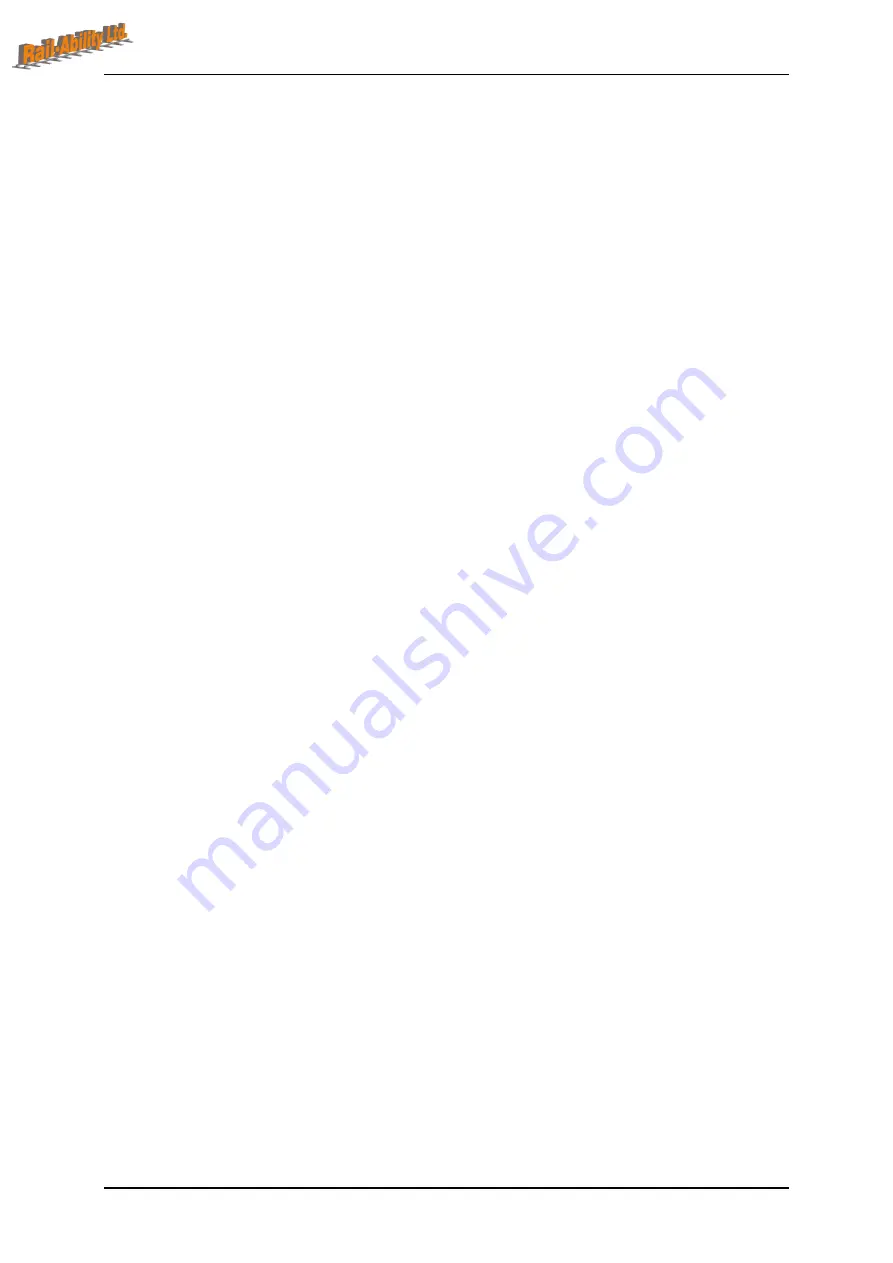
Operator’s Manual
© Copyright 2018 - Rail-Ability Limited
Page
25
of
71
Conversion
•
Do not exceed 10 km/h (6 mph).
•
Use the appropriate number of people and proper lifting techniques when lifting the tow bar.
•
The tow bar must remain with the machine at all times and must never be removed unless when
actually towing.
If the main hydraulic pump is not functioning, use the Electric Power option as detailed below.
10.3.2 Electrical Power
In case of failure of the main hydraulic pump or engine failure:
•
Raise the rail gear using the Battery Driven Pump with cab Levers detailed previously.
•
Use the Rail Gear Recovery Controls in order to Off-Track the machine.
10.4 Emergency Off Tracking
EMERGENCY ON-TRACKING IS NOT COVERED IN THIS MANUAL AS THERE IS NO OCCASION
WHEN THIS PROCEDURE WOULD NORMALLY BE CONDONED.
Emergency Off-Tracking however may be necessary at some point. It must be stressed that this is an
Emergency Procedure Only
and should
NOT
be used for normal operation. If you are asked to Off-
Track using this method (at an unprepared location) without suitable justification you should report to
your On-call Manager and ask their advice before attempting this manoeuvre.
Carry out the preparation below, then the procedure.
10.4.1 Preparation
If there is real cause to use this method there are still certain procedures that must be followed:
•
The Off-Tracking area must be inspected for its suitability as normal.
•
An area where there are no obstructions should be selected. For example, there should be no
conductor rail present, no high ballast shoulders and no obvious hazards.
•
Emergency Off-Tracking must not be carried out on a cant.
•
Emergency Off-Tracking must not be undertaken with attachments other than a bucket.
10.4.2 Procedure
This procedure requires 2 trained and competent personnel and may take 15 minutes to execute on
average under normal circumstances.
In the event of a real emergency the procedure for Emergency Off-Tracking is as follows:
•
Ensure the machine is configured for travel (boom fully stowed).
•
Approach the Off-Tracking area at a safe speed.
•
Sound the horn to alert personnel at the Off-Tracking area as you approach.
•
Raise the front and rear rail gear fully.
•
Turn the machine keeping the tracks on the railhead.
•
Manoeuvre the machine on the railhead until the machine is perpendicular to the rail.
•
Slowly track the machine clear of the running rail.
•
Move the machine at least 3 metres from the closest rail.
When carrying out this operation always follow any hand signals given by a ‘banksman’ or machine
controller and carry out all movements smoothly and at a safe speed. The machine is fitted with an offset
boom and the arm must be centred to avoid causing instability or a possible tip-over situation occurring.
Ensure you are clear of all obstructions.
Ensure the machine is configured to travel to avoid causing instability or a possible tip over situation
occurring.