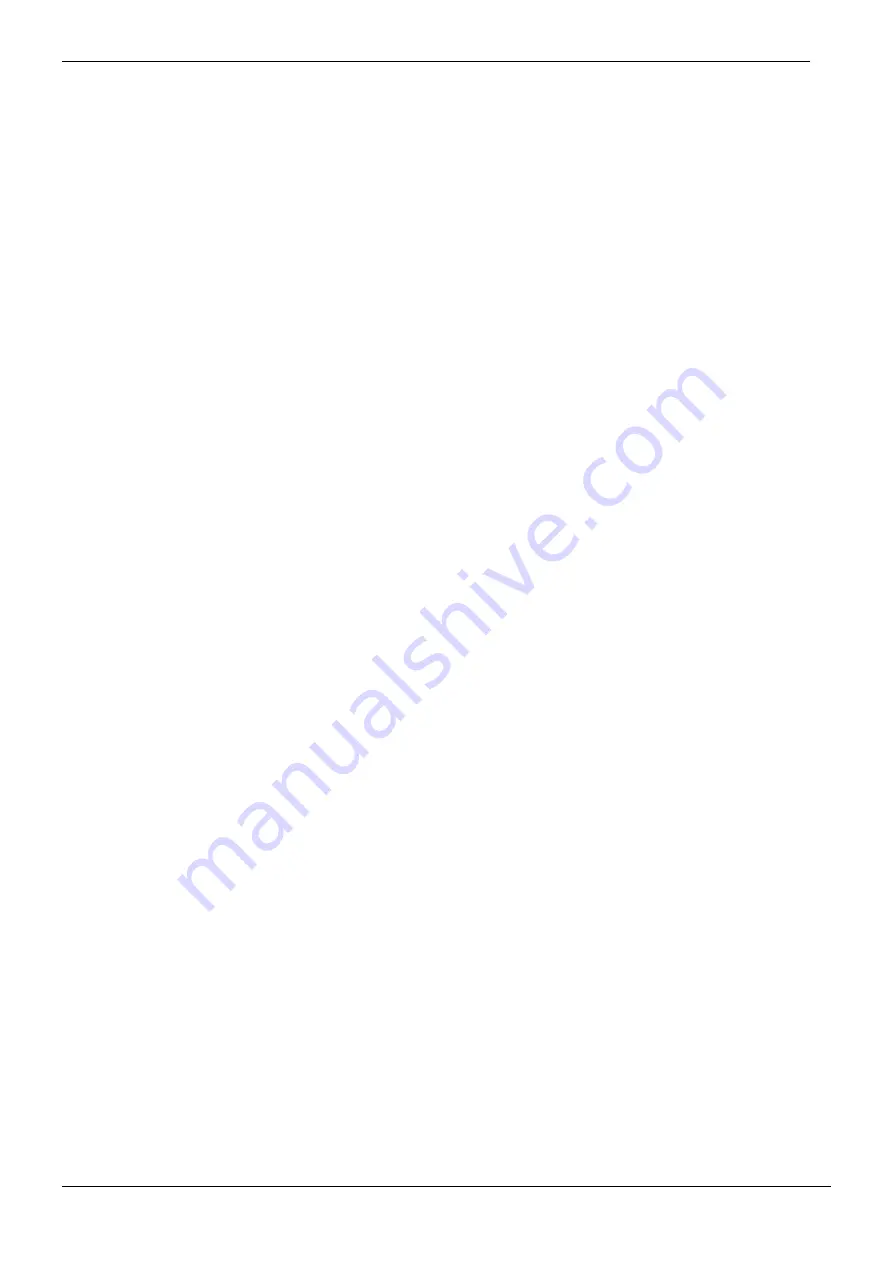
Operation
OM-SC7610
SC7610 Sputter Coater
24
Issue 1
(b)
Preparation
(i)
Check that
LEAK
and
VENT
valves are closed, (fully clockwise).
(ii)
Check the argon cylinder regulator is open. Set pressure to 0.7 bar (5-10psi).
(iii)
Set
TIME
control to required setting, say 120 seconds (the time required is process
dependent).
(iv)
Check that mains power is available, set the rear panel mounted
POWER ON/OFF
switch to the down position (ON).
(c)
Set vacuum pressure
(i)
Operate the START PUMP button, the rotary pump will start and the reducing pressure
will be indicated on the
CHAMBER PRESSURE
meter.
(ii) When the pressure reaches 0.1 mbar, partially open the LEAK valve to flush the
vacuum system with Argon. During flushing, allow the pressure to rise to between 0.5
and 1 mbar for 10-15 seconds. Close the LEAK valve and allow vacuum chamber
pressure to recover to better than 4 x 10
-2
mbar.
(d)
Set process current
Open the
LEAK
valve and monitor the vacuum pressure. When the pressure begins to rise,
intermittently operate the
SET PLASMA
button continuing to adjust the
LEAK
valve. The
PROCESS CURRENT
meter will register the current flow. Open or close the
LEAK
valve to
adjust the current to 18mA. Release the
SET PLASMA
button.
(e)
Sputter processing
(i)
Operate the
START PROCESS
button, the sputtering process will commence and a
blue coloured discharge glow will be visible in chamber. Gold-palladium or other target
material will be sputtered onto the samples for the set time period, then the discharge
will cease.
(ii)
For a thicker coating, repeat (e (i) above).
(f)
Remove Specimens
(i)
Close the
LEAK
valve to shut off the flow of argon to the chamber.
(ii)
Operate the
START PUMP
button, the indicator will extinguish and the rotary pump will
be turned
OFF
.
(iii)
Open the
VENT
valve to admit gas to the chamber.
(iv)
When the chamber pressure returns to atmosphere, close the vent valve, lift the top
plate clear of the glass chamber.
(v)
Remove the specimens.
(v) If further specimens are not to be coated immediately, close the top plate to seal the
chamber. (See Paragraph 6.3(a)-(v))