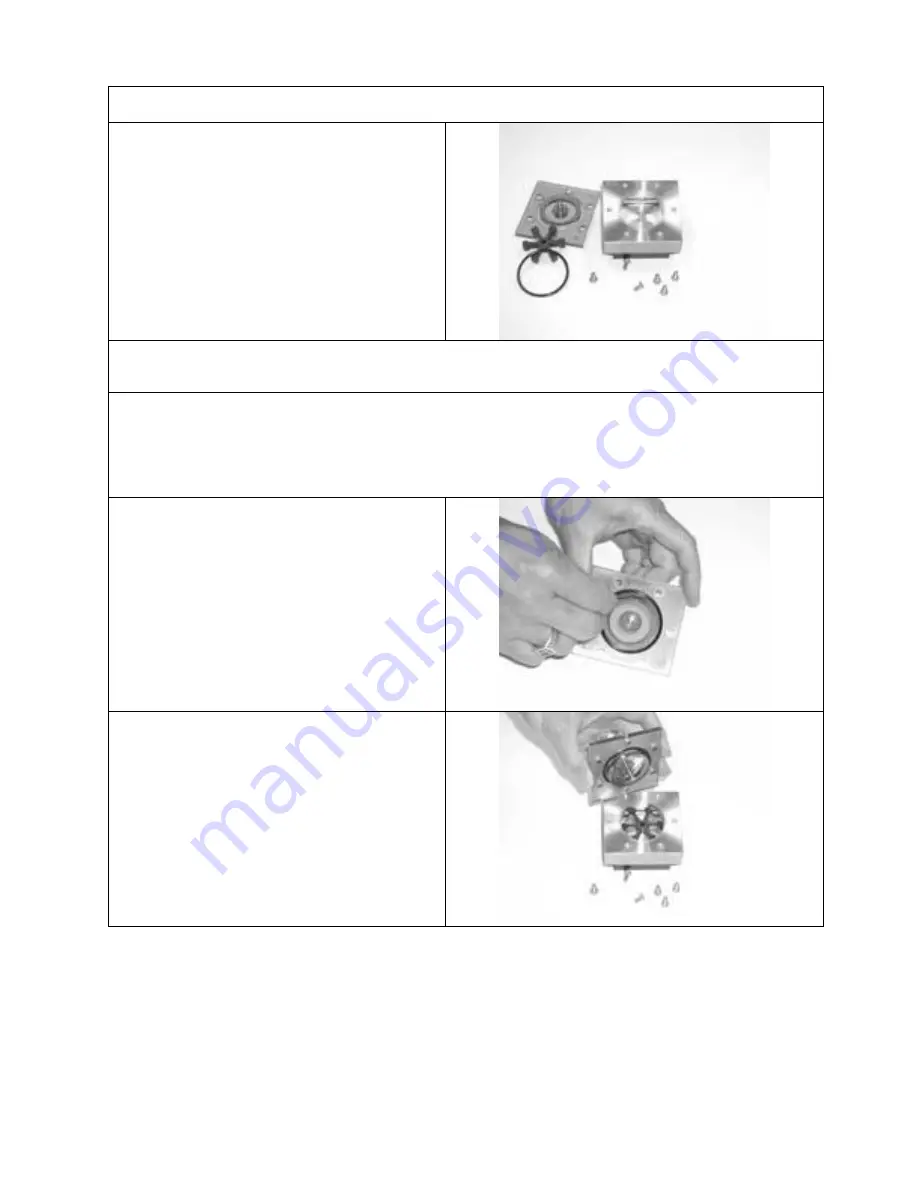
18
Cleaning the 800 Series Flow Sensor
4. Remove the rotor and stainless steel shaft
from the flow cavity.
Remove the O-ring from the faceplate
5. Using a soft cloth dampened with water, alcohol or a light detergent solution, clean debris and dirt
from the rotor, the stainless steel shaft, the inside surfaces of faceplate and the surfaces of the flow
cavity
6. Inspect the bearing surface of the rotor.
If the bearing surface is worn or not round, replace the rotor.
Inspect the stainless steel shaft.
If the shaft shows signs of scoring or other wear, replace the shaft or the whole faceplate assembly.
7. Inspect the O-ring to ensure that it is not
brittle, cracked or otherwise damaged.
If necessary replace with a #132 O-ring of a
material compatible with the liquid being
passed through the flow meter.
Position the O-ring on the inner rim of the
faceplate.
8. Place the rotor in the flow cavity.
Position the shaft (or the faceplate) to locate
the shaft in the rotor.