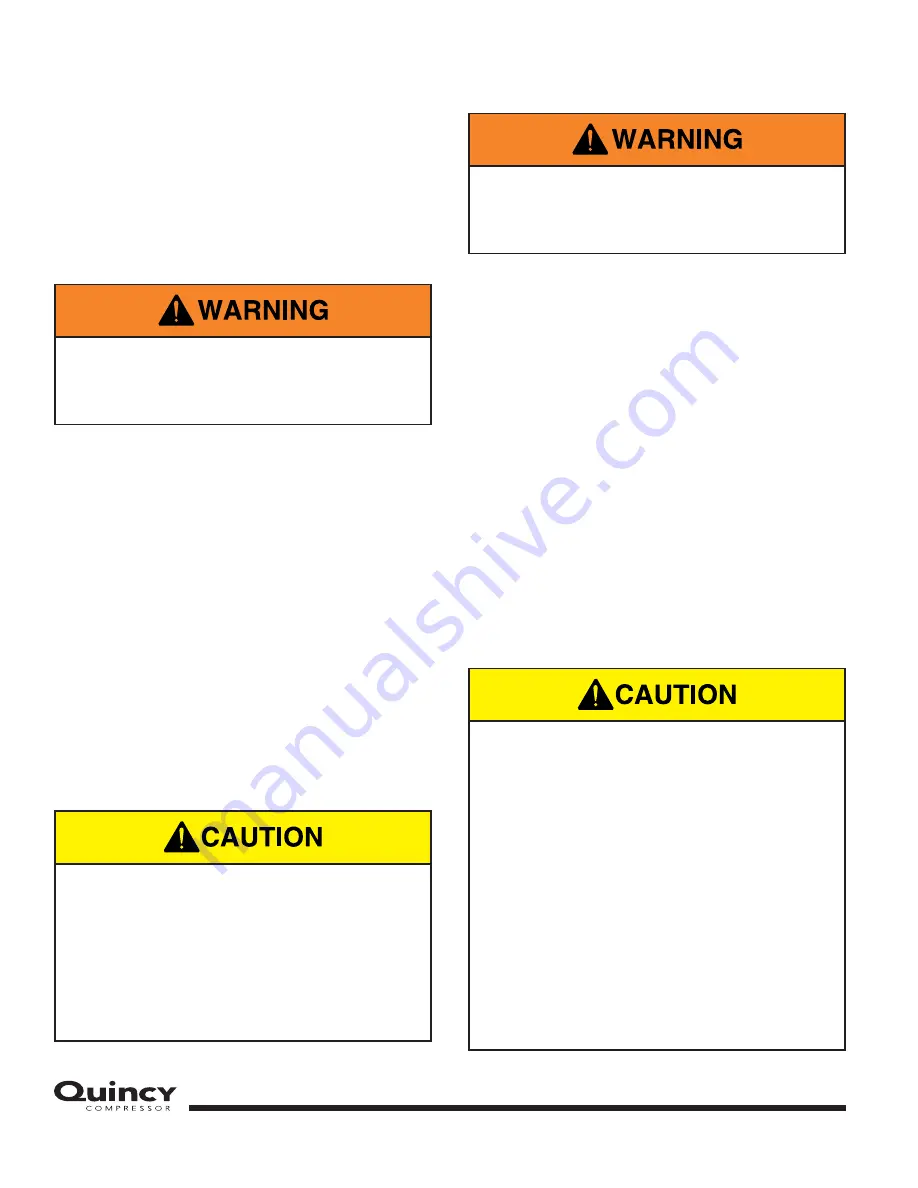
2
Pub. No. 2200772355 — October 2006
GENERAL INFORMATION
Quincy QPNC-10 to QPNC-50 Dryers are designed to
cool with direct expansion and dry evaporators. Air to be
dried is sent to the heat exchanger in which the water
vapor present is cooled and condensed. The condensate
gathers in the separator and is discharged through an
auto drain.
When properly installed, the unit requires little
maintenance or adjustment.
This manual contains important safety information. Read
THOROUGHLY and follow the Safety Instructions provided
in this manual and posted on the unit. Keep this manual
near the unit and in a safe place. Replace this manual if it
becomes torn or dirty and cannot be properly used.
Please read the Installation Instructions and Start-Up and
Operation sections of this manual before attempting to
operate the unit.
Please read the Maintenance and Troubleshooting
sections of this manual before beginning any maintenance
or service work on this unit.
INSPECTION
Inspect equipment. Any concealed shipping
damage must be reported to the carrier
immediately. Damage claims should be filed by
the consignee with the carrier.
To provide safe, breathable air, compressor must be
capable of producing at least Grade D breathing air as
described in Compressed Gas Association Commodity
Specification G7.1-1966. Special filtering, purifying and
associated alarm equipment must be used to convert
compressed air to “Breathing Air.” Other special
precautions must also be taken.
Refer to OSHA 29 CFR 1910.134.
DISCLAIMER OF WARRANTY
If this unit is used to produce breathing air, the special
equipment and precautions expressed in OSHA 29 CFR
1910.134 for specifications of the necessary equipment
and special precautions to make Breathing Air MUST BE
used or any warranties are VOID and manufacturer
disclaims any liability whatsoever for loss, personal injury
or damage.
SAFETY MESSAGES
DO NOT install, operate, maintain, adjust
or service this unit without thoroughly
reading this manual.
Cut the metal strapping carefully to prevent
injury. The packing material (plastic bags,
polystyrene foam, nails, screws, wood,
metal strapping, etc.) must not be left within
the reach of children or abandoned in the
environment, as they are a potential source
of danger and pollution. Dispose of these
materials in approved collection centers.
Air from compressor and from Quincy Air
Drying System, as equipped, is
not
safe
for human respiration (breathing).
• This dryer has been built to dry com-
pressed air for industrial use. The dryer
cannot be used in premises where there
is a risk of fire or explosion or where
work is carried out which releases sub-
stances into the environment which are
dangerous with regard to safety (for
example: solvents, inflammable vapors,
alcohol, etc.).
• This appliance must be used only for the
purpose for which it was specifically
designed. All other uses are to be consid-
ered incorrect and unreasonable. The
manufacturer cannot be held responsible
for any injury or damage resulting from
improper, incorrect or unreasonable use.