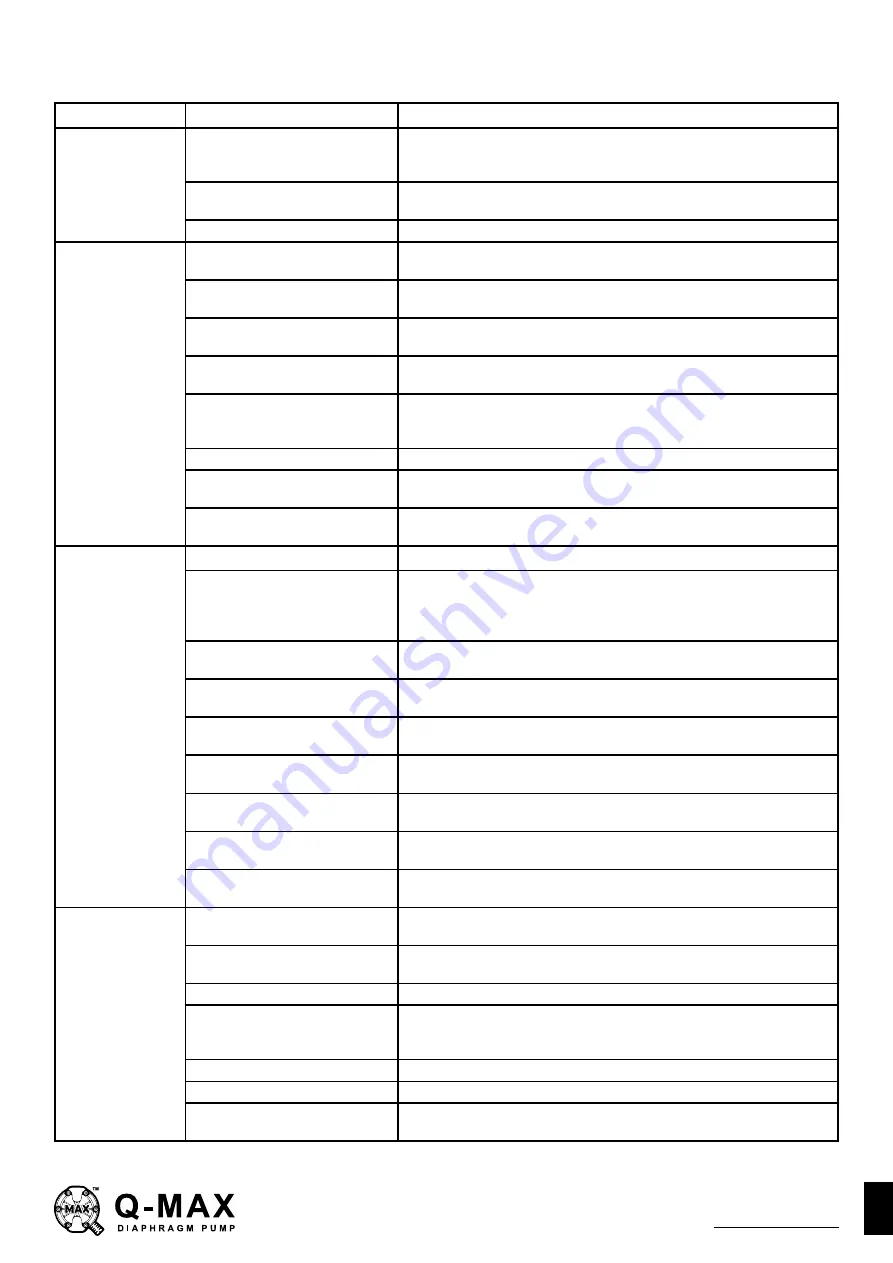
MAX-FLO MY1-25 METAL & NON-METAL - Supreme Performance
Assembly, Installation & Operation Manual | www.qmax.com.my
7
TROUBLESHOOTING GUIDE
Symptom:
Potential Cause(s):
Recommendation(s):
Pump Cycles
Once
Deadhead (system pressure
meets or exceeds air supply
pressure).
Increase the inlet air pressure to the pump. Pump is designed for 1:1
pressure ratio at zero flow. (Does not apply to high pressure 2:1 units).
Air valve or intermediate gaskets
installed incorrectly.
Install gaskets with holes properly aligned.
Bent or missing actuator plunger. Remove pilot valve and inspect actuator plungers.
Pump Will Not
Operate / Cycle
Pump is over lubricated.
Set lubricator on lowest possible setting or remove. Units are designed
for lube free operation.
Lack of air (line size, PSI, CFM).
Check the air line size and length, compressor capacity (HP vs. CFM
required).
Check air distribution system.
Disassemble and inspect main air distribution valve, pilot valve and pilot
valve actuators.
Discharge line is blocked or
clogged manifolds.
Check for inadvertently closed discharge line valves. Clean discharge
manifolds/piping.
Deadhead (system pressure
meets or exceeds air supply
pressure).
Increase the inlet air pressure to the pump. Pump is designed for 1:1
pressure ratio at zero flow. (Does not apply to high pressure 2:1 units).
Blocked air exhaust muffler.
Remove muffler screen, clean or de-ice, and re-install.
Pumped fluid in air exhaust
muffler.
Disassemble pump chambers. Inspect for diaphragm rupture or loose
diaphragm plate assembly.
Pump chamber is blocked.
Disassemble and inspect wetted chambers. Remove or flush any
obstructions.
Pump Cycles and
Will Not Prime or
No Flow
Cavitation on suction side.
Check suction condition (move pump closer to product).
Check valve obstructed. Valve
ball(s) not seating properly or
sticking.
Disassemble the wet end of the pump and manually dislodge
obstruction in the check valve pocket. Clean out around valve ball cage
and valve seat area. Replace valve ball or valve seat if damaged. Use
heavier valve ball material.
Valve ball(s) missing (pushed
into chamber or manifold).
Worn valve ball or valve seat. Worn fingers in valve ball cage (replace
part). Check Chemical Resistance Guide for compatibility.
Valve ball(s) / seat(s) damaged
or attacked by product.
Check Chemical Resistance Guide for compatibility.
Check valve and/or seat is worn
or needs adjusting.
Inspect check valves and seats for wear and proper setting. Replace if
necessary.
Suction line is blocked.
Remove or flush obstruction. Check and clear all suction screens or
strainers.
Excessive suction lift.
For lifts exceeding 20’ of liquid, filling the chambers with liquid will prime
the pump in most cases.
Suction side air leakage or air in
product.
Visually inspect all suction-side gaskets and pipe connections.
Pumped fluid in air exhaust
muffler.
Disassemble pump chambers. Inspect for diaphragm rupture or loose
diaphragm plate assembly.
Pump Cycles
Running Sluggish
/ Stalling, Flow
Unsatisfactory
Over lubrication.
Set lubricator on lowest possible setting or remove. Units are designed
for lube free operation.
Icing.
Remove muffler screen, de-ice, and re-install. Install a point of use air
drier.
Clogged manifolds.
Clean manifolds to allow proper air flow.
Deadhead (system pressure
meets or exceeds air supply
pressure).
Increase the inlet air pressure to the pump. Pump is designed for 1:1
pressure ratio at zero flow. (Does not apply to high pressure 2:1 units).
Cavitation on suction side.
Check suction (move pump closer to product).
Lack of air (line size, PSI, CFM).
Check the air line size, length, compressor capacity.
Excessive suction lift.
For lifts exceeding 20’ of liquid, filling the chambers with liquid will prime
the pump in most cases.