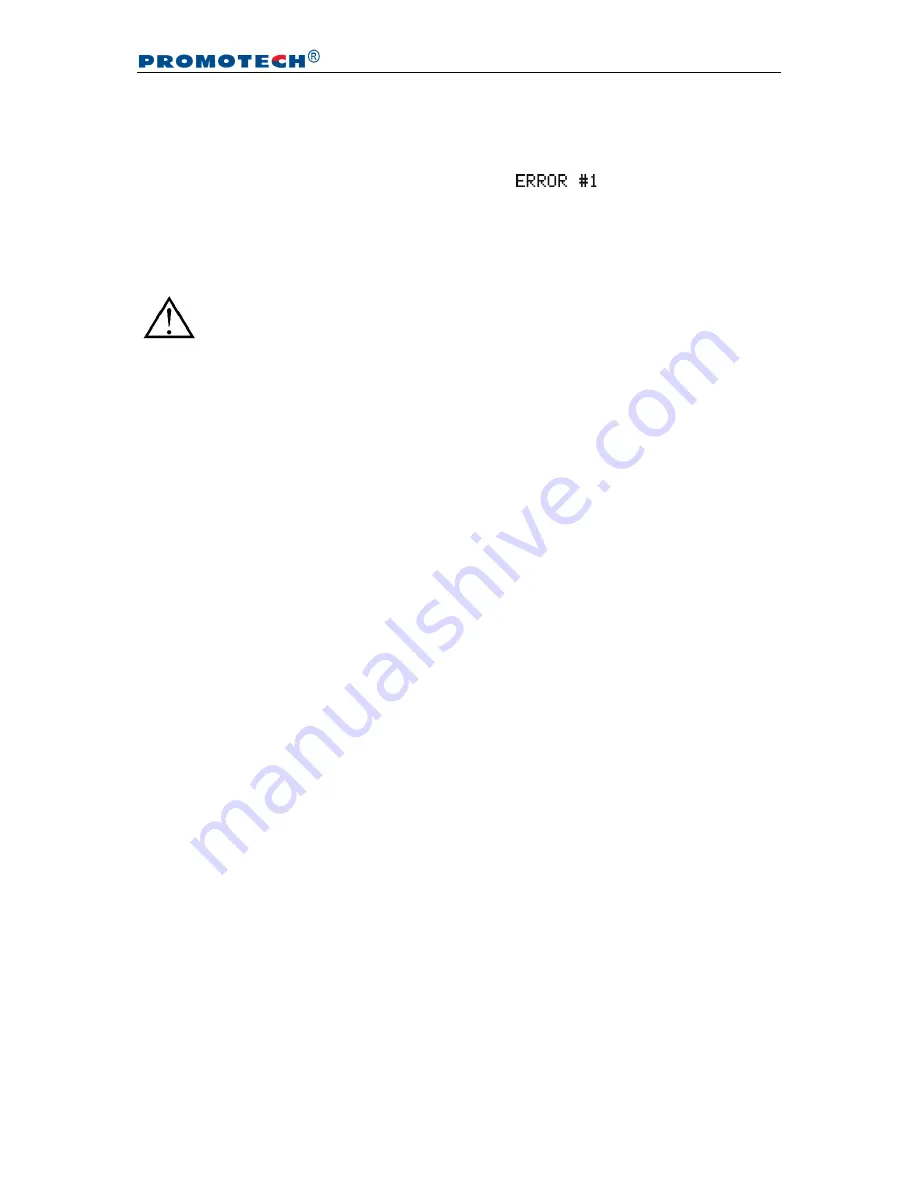
Rail Bull
This document is protected by copyrights.
Copying, using, or distributing without permission of PROMOTECH is prohibited.
15
3.6. Operating
Set the power switch to the position ‘I’, to turn on the carriage and start the
initialization of the control system. If the message
appears on the display,
set the travel direction switch to the
position ‘O’. Then, use the travel speed knob to
set the required speed of the carriage.
If the carriage is to control the torch, set the arc ignition switch to the
position ‘I’.
Use the travel direction switch to select a direction of motion, which will start the
movement of the carriage with the speed shown on the display. The speed can be
adjusted at any time.
To stop the motion, set the travel direction switch to the
position ‘O’.
After the work is finished, turn off the power with the power switch and unplug the
carriage from the power source.
If the arc ignition switch is set to the
position ‘I’, the torch starts welding
/ plasma cutting immediately after selecting a travel direction.