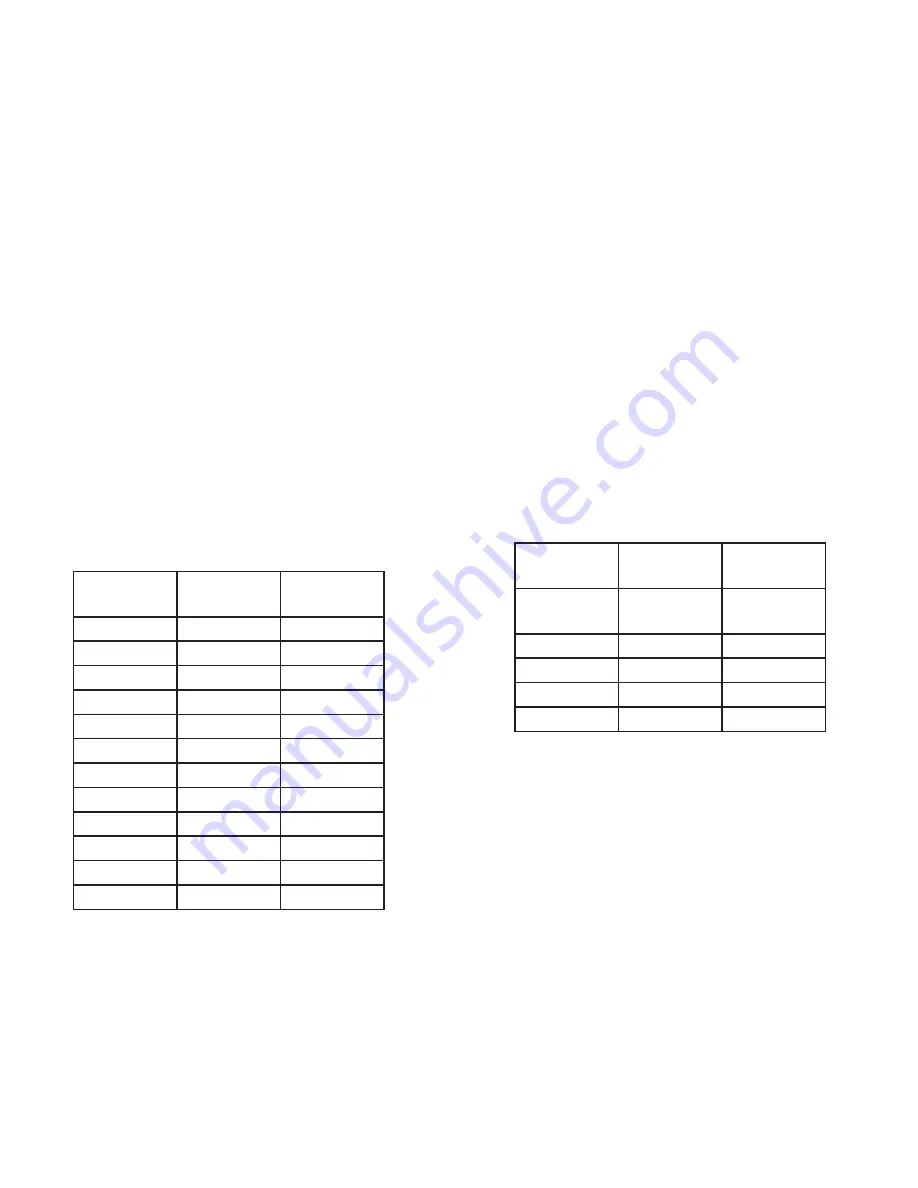
9
RECOMMENDED TURNING SPEEDS
WARNING. Turning too fast for the size of your work may result in injuring yourself or damaging the lathe!
Work piece
Diameter
Max RPM
Roughing
Max RPM
Finishing
1”
3600
3600
2”
3000
4000
3”
2000
2600
4”
1500
2000
5”
1200
1600
6”
1000
1330
7”
850
1100
8”
750
1000
9”
660
900
10”
600
800
11”
540
725
12”
600
660
Maximum Speeds for Balanced Turnings
Multi Speed Chart for TCLC10
Max work
piece dia.
Max Speed
Roughing
9”
Finishing
10”
610
6”
8”
1000
4”
5.5”
1450
3”
4”
2000
2” or less
2.5”
3000
Chart for TCLC10VS & TCLC12VS
Tool Rest (6)
- The tool rest is used to steady the cutting tool while the lathe is in operation. You can position the tool
rest by releasing the lock handle(28) positioned on the side of the rest and sliding the rest into the desired position.
Tighten the lock handle to secure the tool rest into position. The height of the tool rest can be adjusted releasing the
lock handle(27) located on the front of the rest and adjusting the height to the desired position and then tightening the
lock handle.
The position of the entire tool rest can be adjusted by reaching under the bed and loosening the clamp nut. Slide
the rest into position. Tighten the clamp nut. The tool rest should be positioned just above the center line of the work
piece.
Note: The lock levers are spring loaded. To operate, pull out on the lever, rotate it on the pin, and then release.
Changing Belt Speeds
-
Make sure the lathe is unplugged. Loosen the knob on the cover plate. Slide the cover up
and off the lathe. Loosen the motor plate ratchet handle (10) to allow the motor plate to swivel upwards. To change the
speed, move the belt drive from one pulley to another. (Note, Always go from the larger pulley to the smaller pulley)
After moving the belt, tighten the motor pulley with the ratchet handle (10)- this also tightens the belt. Turn your latheês
power on, and make sure that the belt is running consistently in its parallel groove (this should be done with the hand
wheel(9). If all is smooth, turn the power off, reattach the cover.
Replacing the Belt
-
The Turncrafter Commanders are designed with a special feature that allows quick and easy belt changes.
•
Loosen belt, `Remove old belt
•
Slide the new belt over the headstock spindle pulley and onto the motor pulley.