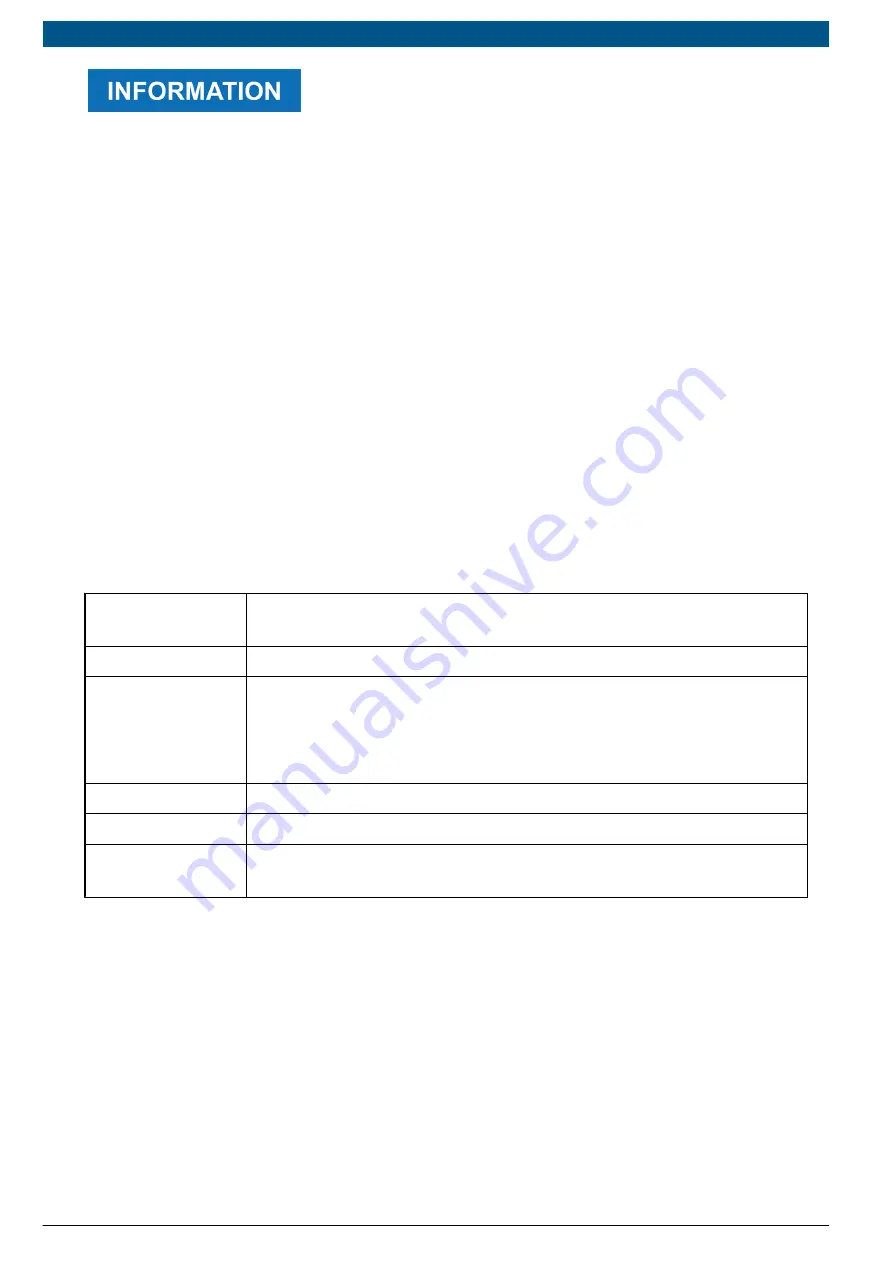
The correct level of the pump oil is at approximately half of the
graduated scale on the pump oil level sight.
The total amount of oil to insert is approximately 370 ml.
10. Tighten the oil filler cap.
11. Make sure there are not any leaks from the side of the drain cap or from the filter.
12. Remount the side panel.
13. Connect the equipment from the mains.
14. Turn on the equipment.
15. Select: ADDITIONAL FUNCTIONS > TOTAL AND RESETTABLE COUNTERS
16. Locate the item: PUMP TIME
17. Press: RESET
17.3 Replacing the Paper in the Printer
Follow the instructions provided in the chapter
Replacing the Paper in the Printer.
17.4 Periodical Checks
In order to guarantee a correct operation of the device we recommend you check the parts
that are the most subject to wear on a regular basis.
Parts subject to
wear
Check
Service hoses
Make sure there are no cuts, scratches or bulges.
Quick fittings
Make sure there are no signs of wear and that the hoses do not harden
during use.
Make sure the service hoses are connected properly.
Make sure there are no cuts or scratches on the O-rings.
Oil and UV bottles
Make sure they are clear and not damaged.
Wheels
Make sure the brakes are working properly.
Power supply
cable
Make sure there are no cuts, scratches or burns.
en | 43 | YUCON |
Ravaglioli
| 2024-03-01