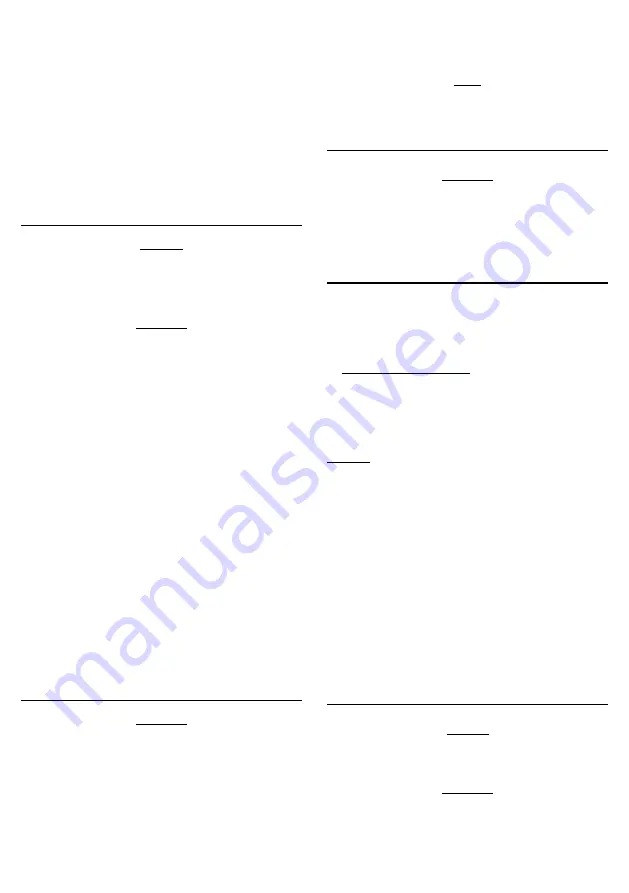
- 9 -
1. Release the clamp screw 4 (Fig. 7), push the tailstock (2) on the
guide into the required position and retighten the clamp screw.
2. To insert a tool, e.g. the centre 1 (Fig. 7), extend the sleeve
approx. 10 mm by turning the handwheel 3.
3. Insert the centre 1 (Fig. 7) and shank taper firmly into the sleeve
by hand. The shank taper is secure and cannot be removed
from the front.
4. To release an inserted tool, turn handwheel (3) to the left to
stop.
5. Then turn approx. one further turn against the resistance. The
taper is released and can be removed.
6. The sleeve can be clamped in any position by tightening the
screw 5 (Fig. 7).
Selecting the turning tool
Warning
Use only accessories recommended for this lathe. Follow the
instructions that accompany accessories. Use of improper acces-
sories may cause hazards.
For your own safety, use only lathe cutters sized and recommended
for this lathe. Follow the instructions that accompany the cutters.
Important
For proper turning, it is essential that:
• the correct turning tool has been selected for the appropriate
purpose
• the blade of the turning tool is sharp
• the blade of the turning tool sits exactly in the "centre" position
• and is operated at the correct speed.
Inside turning tools (a) (Fig. 8)
• are used for interior diameter turning.
Cutoff tools (b)
• for plungecutting grooves and cutting off work pieces.
Thread tools (c)
• are used for cutting outer threads. Finishing or tapering tools (d)
• are used to achieve a clean surface when removing small chips.
Right side tools (e)
• are used to remove as many chips as possible in a short time
when machining towards the right, regardless of the surface
quality of the work piece.
Left side tools (f)
• are used to remove as many chips as possible in a short time
when machining towards the left, regardless of the surface qua-
lity of the work piece.
Inserting the turning tool in the tool holder
Important
Give the turning tool as short an overhang as possible. Allowing
the tool to project too far leads to vibrations, imprecision and an
unclean surface.
1. Unscrew both fastening screws 1 (Fig. 9) until the selected tur-
ning tool (3) fits into the mount.
2. Give the turning tool as short an overhang as possible. Allowing
the tool to project too far leads to vibrations, imprecision and
an unclean surface.
3. Insert the turning tool (3) and tighten the fastening screws (1).
4. Move the turning tool to the centre (4) and check whether the
height has been correctly adjusted.
Note:
For height deviations, small metal sheets (2) (e.g. valve sensor
gauges) must be placed beneath the complete surface.
Setting the spindle speeds
Important
Always disconnect the mains plug before working on the drive
gearbox. Risk of injury.
The spindle speed must be adjusted to suit the work piece
material and diameter.
Calculating the maximum spindle speed
The required spindle speed can be calculated when the specified
maximum cutting speed for a certain material is known.
Maximum permissible spindle speed
Cutting speed x 1000
=
Working piece diameter x 3.14
Example:
A work piece with a diameter of 20 mm is to be turned at a cutting
speed of 50 rpm.
50 x 1000
= 796/min
20 x 3.14
By shifting the V-belt (Fig. 10), set to the next highest speed. In
this case, the speed is 1600 rpm. The correct speed is now set via
the controls, and here is important to note that the controls cover
a speed range of 25% to 100%, i.e. in our example, 400 rpm to
1600 rpm.
1. Release the clamp screw from the drive gearbox and open the
flap.
2. Release Vbelt tensioner 1 (Fig. 10).
3. Adjust the relevant speed by shifting the Vbelt according to Fig. 11
4. Retighten Vbelt tensioner. Note the appropriate tension of the
Vbelt. Overtensioning increases the wear of the belt and
bearing and reduces the motor power.
5. Close the drive gearbox before commencing turning work.
Clamping the work piece in the lathe chuck
Warning
To avoid injury from accidental start, make sure the switch is in the
OFF position and the plug is not connected to the power source
receptacle before changing any parts or tools (i. e. cutter).
Important
If work pieces are clamped in the lathe chuck using the tail stock
without a steady, the projection (Fig. 12) must not be greater than
three times the diameter of the material (L = 3 x D).
Summary of Contents for PD 250/E
Page 1: ...PD 250 E Manual...
Page 16: ...16 Spare parts list Assembly 00 Change gears...
Page 18: ...18...
Page 22: ...22 Spare parts list Assembly 04 Tailstock...
Page 25: ...Notes 25...
Page 26: ...Art Nr 34004 99 PR 709716701 J...