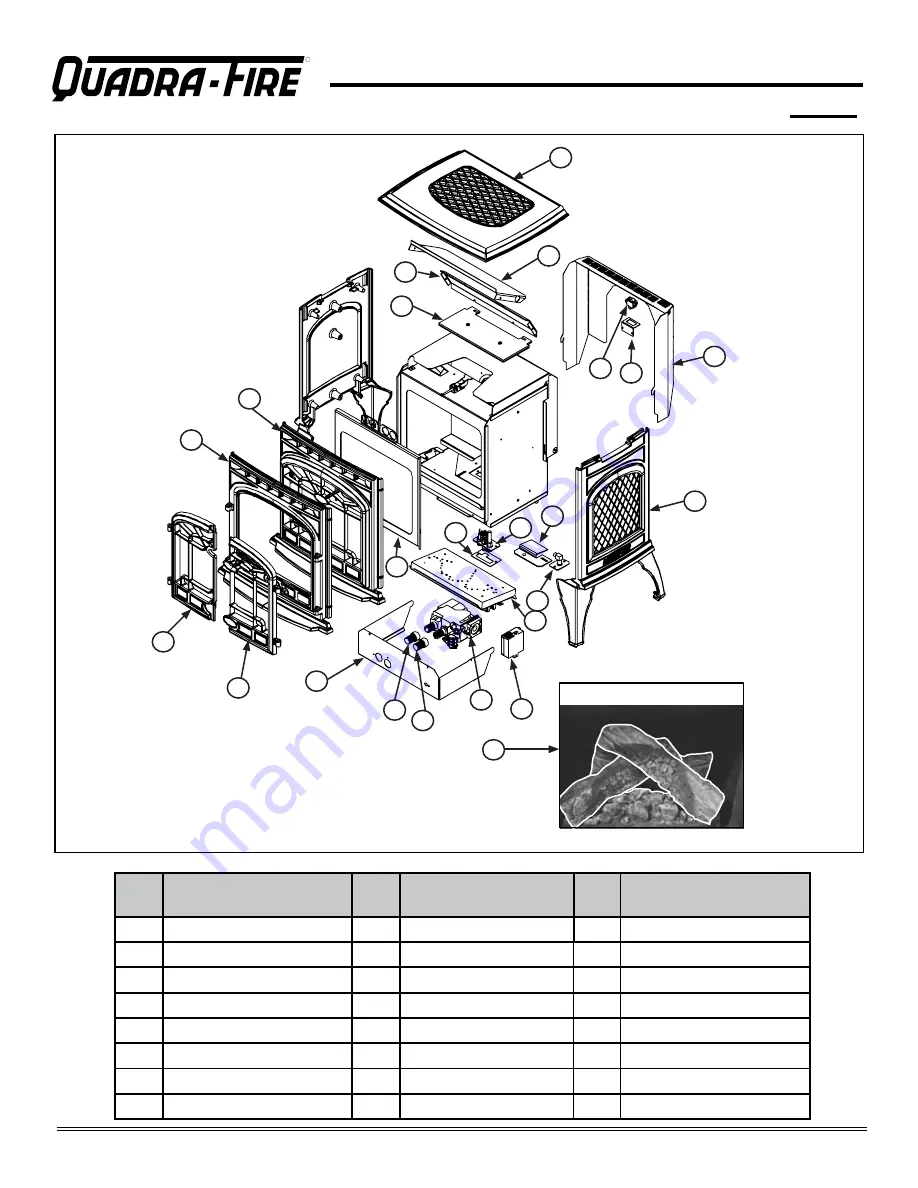
Page 48
September 1, 2008
Quadra-Fire · Garnet-T · 7016-127F
D.
Service Parts List
R
GARNET-T
(NG, LP) Exploded Parts Diagram
Beginning Manufacturing Date: 6-16-04
Ending Manufacturing Date:
Item
#
Description
Item
#
Description
Item
#
Description
1
Valve Cover
9
Pilot Assembly
17
Baffle
2
Knob, Extension, SIT, ON/OFF
10
Air Shutter Assembly
18
Relief Door Assembly
3
Knob, Extension SIT, HI/LO
11
Side
19
Front Plate, Solitaire
4
Valve
12
Back Shield
20
Front
5
Log Set
13
Switch Bracket
21
Door, Left
6
Ignition Module
14
Switch, Rocker, ON/OFF
22
Door, Right
7
Burner Assembly
15
Baffle Back
23
Door Assembly
8
Bulkhead with Flex Tube
16
Top
24
Gasket, Pilot
1
2
3
T hree-piece L og S et
11
1
6
1 4
2
7
1 3
3
8
1 2
4
1 0
1 5
5
9
23
1 6
19
24
1 7
20
1 8
21
22