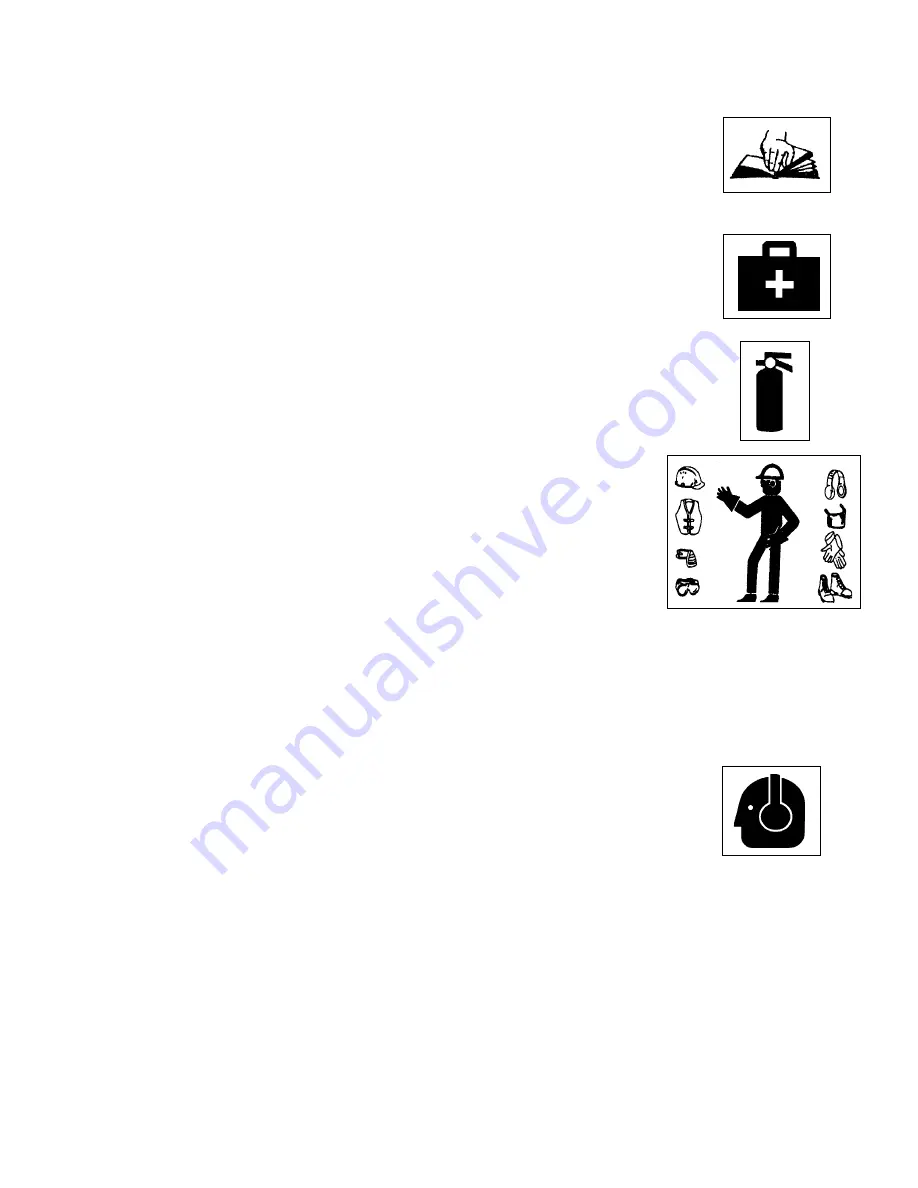
1.
Read and understand the
Operator’s Manual and all
safety signs before operating,
maintaining or adjusting the
Quick-Attach Bucket Forks.
3
2.1 GENERAL SAFETY
2.
Have a first-aid kit available
for use should the need
arise and know how to use
it.
3.
Have a fire extinguisher
available for use should the
need arise and know how to
use it.
4.
Wear appropriate
protective gear. This
list includes but is not
limited to:
-
A hard hat
-
Protective shoes
with slip resistant
soles
-
Protective goggles, glasses or face shield
-
Heavy gloves
-
Protective clothing
5.
Install and secure all guards before starting.
8.
Lower bucket/forks to the ground, set park
brake, remove ignition key and wait for all
moving parts to stop before servicing, adjust-
ing and repairing.
9.
Clear the area of people, especially small
children, before starting.
10. Review safety related items annually with all
personnel who will operating or maintaining
the Quick-Attach Bucket Forks.
6.
Do not allow riders.
7.
Wear suitable ear protection
for prolonged exposure to
excessive noise.
SAFETY
YOU
are responsible for the
SAFE
operation and
maintenance of your Quick-Attach Bucket Forks.
YOU
must ensure that you and anyone else who
is going to operate, maintain or work around the
Forks be familiar with the operating and mainte-
nance procedures and related
SAFETY
informa-
tion contained in this manual. This manual will
take you step-by-step through your working day
and alerts you to all good safety practices that
should be adhered to while operating the Forks.
Remember,
YOU
are the key to safety. Good
safety practices not only protect you but also the
people around you. Make these practices a
working part of your safety program. Be certain
that
EVERYONE
operating this equipment is
familiar with the recommended operating and
maintenance procedures and follows all the safety
precautions. Most accidents can be prevented. Do
not risk injury or death by ignoring good safety
practices.
•
Fork owners must give operating instructions
to operators or employees before allowing
them to operate the machine, and at least
annually thereafter per OSHA (Occupational
Safety and Health Administration) regulation
1928.57.
•
The most important safety feature on this
equipment is a
SAFE
operator. It is the
operator’s responsibility to read and under-
stand
ALL
Safety and Operating instructions
in the manual and to follow these. Most
accidents can be avoided.
•
A person who has not read and understood all
operating and safety instructions is not quali-
fied to operate the machine. An untrained
operator exposes himself and bystanders to
possible serious injury or death.
•
Do not modify the equipment in any way.
Unauthorized modification may impair the
function and/or safety and could affect the life
of the equipment.