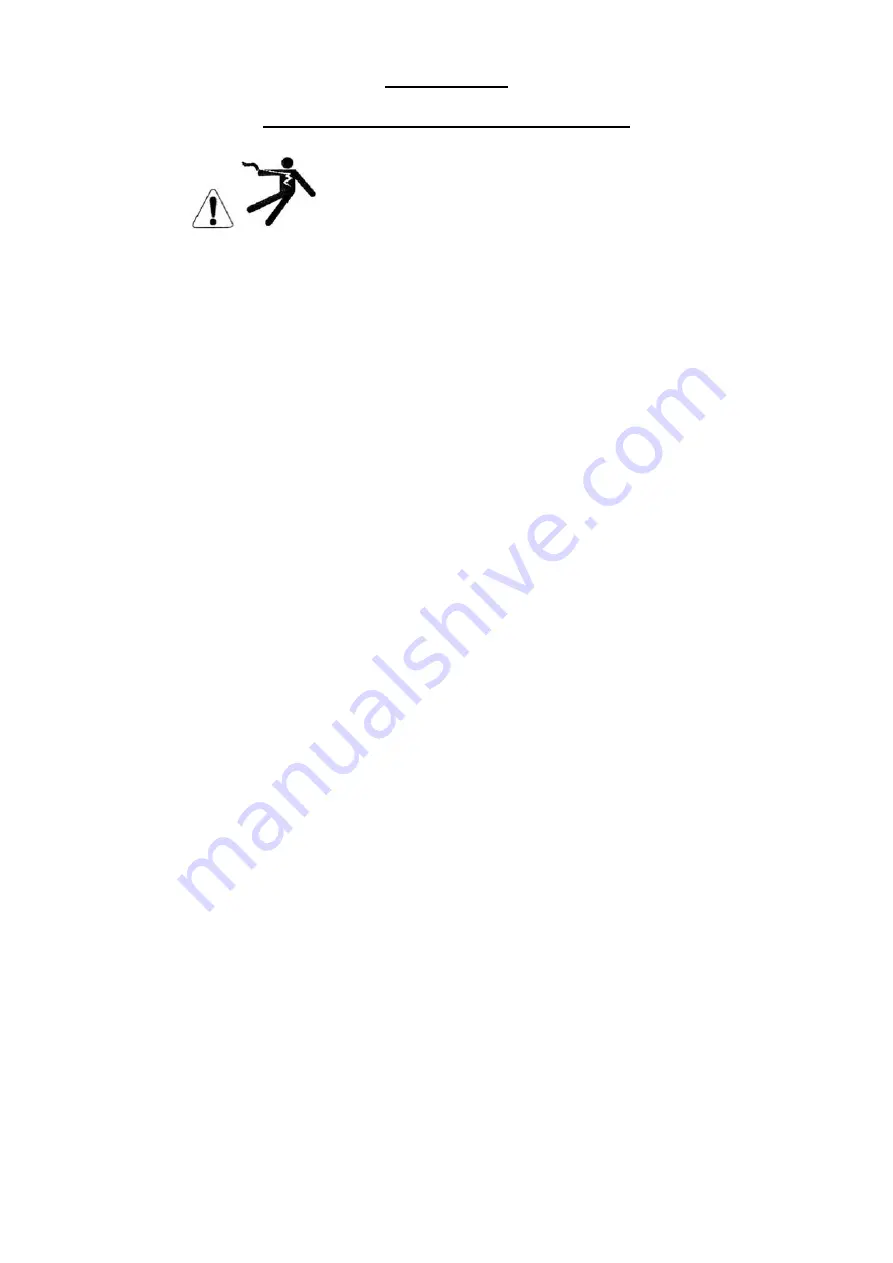
14
Maintenance
Routine and periodic maintenance
WARNING!
ELECTRIC SHOCK CAN KILL
Turn the input power OFF at the mains switch & fuse box and remove mains plug from socket before working on
this equipment.
Have a qualified electrician install & service this Plasma cutting equipment. Allow machine to sit for 5 minutes
minimum after disconnection from mains power to allow the power capacitors to discharge before working inside this
equipment.
Do not touch electrically live parts
1. Periodically (3-6 months depending on use / environment), remove the side/top panels of machine and
clean out machine with a low pressure dry air line paying particular attention to PC Boards, Fan blades and
switchgear
2. Failure to maintain plant can void manufacturer’s warranty.
3. Inspect input and output cables & hoses for fraying and cuts, replace if damaged present
4. Keep cutting torch and earth cables in good condition
5. Clean air vents to ensure proper air flow and cooling
6. The fan motor has sealed bearings which requires no maintenance