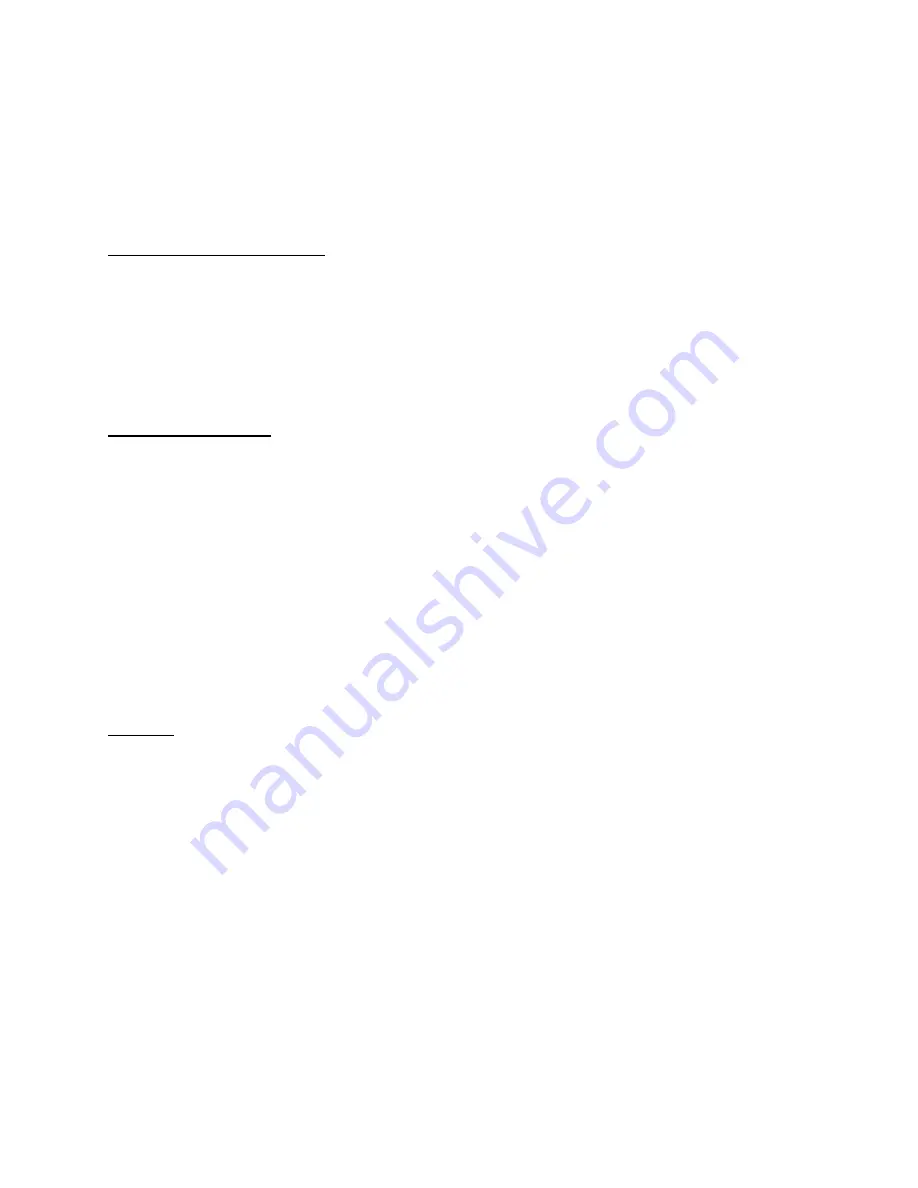
09/11/2018
RANS S-21 OUTBOUND
TEXT MANUAL
14-18
(6)
As rotation stops, neutralize rudder and apply back pressure on the
control stick to slowly reduce airspeed to normal cruise speed.
IGNITION MALFUNCTION
A sudden engine roughness or misfiring is usually evidence of ignition problems.
Switching from BOTH to either L or R ignition switch position will identify which circuit is
malfunctioning. Select different power settings if continued operations on BOTH circuits
is practicable. If not, switch to the good circuit and proceed to the nearest airport for
repairs.
CARBURETOR ICE
NOTE:
Actuation only applies if Carburetor Heat is installed on your aircraft. If
carburetor ice is experienced, transit to an area with less possibility of carburetor ice
forming.
A sudden engine roughness or loss of rpm could be carburetor ice problems. Actuate
the Carburetor Heat switch.
As soon as the engine roughness or suspected carburetor ice is gone, turn off the
Carburetor Heat. Repeat as necessary.
DOORS
The S-21 OUTBOUND can be flown with the doors open, up to and including 100 mph.
The S-21 OUTBOUND doors should not be opened at airspeeds above 65 mph.
The S-21 OUTBOUND can be flown with (1) or both doors removed up to 100 mph.
A loss in L & D, climb, and cruise speed is to be expected with the doors open or off
Doors can open in flight if the latches are not secured.
CAUTION:
If any door opens in flight, continue to fly the plane, trim to hands-off level
flight if possible, slow to 65 mph, then close door.
The aircraft will fly with open doors. The door will float in a position pending on
the speed of the aircraft. To close an open door in flight, slow to 65 mph, push the
opposite rudder pedal. This will make the aircraft yaw and help to get the door
closed.