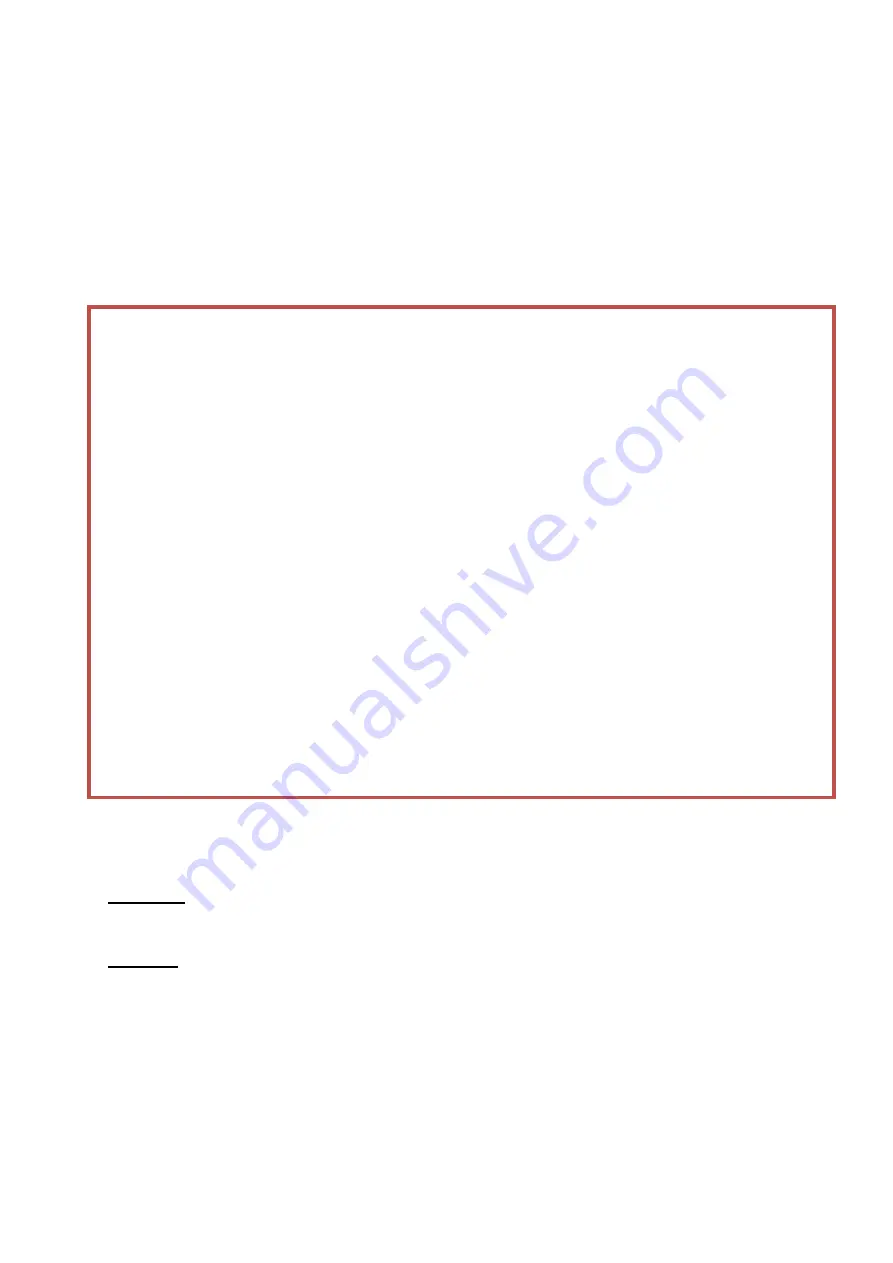
3
Thank you for selecting the R-Tech MMA160S Inverter Arc Welder.
The MMA160S has many benefits over traditional Arc welders, including an industrial 60%
duty cycle, Anti-stick hot start technology, portable and lightweight
We want you to take pride in operating our MMA160S as much pride as we have taken in
making this product for you. Please read all information in this manual before operation
PLEASE EXAMINE THE CARTON AND EQUIPMENT FOR DAMAGE IMMEDIATELY
When this equipment is shipped, title passes to the purchaser upon receipt from the courier.
Consequently all claims for material damaged in shipment must be made by purchaser against
the transportation company used.
Please record your equipment identification below for future reference. This information can be
found on the data plate at rear of machine.
Product: MMA160S
Serial No. ___________________________________
Date of Purchase _____________________________
Where Purchased _____________________________
Whenever you request replacement parts or information on this equipment please always
supply information you have recorded above.
This product is covered by a 2 year parts and labour warranty; we will cover the cost of collecting and
returning the item to you. External items, (
torch, earth lead etc…) are covered by a 3 month warranty. Any
faults/damage found caused by a customer will be charged accordingly.
Pay particular attention to the safety instructions we have provided you for your protection
The level of seriousness to be applied to each section is explained below
WARNING
This statement appears where the information must be followed exactly to avoid serious personal injury.
CAUTION
This statement appears where the information must be following to avoid a minor personal injury or damage
to this equipment.
Summary of Contents for MMA 160S
Page 1: ...MMA 160S ARC MMA WELDER OPERATION INSTRUCTIONS www r techwelding co uk ...
Page 2: ...2 ...
Page 15: ...15 15 ...
Page 16: ...16 ...
Page 17: ...17 ...