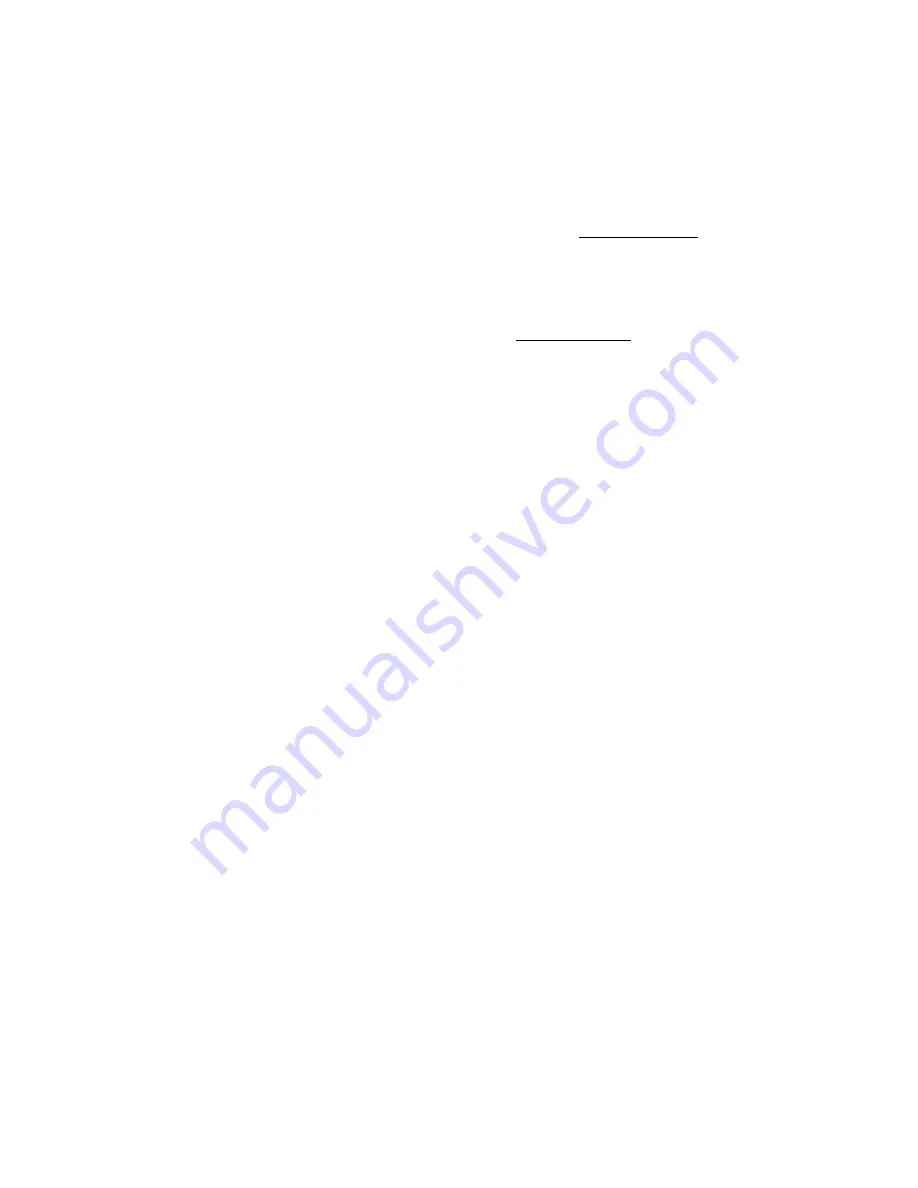
Periodic Maintenance
1)
Lubricate the packing’s (5) on the PC100 valve every 200 hrs by placing a few
drops of mineral oil or other light oil inside the packing nut.
*Note: PVA offers a 2.5cc mineral oil lubrication kit; Part#: B62-0752
2)
The packing nuts (6) will require occasional tightening, as wear occurs in order to
prevent leaks through the packing.
3)
At the end of each day, remove and dispose of the static mixer, then replace the
mixer with a night cap to prevent material exposure to the atmosphere.
*Note: PVA offers a standard night cap seal; Part#: 165-CAP
Routine Cleaning and Disassembly
Cleaning and rebuilding the valve will be required from time to time. A spare
parts kit, part #
PC1-SP
is available with all the normal wear parts included.
1)
Begin disassembly by removing air and fluid pressure from the valve.
2)
Remove all pneumatic tubing and fluid delivery fittings, hoses, etc. from the
valve.
3)
Remove the retaining nut (23) and dispose of the static mixer.
4)
Using the tip of a 3/32” Allen key, loosen both packing nuts (6).
5)
Using the same 3/32” Allen key, evenly remove the four machine screws (13) that
are located on the same corners as the standoffs (4). Note during removal that
there are springs (17) forcing the air sections away from the fluid section.
6)
Pull the air sections (red anodized portions) away from the fluid section (stainless
steel portion).
7)
Clean off the tip of the stainless steel needles (3).
8)
From the fluid section of the valve, unthread and remove the packing nuts (6), and
the packing’s (5).
9)
Using a 3/32” Allen Key, remove the eight machine screws (24) that hold the
fluid sections (4) to the manifold (1) and separate the sections.
10)
Remove the two 010 Kalrez o-rings (21) from the manifold (1).
11)
Using pliers pull the seats (2) out of the fluid sections (4) and remove the 006
Kalrez o-rings (15) from the seats. Note: If stuck, the seats can be pushed through
from the opposite side of the fluid section.
12)
Clean all of the wetted parts thoroughly with an appropriate solvent.
13)
On the air sections, use a standard 3/32” Allen Key to evenly remove the final
four machine screws (14) that thread into the end caps (7). Note: During removal
that the springs (17) will force the air sections apart.
14)
Separate the upper air bodies (11) from the lower air bodies (8) to remove the
springs (17) then slide the end caps (7) off of the needles (3).
15)
Holding the lower air bodies (8) in one hand, grab the needles (3) and push the
needle and piston (10) assemblies out of the lower air bodies.
16)
Remove the 004 Buna o-rings (16) from the lower air bodies (8).