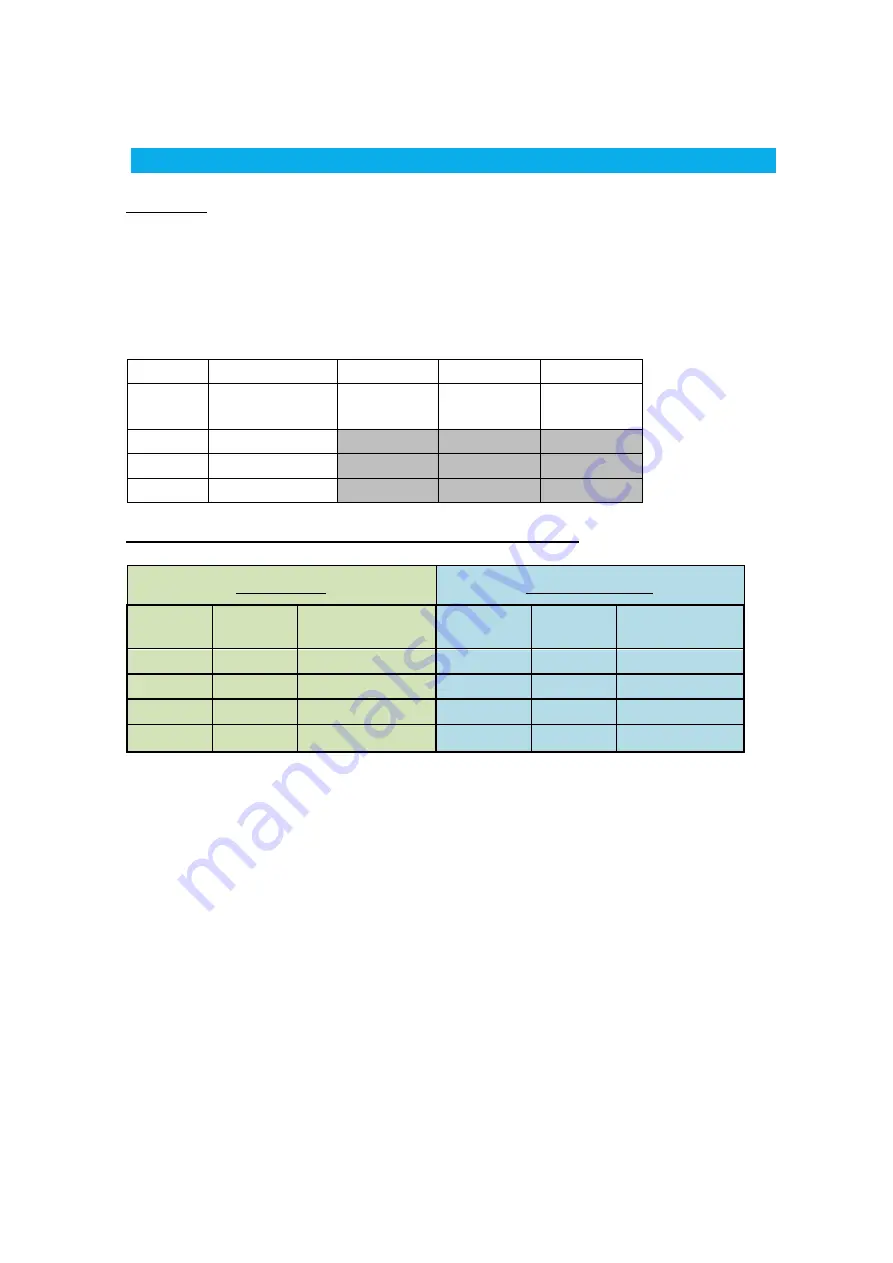
Page 3
Leaving the RTM300 sensor connected whilst conducting a 500v insulation
(Megger) test will damage the sensor’s internal electrical components
rendering it unusable and invalidating any existing warranty.
6
INSTALLATION
CAUTION Ensure that all proper safety precautions are taken. Observe all
National and Customer codes of conduct and procedures whilst working on
any street furniture. Provisions should be made to ensure safe operation of
the crossing/junction at all times.
Confirm the operational modes required and set the front panel switches and
jumpers J1-4 of the RTM500 interface card accordingly.
Jumper Function
Fitted
Not Fitted
Notes
1
Output mode
Low
power
Fail safe
(TR2512)
Issue 3
and below
2
Not used
3
Not used
4
Not used
RTM500 Sensitivity & Presence Time Switch Settings
Sensitivity
Presence Time
S1
S2
P1
P2
0
0
LOW
0
0
CH OFF
1
0
MED LOW
1
0
3s
0
1
MED HIGH
0
1
4min
1
1
HIGH
1
1
35min
NOTE: This equipment is fitted with overvoltage protection to minimise the
disruption that may be caused by induced voltages from lightning or other
environmental effects.
6.1 INSTALLATION OF THE RTM300 SENSOR
6.1.1 The installation of the RTM300 sensor presumes that a suitable duct has
been installed, has sufficient capacity and is accessible. Where more than
one sensor is to be installed in the same duct, install the furthest sensor first
and work progressively to the nearest sensor.
Further information on the installation of ducts can be found in Appendix 3.
6.1.2 Attach a sufficiently long and suitable (e.g polypropylene) draw cord to the
attachment point on the sensor. Using the site plans or by measurement
along the kerb at 90° and at 45° (see figure 1 below) find the distance to the
white line. Half of this is the mid lane distance. Add on the set back of the
duct end in the pit from the kerb line to get the distance that the sensor has to
be pushed out. Measure off this distance on the draw cord and mark it using
suitable tape.