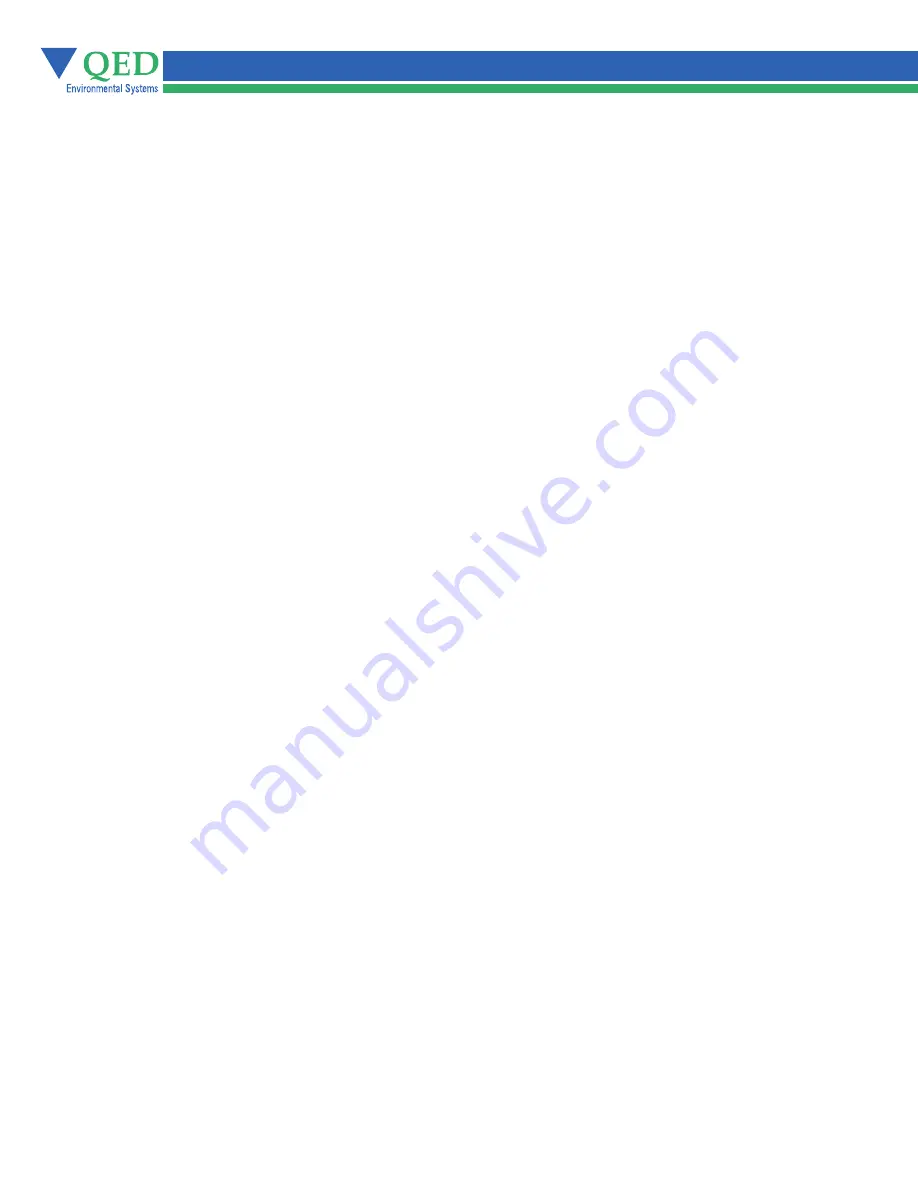
Chapter 5: Installation
1. Cover the pump tubing/hose ends with tape if they are to be pulled through trenches or laid on the
ground. This is to prevent debris from entering the lines.
2. Blow out all water and particles from compressed air conduits (including downwell pump air supply lines)
and fluid lines for at least 10 seconds after the water and particles exit before connecting them to the
system.
3. Slip clamps over appropriate tubing/hose prior to connecting the tubing/hose to the pump barbs.
4. Push tubing/hose down flush with the fitting's nut if possible; cover at least three barbs if three or more
are present (
Note:
when installing tubing in freezing weather, tubing can be dipped in warm water for a
few seconds to soften the nylon).
5. Attach pump support rope/cable to the pump.
6. Attach pump air supply and liquid discharge lines to the well cap. Attach the air exhaust line to the well
cap if the pump air is to exhaust outside the well (Note: the liquid discharge line is always the largest
diameter of the three lines, and the air supply line is always the smallest diameter).
7. Connect the pump air supply and liquid discharge lines to the appropriate surface lines/headers.
8. Turn on the air pressure to the pump (minimum of 0.5 psi per foot of vertical static head).
Note:
Submerging the pump before supplying it with air can also result in fluid entering the air supply line.This
fluid from the well can contain particles, which could interfere with operation of the pump's air valve.
9. Lower the pump to the desired depth in the well.
10. Secure the pump by tying off the pump support line or by placing the well cap (or flange) on the well.
11. Increase the air pressure to the pump until the pump is pushing the fluid out at the desired rate. With
sufficient air pressure (at least 10 to 15 psi higher than the vertical static head), the pump will gradually
draw down the fluid level in the well to the level of the pump. The time required for this draw down varies
with the yield of the well as compared to the flow rate of the pump. The maximum recommended pump
operating pressure is 120 psi.
Caution:
Submerging the pump before supplying it with air will result in fluid entering the exhaust tubing/hose.
Those fluids will be discharged from the exhaust tubing/hose during the first few cycles of the pump. If this
discharge will not be confined to the well; i.e., if the air exhaust line is routed outside the well*, it is important
to make sure that the air exhaust line is not directed such that equipment/ personnel could be splashed by the
discharged fluid when air is turned on to the pump.
Note:
If the well environment is such that deposition occurs on stainless steel parts, the operator
may wish to raise the pump above the water level during a shutdown of the system.
* Routing the air exhaust in vacuum wells:
When QED controllerless pumps are used in wells that are under vacuum, and the exhaust air is
routed into the well, the well level will be maintained at this normal actuation point. If, however, the
well is under vacuum and the exhaust air is routed outside of the well (to atmospheric pressure),
the actuation point of the pump will be higher than the normal actuation point by a distance equal
to the amount of vacuum applied to the well (expressed in "inches of water column"). Please note
that the pump will still function normally and maintain the liquid level, albeit a higher level.
QED controllerless pumps automatically control the liquid level in the well. Under normal conditions,
the liquid level will be maintained at a point approximately one foot below the top of a bottom load
pump (this is the pump's actuation point). The pump will automatically start and stop as needed to
maintain the level at this actuation point.
9