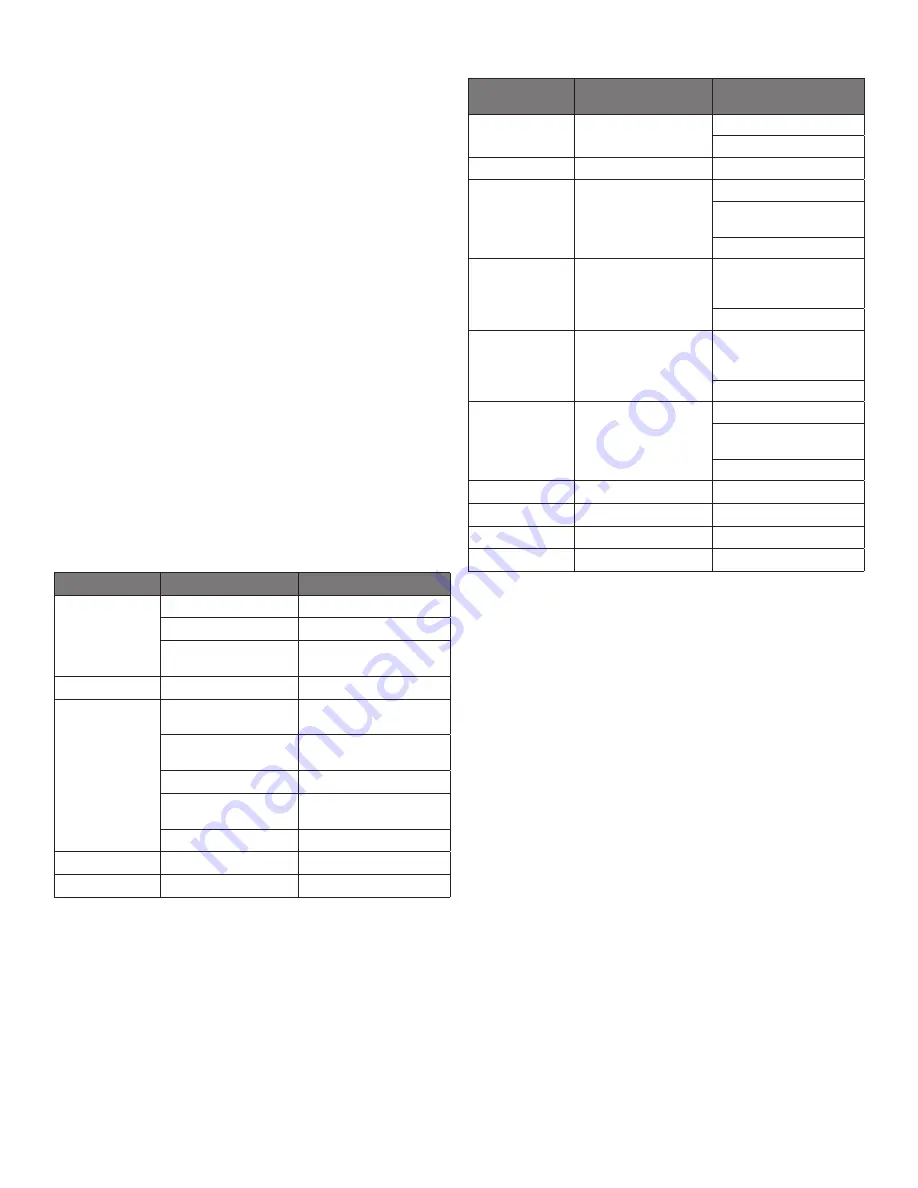
5
OM-8000 & 9000W SERIES PREP TABLES
For more information on preventive maintenance, consult your local service
company or CFESA member. Most repair companies offer this service at very
reasonable rates to allow you the time you need to run your business along with
the peace of mind that all your equipment will last throughout its expected life.
These services often offer guarantees as well as the flexibility in scheduling or
maintenance for your convenience. For a complete listing of current Unified Brands
ASA please visit www.unifiedbrands.net.
Unified Brands believes strongly in the products it manufactures and backs those
products with one of the best warranties in the industry. We believe with the
proper maintenance and use, you will realize a profitable return on your investment
and years of satisfied service.
REPLACEMENT PARTS
To order parts, contact your Authorized Service Agent. Supply the model
designation, serial number, part description, part number, quantity, and when
applicable, voltage and phase.
CONTACT US
If you have questions pertaining to the content in this manual, contact Unified
Brands at 888-994-7636 or [email protected].
TROUBLESHOOTING
This unit is designed to operate smoothly and efficiently if properly maintained.
However, the following is a list of checks to make in the event of a problem. Wir-
ing diagrams are found at the end of this manual. When in doubt, turn unit off
and contact service at 888-994-7636 or [email protected].
SYMPTOM
POSSIBLE CAUSE
PROCEDURE
Unit does not run
No power to unit
Plug in unit
Control in OFF position
Turn controller on
Faulty control
Call for service at 888-994-
7636
Unit too cold
Incorrect set point
Adjust control set point
Unit too warm
Door / drawer ajar
Ensure door / drawer is fully
closed
Gasket torn or out of place
Inspect the gasket for wear
and position
Incorrect set point
Adjust control set point
Warm product introduced
to cabinet
Pre-chill product 37ºF
Ice on the coil
Initiate manual defrost
Unit noisy
Ice on the coil
Initiate manual defrost
Unit does not defrost Excessive ice on the coil
Initiate manual defrost
DANFOSS CONTROLLER CODES
DISPLAYED
ALARM CODE
ALARM
ACTION
Hi
High Temperature Alarm
Inspect door/drawer sealing
Contact service
Lo
Low Temperature Alarm
Contact service
CON
Condenser Temperature
High Limit
Clean condenser coil
Inspect coil for any objects
obstruction hindering airflow
Contact service
uHi
Line Voltage Too High
Verify voltage of power source,
to be performed by qualified
technician
Contact service
uLi
Line Voltage Too Low
Verify voltage of power source,
to be performed by qualified
technician
Contact service
LEA
Continuous Compressor
Runtime
Inspect door/drawer sealing
Inspect condenser coil, clean if
necessary
Contact service
E01
S1 Sensor Failure
Contact service
E02
S2 Sensor Failure
Contact service
E03
S3 Sensor Failure
Contact service
E04
S4 Sensor Failure
Contact service