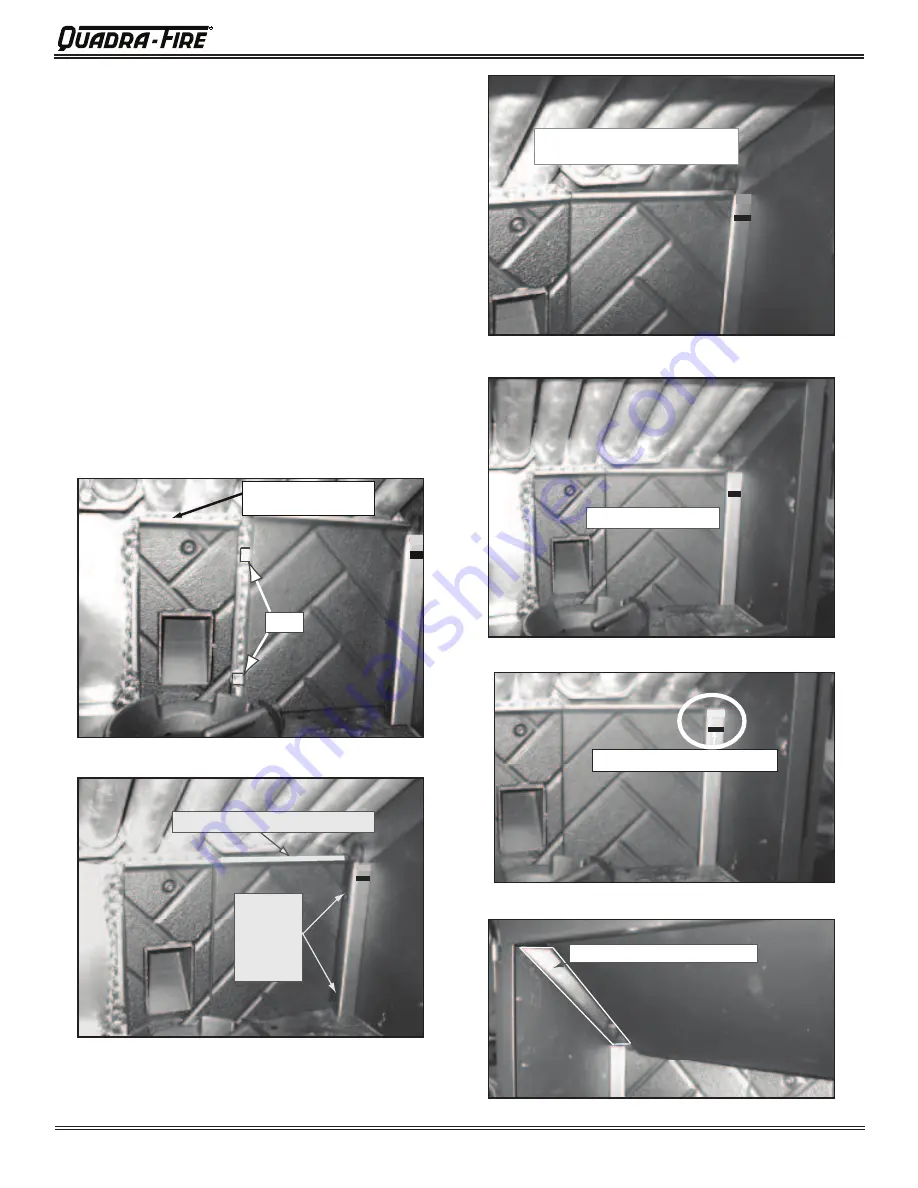
Page 38
7050-128B
September 3, 2009
Santa Fe Pellet Stove
R
F. Baffl e & Brick Replacement
Right Brick Installed
Brick is flush against back wall
Brick in
front of
clip and
Notches
exposed
Lift Brick, pull forward at an angle
and drop down into notches
Opening at left side of Baffle
Tabs
Do not remove rope
from center brick
Figure 38.1
1. Place right brick in behind the right bracket and then
slide to the left so the tabs are behind the center brick.
Figure 38.1.
2. The brick will be fl ush against the back wall and the
braket’s notches will be exposed.
Figure 38.2.
3. Pull the right edge of the brick forward and slide the
brick into the notches both top and bottom of right
bracket.
Figure 38.3.
4. Repeat for left brick.
5. Insert baffl e into top front of fi rebox and then raise up
the bottom end and insert baffl e tab into notch on the
right bracket to lock into place.
Figure 38.5.
Place the
left side hook of the bottom baffl e over the top of brick
for stability.
6. The baffl e does not completely cover the top of the fi re-
box. There is an opening as shown in
Figure 38.6.
Insert Baffle Tab into Slot
Figure 38.2
Figure 38.3
Figure 38.4
Figure 38.5
Figure 38.6