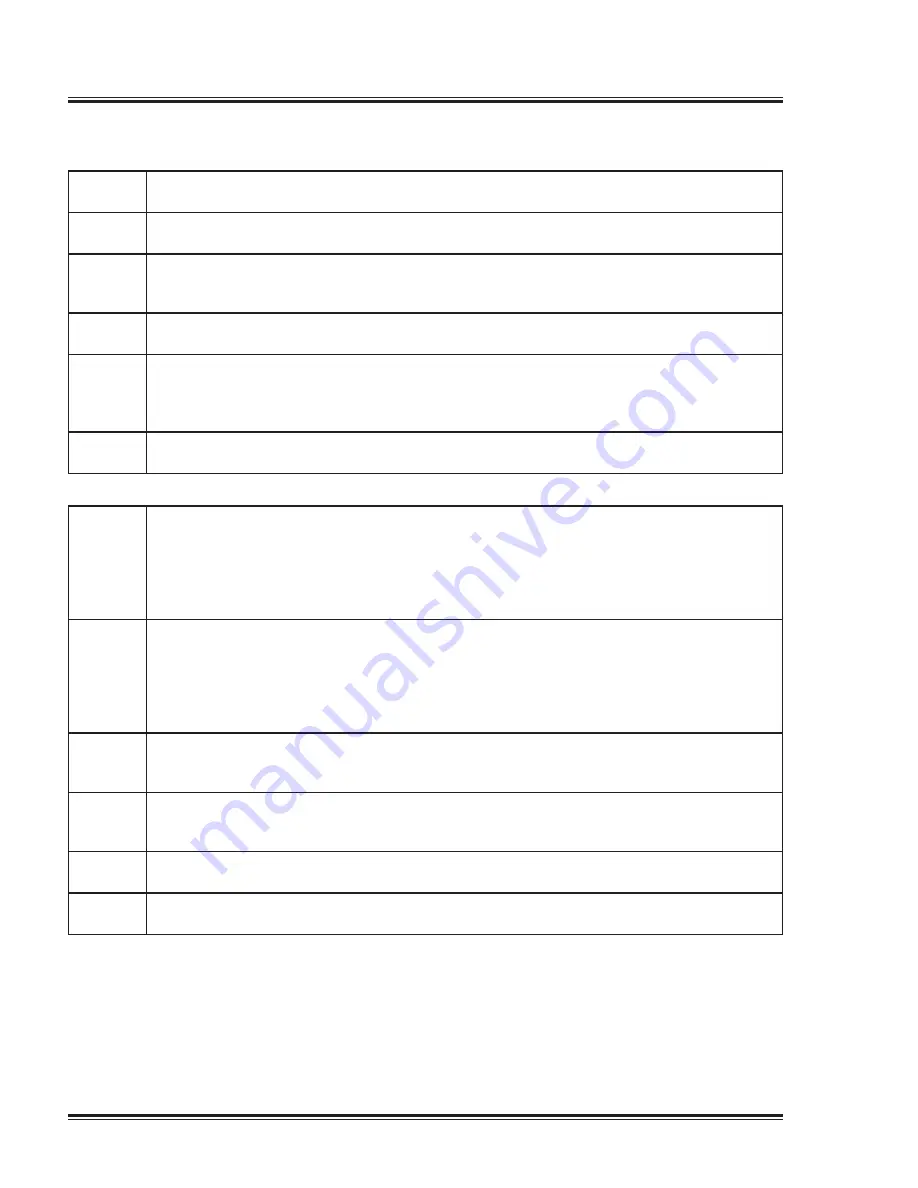
Section IX - Instructions for use
42
Quincy Compressor
Air receiver
This section applies to compressors including air receiver(s).
-
The vessel can contain pressurized air; this can be potentially dangerous if the
equipment is misused.
-
The vessel shall only be used to store compressed air and shall not be subject
to rapid fluctuation of pressure.
-
The vessel shall only be used within the pressure and temperature limits
stated on the data plate and the testing report, which should be kept in a
safe place.
-
No alterations must be made to this vessel by welding, drilling or other
mechanical methods without the written permission of the manufacturer.
-
Make sure that the vessel is equipped with suitable and appropriate safety
and control fittings and replace them with new ones if necessary (consult the
Parts list). The discharge capacity of the safety valve used must be higher
than the capacity of the compressor.
-
Do not store the vessel near heating sources and inflammable substances and
avoid storing the vessel in badly ventilated rooms.
-
Depending on the conditions of use and the configuration of the equipment,
condensate may accumulate inside the tank and must be drained every day
to prevent corrosion.
This may be done manually, by opening the drain valve,
or by means of the automatic drain, if fitted to the vessel. Nevertheless, a
weekly check of correct functioning of the automatic valve is needed. This has
to be done by opening the manual drain valve and check for condensate.
-
Yearly service inspection of the air receiver is needed, as internal corrosion
can reduce the steel wall thickness with the consequent risk of bursting.
Local rules need to be respected, if applicable. The use of the air receiver is
forbidden once the wall thickness reaches the minimum value as indicated in
the service manual of the air receiver (part of the documentation delivered
with the unit).
-
Lifetime of the air receiver mainly depends on the working environment.
Avoid installing the compressor in a dirty and corrosive environment, as this
can reduce the vessel lifetime dramatically.
-
Do not anchor the vessel or attached components directly to the ground
or fixed structures. Fit the pressure vessel with vibration dampers to avoid
possible fatigue failure caused by vibration of the vessel during use.
-
Use the vessel within the pressure and temperature limits stated on the
nameplate and the testing report.
-
No alterations must be made to this vessel by welding, drilling or other
mechanical methods.