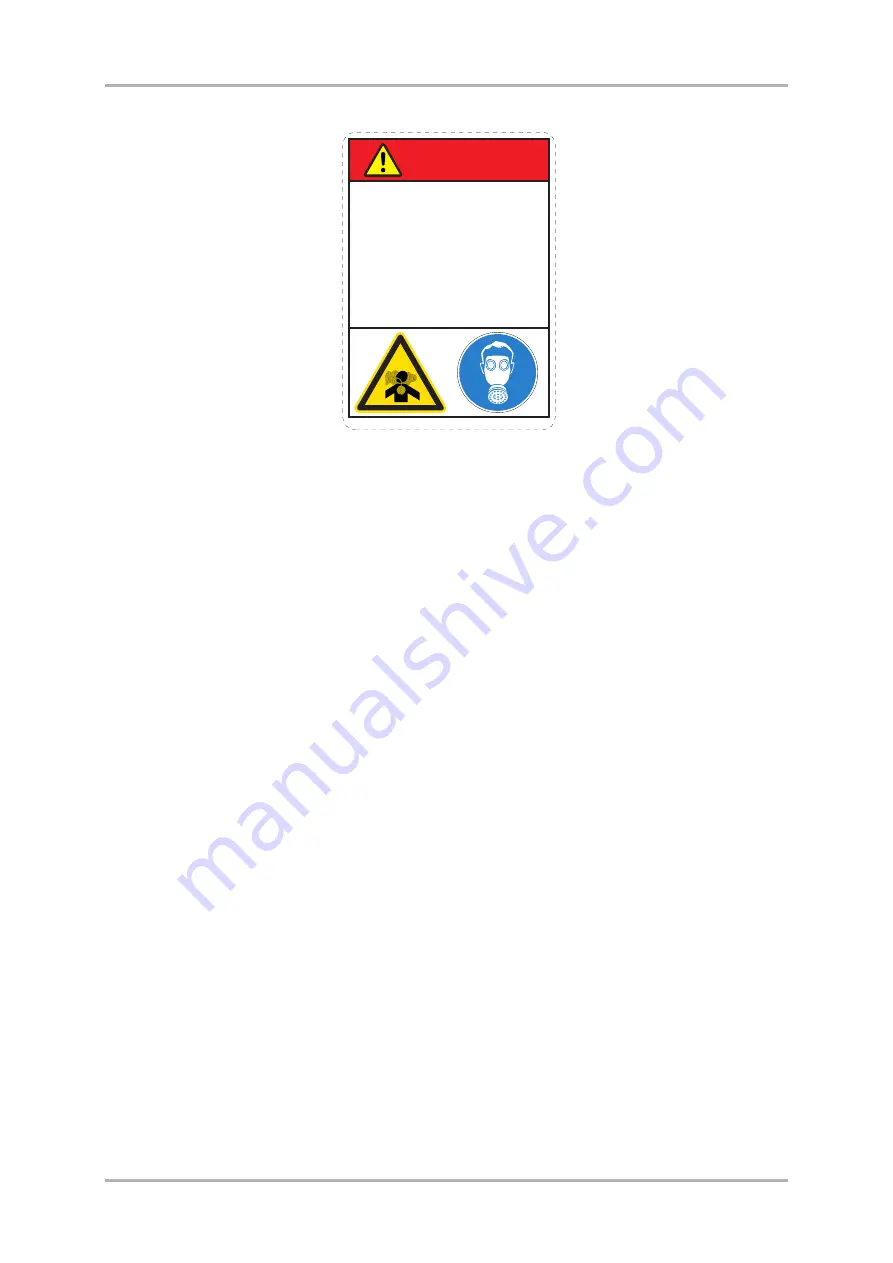
COPYRIGHT © 2019 SANDVIK MINING AND CONSTRUCTION OY
Page 16 - Operation
Safety
RPV14R, RPV22R, RPV29R, RPV39R, RPV53R, RPV75R
Airborne pollutants are microscopic particles, which will damage your health when
inhaled. Aiborne pollutants on construction sites can be for example silica dust, oil
fumes or diesel exhaust particles, visible or invisible. Especially in demolition sites,
there may be other dangerous substances, such as asbestos, lead paints or other
chemical substances.
The effect of airborne pollutants may be immediate if the substance is poisonous.
The main danger with airborne pollutants comes from long term exposure, where
particles are inhaled but not removed from the lungs. The disease is called silicosis,
asbestosis or other, and will result in death or serious injury.
To protect yourself from airborne pollutants, always keep excavator doors and
windows closed during operation. Excavators with pressurized cabins should be
utilized in product operation. Proper maintenance of fresh air filters of the excavator
is essential. Where pressurized cabins are not available, proper respirators must be
utilized.
Stop working when bystanders are in the area of airborne pollutants and make sure
they have proper respirators. Respirators are as important for bystanders as hard
hats.Respirators for both operator and bystanders must be approved by the
respirator manufacturer for the application in question. It is essential that the
respirators protect from the tiny dust particles which cause silicosis and which may
cause other serious lung diseases. Do not use the product until you are sure the
respirators are working properly. This means each respirator must be checked to
make sure that it is clean, that its filter has been changed, and to otherwise make sure
the respirator will protect in the way it is meant to.
Always make sure dust has been cleaned off your boots and clothes when you leave
your shift. The smallest particles of dust are the most harmful. They may be so fine
that you cannot see them. Remember, you MUST protect yourself and bystanders
from the danger of breathing or inhaling dust.
Always follow local laws and regulations for airborne pollutants in the working
environment.
R010
3
49
DUST HAZARD
Breathing dust will cause death
or severe injury.
Always wear approved
respirator.
DANGER
169410_ENG-1