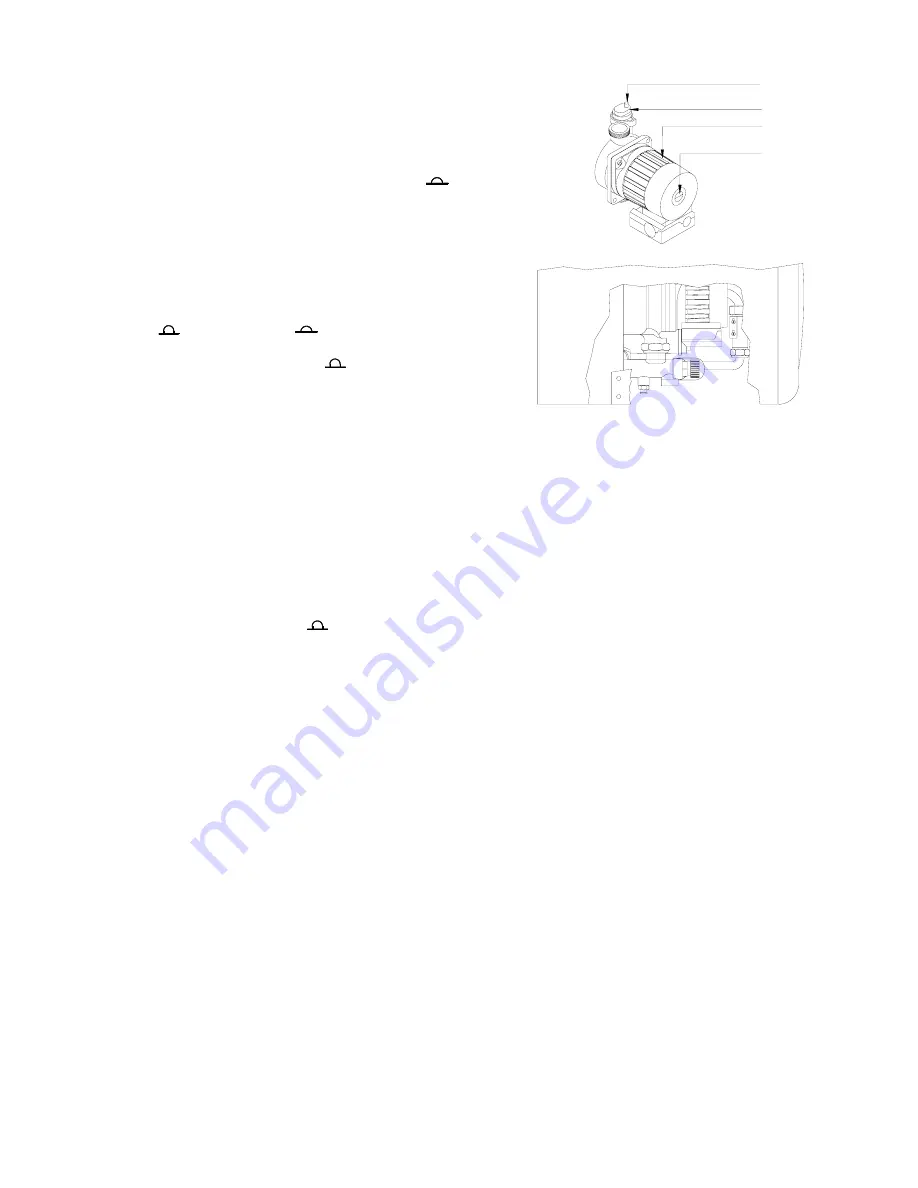
Installation Manual
DOMESTIC HOT WATER WITH STORAGE CYLINDER – TA05A027.A0504
14
•
check the pressure in the system: if this has gone down, comes on restore
pressure
;
AIR VENT VALVE CAP
CIRCULATING PUMP
RS
AIR VENT VALVE
PUMP CAP
•
close the tap on the filling loop once this operation is completed
;
Starting up the boiler
•
turn on the gas cock situated under the boiler grill;
•
set the ON/OFF button (1) (see fig.1 pag. 12) to ON position
;
Fig. 1
•
make sure that no flashing value is on the display (14); if value 04 is flashing
and no.8 light is ON it means water deficiency in the system: open the filling
tap on the filling loop and fill the system
until a pressure of 1.5 bar has been
reached (light no.11 ON) and then
close the tap on the filling loop
;
•
the automatic ignition system will turn the burner on;
•
should the boiler fail to ignite: if the display (14) shows value 04 flashing, it is
necessary to repeat the procedure of filling the system; if the display (14)
shows value 01 flashing
wait 3 minutes;
set the ON/OFF button (1) to OFF
position
and then ON position
(fig.1). It may be necessary to repeat
the procedure a few times to purge air from the pipes;
•
set ON/OFF switch (1) in OFF position
(fig.1 page 12), insert a gauge
into the pressure point no.4 (fig.2 page 14). Turn ON the boiler and check the
minimum and maximum gas pressure setting in accordance with values
stated on the gas data plate (to check maximum gas pressure value, turn ON
a hot water tap and check that the maximum pressure is equal to that stated
on the gas data plate; to check the minimum gas pressure, close the hot
water tap, and select WINTER mode, the pressure gauge will show the minimum gas pressure value for 10 seconds. If the pressure
values are not the same as those stated on the gas data plate, calibrate pressure again;
Fig. 2
•
once the calibration procedure has been completed, unplug the mains lead or turn off the mains switch, close the gas cock and remove
the gauge from the pressure point; tighten the screw making sure there are no gas leaks;
•
after carrying out this operation, return the panel to its correct position and put the front casing back.
CHECK
the maximum heating power.
For procedure regarding regulation of the heating system thermal capacity
see «BOILER ADJUSTMENTS».
EMPTYING THE CENTRAL HEATING SYSTEM
Whenever it is necessary to empty the system, proceed as follows:
•
set ON/OFF switch in OFF position
(fig.1 page 12);
•
wait for the boiler to cool down;
turn the system drain tap
RS
(see fig. 2) and use a container to collect the water that runs out;
EMPTYING THE DOMESTIC HOT WATER SYSTEM
Whenever there is danger of freezing, the hot water system should be emptied in the following way:
•
shut off the water at the mains;
•
open all hot and cold water taps;
•
empty from the lowest point (where possible).
WARNING
Please ensure that the boiler in commissioned in line with all BENCHMARK BOOKLET REQUIREMENTS. Failure to do this may in validate
the guarentee.
Summary of Contents for RSF 30 E
Page 2: ......