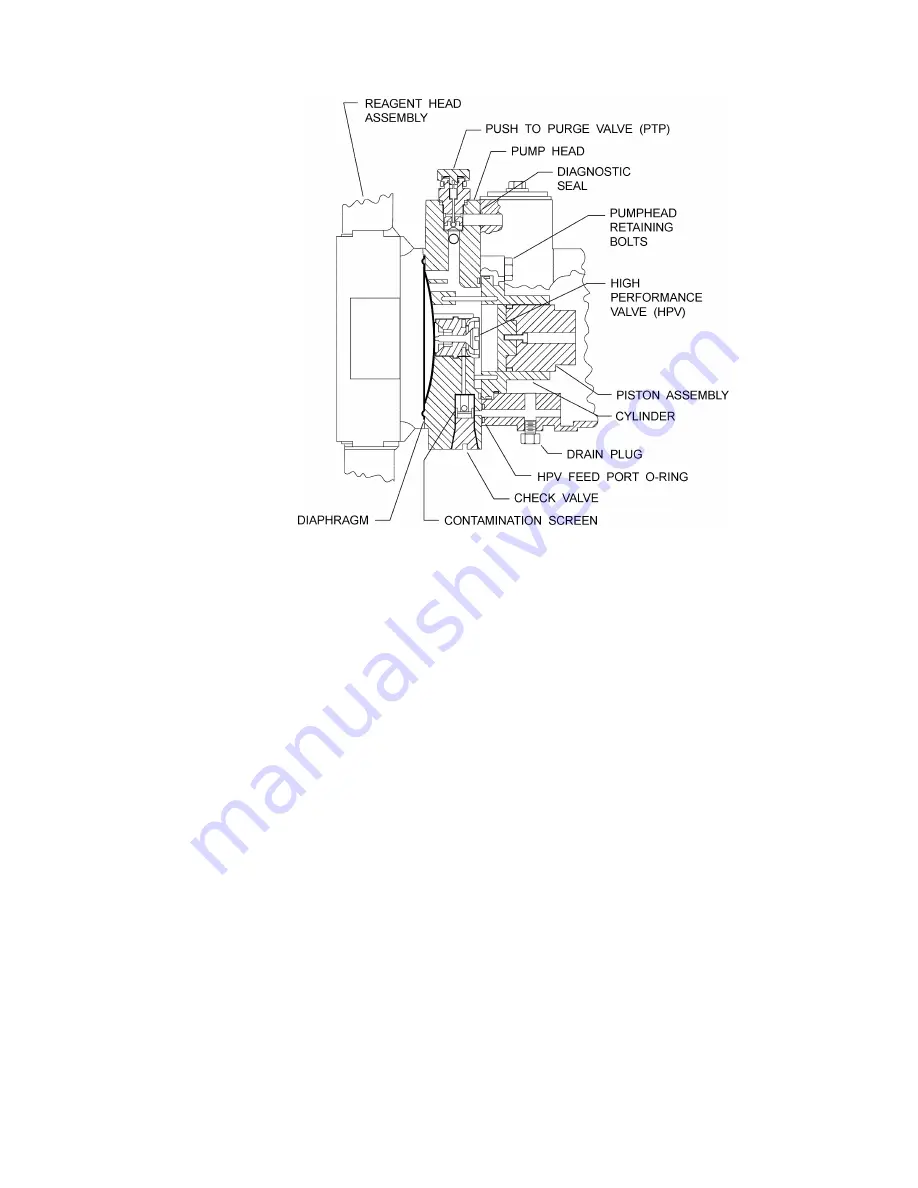
20
7.2.2 Re-Priming the Pump head
Figure 15
Leak Detection diaphragm systems require special hydraulic priming considerations to
protect the diaphragm from damage during initial pump startup. Refer to Appendix I,
page 33 and review these procedures carefully before re-starting a PULSAR pump
equipped with a leak detection system
.
Hydraulic Priming Procedure, for standard Composite (THY) and Solid (PTFE) diaphragms:
1. Disconnect the power source to the drive motor.
2. Relieve all pressure from the piping system and where possible allow liquid to enter the
reagent head assembly.
3. Remove the diagnostic window and fill the eccentric box with
PULSA
lube 7H hydraulic oil to
the proper level. Replace the diagnostic window.
4. Turn on the pump and adjust the stroke length to the maximum setting of 100%.
5. Fully depress and hold the PTP valve. After several minutes oil should begin to flow out of
the center diagnostic port. Continue to hold the valve down until the oil is clear of bubbles.
The pump is now primed. If oil fails to flow out of the diagnostic port, proceed to step 6.
6.
Reset to the zero-stroke length setting
and turn off the pump. Setting the pump to zero
stroke moves the piston forward to prevent diaphragm damage at startup.
7. Remove the PTP valve from the pump head. Using a small plastic funnel, slowly pour oil
into the pump head through the PTP valve port until full.
8. Replace the PTP valve, ensuring that the flat copper gasket and o-ring are properly in place.
9. Turn on the pump. Gradually raise the stroke to the full 100% setting. Fully depress and
hold the PTP valve. Oil should begin to flow out of the center diagnostic port. Continue to
hold the valve down until the oil is clear of bubbles. If oil fails to flow out of the diagnostics
port, then additional oil is required in the pump head: repeat steps (6) and (7) above.
Summary of Contents for PULSAR 25HJ
Page 53: ...47...