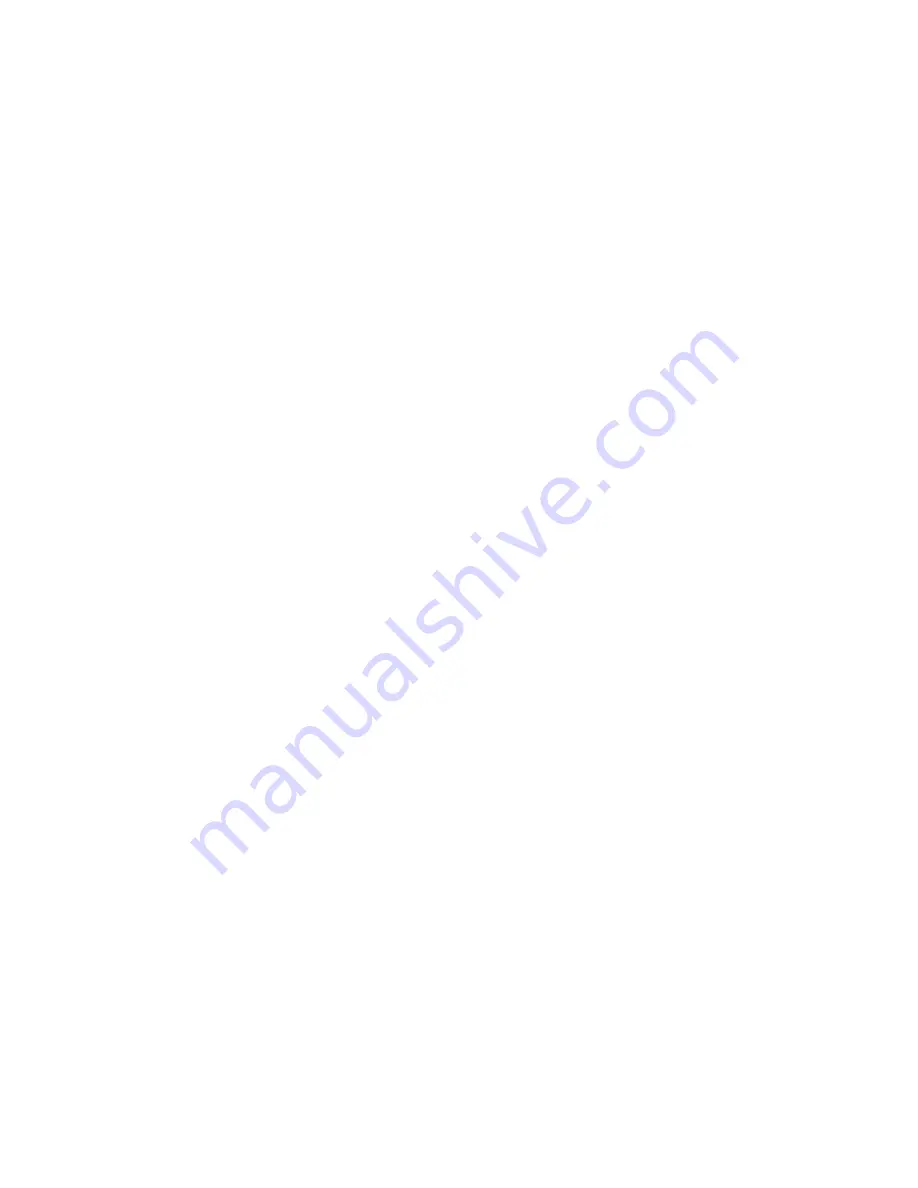
Reference key of system declaration of conformity
1.
Like in the case of gas plants, by “other” we may mean the replacement of a device installed in
a fixed manner.
2.
Indicate: name, surname, qualification and (when there is an obligation as per Art.5, paragraph 2)
registration data to the relative Professional association of the technician that drafted the project.
3.
Specify the technical standards and regulations in force, classifying them per design, execution
and inspection.
4.
Should the system executed according to the design be modified during work, the project submit-
ted at the end of the works should include the versions made. The project also includes the fire
prevention protocol (where applicable).
5.
For products subject to standards, the report should contain a complete statement of compliance
to the same, where applicable, with reference to marking, test certificates etc. issued by author-
ized bodies. For the other products (to be listed) the signatory should declare that it regards materi-
als, products and parts compliant with the provisiong og Articles 5 and 6. The report should state
the compliance with installation area. When this is relevant for the proper operation of the system,
indications on the number or features of appliances installed or about to be installed should be
provided (e.g. for gas: 1) number, type and power of appliances; 2) features of the parts that make
up the ventilation systems of the area; 3) features of the system that feeds the fuels; 4) information
on appliance wiring, where applicable).
6.
The layout of the system executed includes the description of the works done (with simple refer-
ence to the project when the latter was drawn up by an authroized professional and variations
during works have not been approved). In the case of: modification, enlargement and non-routine
maintenance, the intervention should be integrated, if possible, into the layout of the existing
system. The layout shall include the fire prevention protocol (where applicable).
7.
The reference data include the name of the company that carried out the works and the date of the
statement. For plants or parts of plants built before the entry into force of this decree, the reference
to declarations of conformity may be replaced by a reference to declarations of conformity (Article
7, paragraph 6). If part of the system is executed by another company (such as ventilation and
fume exhaust in gas installations), the declaration should include reference data for the said parts.
8.
If the installation includes products or systems legitimately used for the same job in another Mem-
ber State of the European Union or party to the Agreement on the European Economic Area, for
which there are no technical standards for the product and installation, the declaration of conform-
ity should be annexed to the project drafted and signed by a registered professional engineer in
accordance with the specific technical skills required, certifying that the risk assessment associ-
ated with the use of the product or production system was performed, and the fact that he had
adopted all necessary measures to achieve levels of safety equivalent to those guaranteed for the
installations carried out, according to sate-of-the-art standards and to have supervised the proper
execution of the installation in all its phases in compliance with all technical standards provided by
the manufacturer of the system or the product.
9.
Example: any certificates containing the outcome of the checks performed on the system before
commissioning or cleaning, sanitizing treatments etc..
10.
Upon completion of works, the company that installed the system should issue the client a declara-
tion of conformity of the systems in compliance with the standards in Art.7. The client or the owner
should entrust installation, modification, enlargement and maintenance tasks of the system in Art.
1 exclusively to authorized companies as per Art. 3.
Summary of Contents for o-ring
Page 1: ...en USER MANUAL O RING...
Page 2: ......
Page 32: ...Note...
Page 33: ...Note USER MANUAL O RING 33...
Page 34: ...Note 34...
Page 35: ......