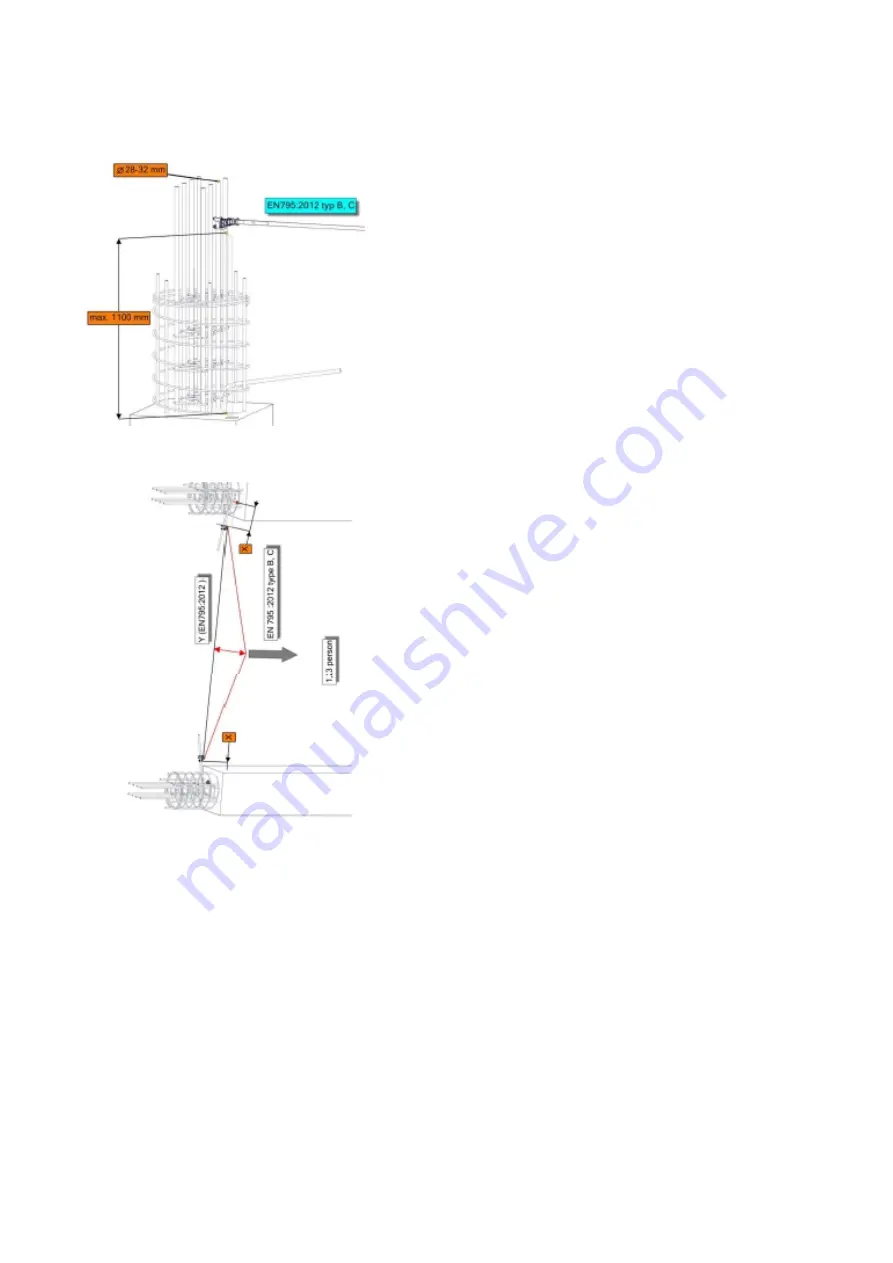
If the anchor point is going to be used with horizontal anchor system compliant with EN
795:2012 type B, C, and Figure 8 it is necessary to meet the following conditions:
Diameter of ribbed bar core must be 28–32 mm.
Lower surface of anchor point
A-165
cannot be installed on the bar higher than 1100mm
above concrete structure surface.
It is necessary to include additional deflection of horizontal lifeline by a height at which
anchor points
A-165
were installed Figure 9.
Figure 8. Installation of horizontal lifelines in connection with anchor point
A-165
Figure 9. Include deflections of bars above concrete level.
X – height at which anchor point is installed above concrete structure.
Y – deflection of horizontal lifeline in accordance with its instruction manual
8. Principles for use of personal fall protection equipment
Anchor point
A-165
must be used in accordance with instruction manuals for personal
fall protection equipment and standards:
EN 361 - for full body harness
EN 352-3; EN 355; EN 360 - for personal fall protection equipment
EN 362 - for connectors
EN 795 - for anchor points
·
personal fall protection equipment should be used only by personnel trained
in this respect.
·
personal fall protection equipment must not be used by a person with
medical condition that could affect the safety of the equipment user in normal and
emergency use.
·
prepare a rescue plan to be implemented whenever necessary.
·
it is forbidden to make any alterations or additions to the equipment without
the manufacturer's prior written consent.
·
any repair shall only be carried out by manufacturer of the equipment or his
certified representative.
·
personal fall protection equipment shall not be used for any purpose other
than intended.
·
personal fall protection equipment provides individual protection and shall be
used by one person only.
·
before each use make sure that all parts of the fall arresting system
cooperate correctly. Periodically examine connections and fitting of components of the
equipment to prevent any accidental loosening or disconnection.
·
it is forbidden to use a combination of equipment where function of any one
item is affected by, or interferes with the function of any other.
·
before each use of personal fall protection equipment, a pre-use check
should be carried out to ensure that it is in a serviceable condition and operates
correctly.
·
in particular, inspect all accessible elements of the equipment for any
damages, excessive wear, corrosion, abrasion, cutting or improper function. On
individual devices pay particular attention to:
-
in full body harness and work positioning devices: buckles, regulating
elements, attachment points (buckles), webbing, seams, belt loops;
-
in energy absorbers: attachment loops, webbing, seams, housing,
connectors;
-
in lanyards and textile guides: rope, loops, thimbles, connectors, regulating
parts, splices;
-
in lanyards and steel guides: rope, wires, clamps, loops, thimbles,
connectors, regulating parts;
-
in retractable type fall arresters: lanyard or webbing, retractor and locking
mechanism for proper operation, housing, energy absorber, connectors;
-
in guided type fall arresters: body, proper guiding, locking mechanism for
proper operation, rollers, bolts and rivets, connectors, energy absorber;
-
in connectors (snap hooks): load-bearing body, rivets, main pawl, function of
locking gear.
·
at least once a year, after each 12 months of use, personal fall protection
equipment must be withdrawn from use to carry out periodic detailed inspection. Periodic
inspection can be carried out by a properly trained and skilled person.
Periodic inspections can be carried out also by manufacturer of the equipment or his
authorized representative, or an authorized company. Inspect in detail all accessible
elements of the equipment paying attention to any damages, excessive wear, corrosion,
abrasion, cutting or incorrect function (see the above item.) In some cases, if the fall
protection equipment has a complex design (e.g. fall arresters), periodic inspections can
be carried out by manufacturer of the equipment, or his authorized representative only.
After the periodic inspection, date of the next inspection should be arranged.
·
regular periodic inspections are essential in respect of the equipment
condition and safety of users which is dependant on functionality and durability of the
equipment.
·
during periodic inspection it is necessary to check the legibility of all
markings on the equipment (identity label of the device).
·
all information on fall protection equipment (name, serial no., date of
purchase and date of first use, name of user, information on repairs and inspections and
withdrawal from use) must be provided in the identity card of the device. It is
responsibility of the user organisation to provide the Identity Card and to fill in the
required details. The Identity Card should be filled in by a person responsible for
protective equipment. It is forbidden to use personal fall protection equipment if the
Identity Card is not filled in.
·
if the product is re-sold outside the original country of destination the reseller
must provide instructions for use, for maintenance, for periodic inspection and for repair
in language of the country where the product is to be used.
·
personal fall protection equipment must be withdrawn from use immediately
if any doubts arise in regard of its condition, or proper operation. The device must not be
used until manufacturer of the equipment carries out a detailed inspection and gives his
written consent to use the equipment again.
·
personal protection equipment must be withdrawn from use immediately and
destroyed if it has been used to arrest a fall.
·
full body harness is the only acceptable device to be used to support the
user body in personal fall protection equipment.
·
in full body harness use only attaching points (buckles, loops) marked with
capital letter “A” to attach a fall protection system.
Anchor points (of devices) of the fall protection equipment should have a
stable structure and position so as to prevent a possibility of the load fall and minimize a
free fall distance. The equipment's anchor point should be located above the user's work
station. The shape and construction of the anchor device/point shall not allow for a self-
acting disconnection of the equipment. It is recommended to use certified and marked
anchor points of the equipment compliant with EN 795.
·
it is obligatory to verify the free space required under the user at workplace
before each occasion of using the personal fall protection system, so that, in case of a
fall, there is no collision with the ground or other obstacle in the fall path. The required
free space is specified in the instruction manual of the equipment to be used.
·
when using the equipment pay particular attention to hazardous situations
and environmental factors which may affect the performance of the device, and in
particular to:
·
- trailing or looping of device lanyards over sharp edges;
·
- pendulum falls;
·
- electrical conductivity;
·
- any damages such as cuts, abrasions, corrosion;
·
- extremes of temperature;
·
- negative influence of weather conditions;
·
- corrosive substances, chemicals, solvents, acids.
·
personal fall protective equipment must be transported in a package (e.g.:
bag made of moisture-proof textile or containers or boxes made of steel or plastic) to
protect it against damage or moisture.
·
personal fall protective equipment should be cleaned without causing
adverse effect on the materials used in the manufacture of the equipment. For textile
materials (webbings, ropes) use agents suitable for delicate fabrics. They can be hand-
or machine-washed, and then rinsed thoroughly. Wash textile products with water only.
When the equipment becomes wet, either from being in use or after cleaning, allow it to
dry naturally, and keep it away from a direct heat. In metallic products lubricate some
mechanical parts (springs, hinges, pawls, etc.) regularly to improve their operation.
·
personal fall protective equipment should be stored loosely packed in well-
3/4