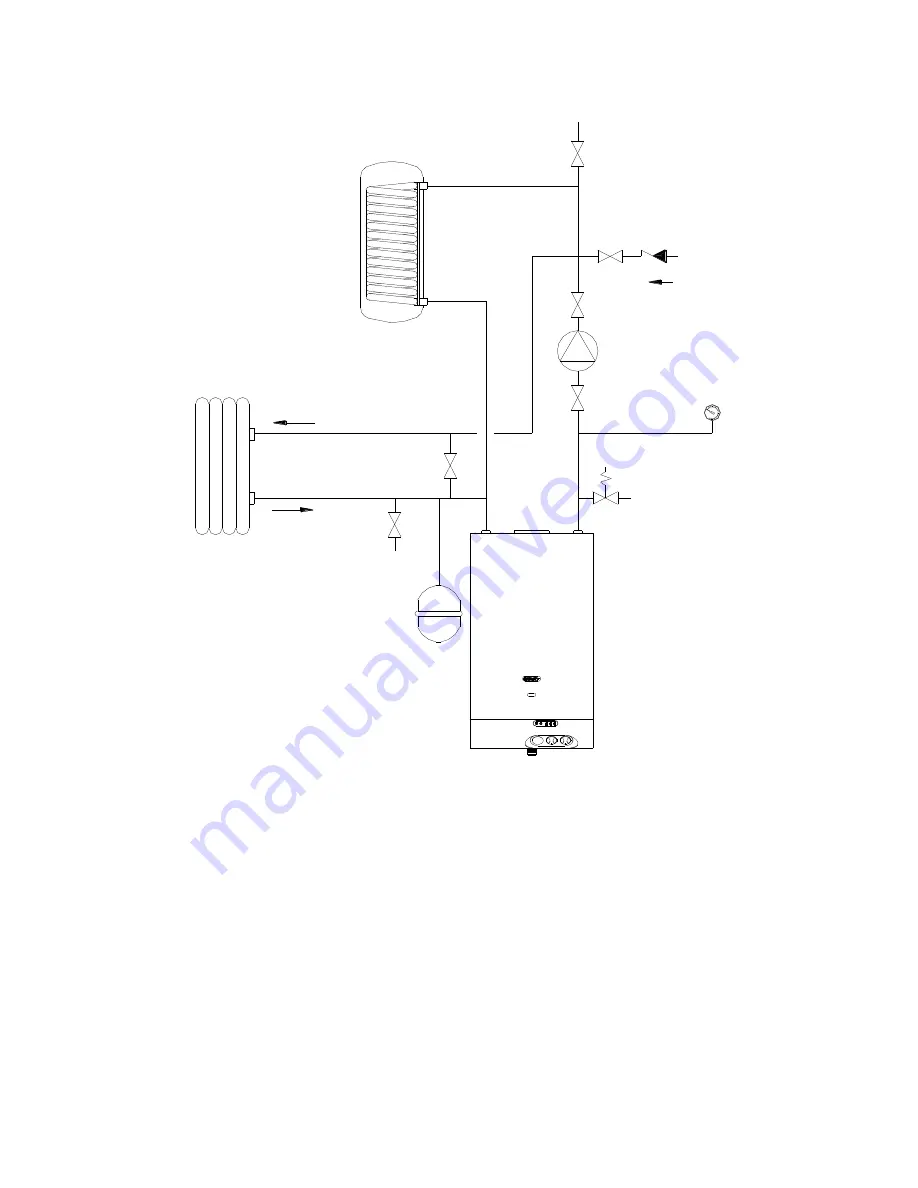
Installation Manual
SYSTEM BOILER
– TA02A101.B1203
12
SEALED WATER SYSTEM
Safety valve:
a safety valve complying with BS 6750 Part 1 must be fitted close to the boiler on the flow pipe by means of a horizontal
or vertically upward connection with no intervening valve or restrictions and should be positioned to facilitate testing. The valve should
be pre-set and non-adjustable to operate at a pressure of 3 bar. It must be arranged to discharge any water or steam through a pipe to a
safe outlet position.
Pressure Gauge
: a pressure gauge of minimum range 0-4 bar with a fill pressure indicator must be fitted to the system at the same
point as the expansion vessel in an easily visible position.
Expansion Vessel:
An expansion vessel complying with to BS 4814 must be fitted to the system by means of a connection close to the
inlet side of the circulating pump in accordance with the manufacturers instructions, the connecting pipe being unrestricted and not less
than 15mm (1/2 in) nominal size. The volume of the vessel should be suitable for the system water content and the air charge pressure
should not be less than the system static head. Further details of sealed system design can be obtained from BS 5449:Part 1 and the
British Gas publication „Specification for Domestic W. Central Heating systems‟.
Filling Point:
A filling point and an approved stop valve to BS 1010 must be fitted at low level and the method used for filling the system
should be approved by the local water undertaking. For further details see BS 6798.
Make Up System:
A method of replacing water lost from the system should be provided.
COCK
BYPASS WITH LOCKSHIELD
DRAIN
VALVE
RETURN
22 mm (min.)
FLOW
VALVE
EXPANSION
VESSEL
POINT
AIR RELEASE
FILLING POINT
CIRCULATING
PUMP
SAFETY
PRESSURE
GAUGE
Summary of Contents for RS 24 E 70/90
Page 2: ......