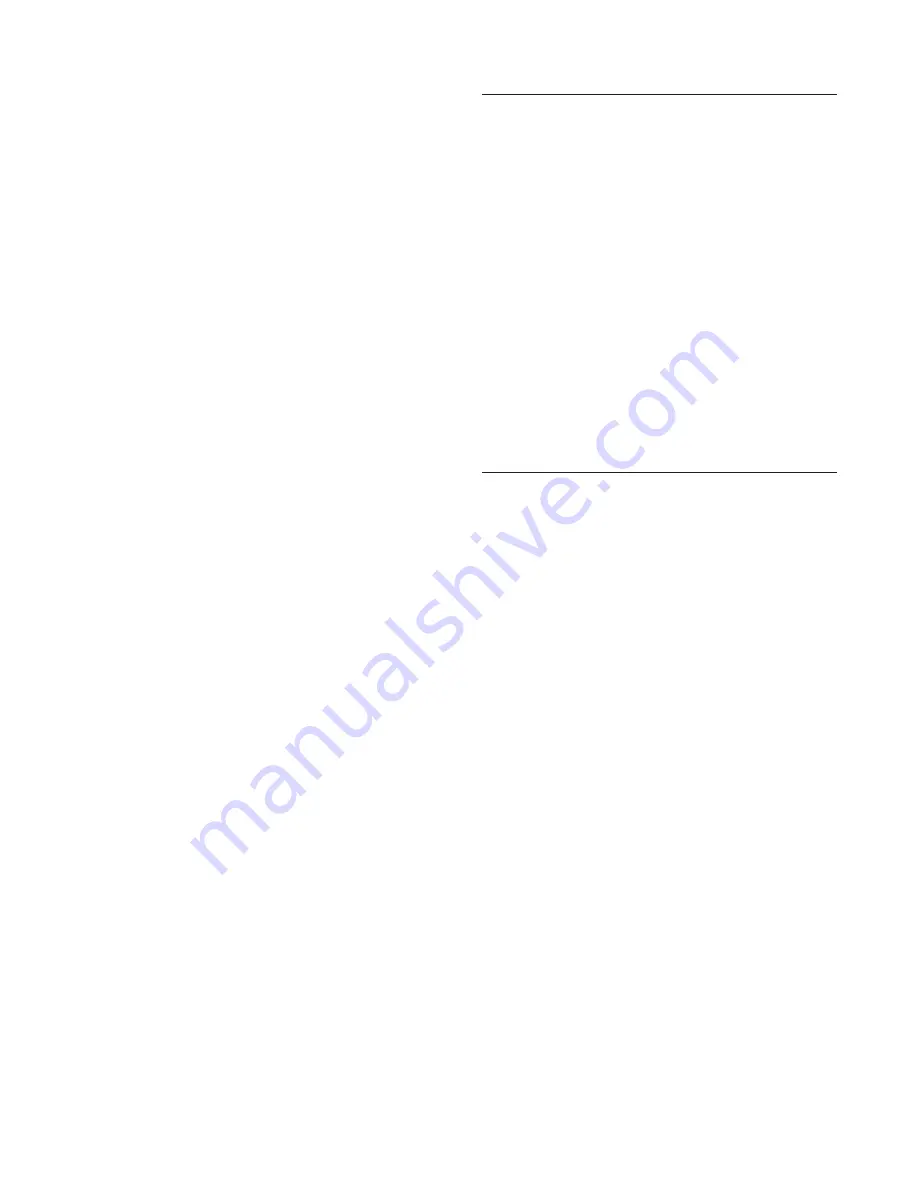
Page 3
05305L-90(J)
*Max set screw torque 80 oz-in
4. INSTALL NEW POTENTIOMETER
a) Push new potentiometer into potentiometer mounting & coil
assembly making sure o-ring is on shaft.
b) Feed potentiometer and coil wires through hole in bottom
of potentiometer housing.
c) Screw potentiometer housing onto potentiometer mounting
& coil assembly.
d) Gently pull transducer wires through bottom of potentiometer
housing to take up any slack. Apply a small amount of
silicone sealant around hole.
e) Install transducer assembly on vertical shaft allowing
0.5 mm (0.020") clearance from vertical bearing.
Tighten set screws* at bottom of transducer assembly.
f) Place potentiometer adjust thumbwheel on potentiometer
shaft and tighten set screw*.
g) Place potentiometer coupling on potentiometer adjust
thumbwheel. Do Not tighten set screw yet.
5. RECONNECT TRANSDUCER WIRES
a) Using needle-nose pliers or a paper clip bent to form a small
hook, gently pull transducer wires through hole in junction
box.
b) Solder wires to circuit board according to wiring diagram.
Observe color code.
c) Secure circuit board in junction box using two screws removed
in step 2b. Do not overtighten.
6. REPLACE MAIN HOUSING
a) Place main housing over vertical shaft bearing rotor. Be careful
to align indexing key and channel in these two assemblies.
b) Place main housing over vertical shaft bearing rotor until
potentiometer coupling is near top of main housing.
c) Turn potentiometer adjust thumbwheel until potentiometer
coupling is oriented to engage ridge in top of main housing.
Set screw on potentiometer coupling should be facing the
front opening.
d) With potentiometer coupling properly oriented, continue
pushing main housing onto vertical shaft bearing rotor until
main housing latch locks into position with a “click”.
7. ALIGN VANE
a) Connect excitation voltage and signal conditioning electronics
to terminal strip according to wiring diagram.
b) With mounting post held in position so junction box is facing
due south, orient vane to a known angular reference. Details
appear in CALIBRATION section.
c) Reach in through front of main housing and turn potentiometer
adjust thumbwheel until signal conditioning system indicates
proper value.
d) Tighten set screw* on potentiometer coupling.
8. REPLACE NOSE CONE
a) Screw nose cone into main housing until o-ring seal is seated.
Be certain threads are properly engaged to avoid cross
threading.
FLANGE BEARING REPLACEMENT
If anemometer bearings become noisy or wind speed threshold
increases above an acceptable level, bearings may need
replacement. Check anemometer bearing condition using a Model
18310 Propeller Torque Disc. If necessary, bearings are replaced
as follows.
1. REMOVE OLD BEARINGS
a) Unscrew nose cone. Set o-ring aside for later use.
b) Loosen set screw on magnet shaft collar and remove magnet.
c) Slide propeller shaft out of nose cone assembly.
d) Remove front bearing cap which covers front bearing.
e) Remove both front and rear bearings from nose cone
assembly. Insert edge of a pocket knife under bearing flange
and lift it out.
2. INSTALL NEW BEARINGS
a) Insert new front and rear bearings into nose cone.
b) Replace front bearing cap.
c) Carefully slide propeller shaft thru bearings.
d) Place magnet on propeller shaft allowing 0.5 mm (0.020")
clearance from rear bearing.
e) Tighten set screw* on magnet shaft collar.
f) Screw nose cone into main housing until o-ring seal is seated.
Be certain threads are properly engaged to avoid cross-
threading.
VERTICAL SHAFT BEARING REPLACEMENT
Vertical shaft bearings are much larger than the anemometer
bearings. Ordinarily, these bearings will require replacement less
frequently than anemometer bearings. Check bearing condition
using a Model 18331 Vane Torque Gauge.
Since this procedure is similar to POTENTIOMETER REPLACEMENT,
only the major steps are listed here.
1. REMOVE MAIN HOUSING.
2. UNSOLDER TRANSDUCER WIRES AND REMOVE
TRANSDUCER ASSEMBLY. Loosen set screws at base of
transducer assembly and remove entire assembly from vertical
shaft.
3. REMOVE VERTICAL SHAFT BEARING ROTOR by sliding it
upward off vertical shaft.
4. REMOVE OLD VERTICAL BEARINGS AND INSTALL NEW
BEARINGS. When inserting new bearings, be careful not to
apply pressure to bearing shields.
5. REPLACE VERTICAL SHAFT BEARING ROTOR.
6. REPLACE TRANSDUCER & RECONNECT WIRES.
7. REPLACE MAIN HOUSING.
8. ALIGN VANE.
9. REPLACE NOSE CONE.