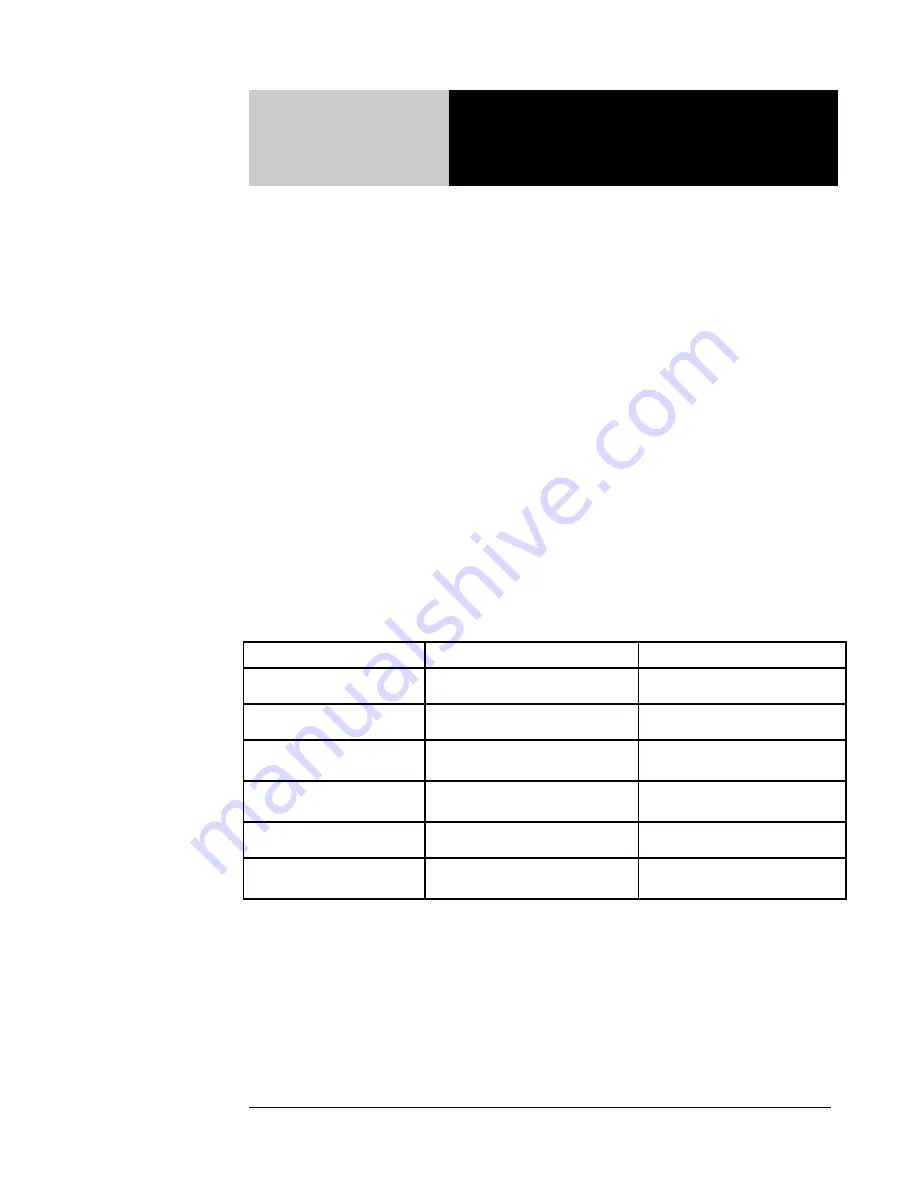
difoodservice.com
13
Preventive Maintenance
Randell strongly suggests a preventive maintenance program which would include
the following
Monthly
procedures:
1. Cleaning of all condenser coils. Condenser coils are a critical component in the
life of the compressor and must remain clean to assure proper air flow and heat
transfer.
Failure to maintain this heat transfer will affect unit performance and
eventually destroy the compressor. Clean the condenser coils with coil cleaner
and/or a vacuum, cleaner and brush.
NOTE: Brush coil in direction of fins, normally vertically as to not damage or
restrict air from passing through condenser.
2. Clean fan blade on the condensing unit.
3. Clean and disinfect drains with a solution of warm water and bleach.
4. Clean and disinfect drain lines and evaporator pan with a solution of warm water
and bleach.
5. Clean all gaskets on a weekly if not daily basis with a solution of warm water
and a mild detergent to extend gasket life.
NOTE: DO NOT USE SHARP UTENSILS.
RECOMMENDED CLEANERS FOR YOUR STAINLESS STEEL INCLUDE THE
FOLLOWING:
JOB
CLEANING AGENT
COMMENTS
Routine cleaning
Soap, ammonia, detergent
Medallion
Apply with a sponge or cloth
Fingerprints and smears
Arcal 20, Lac-O-Nu,
Ecoshine
Provides a barrier film
Stubborn stains and
discoloration
Cameo, Talc, Zud, First
Impression
Rub in the direction of the
polish lines
Greasy and fatty acids,
blood, burnt-on foods
Easy-Off, Degrease It, Oven
Aid
Excellent removal on all
finishes
Grease and Oil
Any good commercial
detergent
Apply with a sponge or cloth
Restoration/Preservation
Benefit, Super Sheen
Good idea monthly
Reference: Nickel Development Institute, Diversey Lever, Savin, Ecolab, NAFEM.
NOTE: Do not use steel pads, wire brushes, scrapers, or chloride cleaners
to clean your stainless steel.
CAUTION:
DO NOT USE ABRASIVE
CLEANING
SOLVENTS,
AND
NEVER
USE
HYDROCHLORIC
ACID
(MURIATIC ACID) ON STAINLESS STEEL.
NOTE:
Do not pressure wash equipment as damage to electrical
components may result.
Summary of Contents for PH120E2-220
Page 2: ......
Page 4: ......
Page 17: ...difoodservice com 15 Electrical Diagram ...
Page 19: ...difoodservice com 17 Replacement Parts List Pizza Hut Maketable PH120E2 ...
Page 20: ...18 800 621 8560 ...