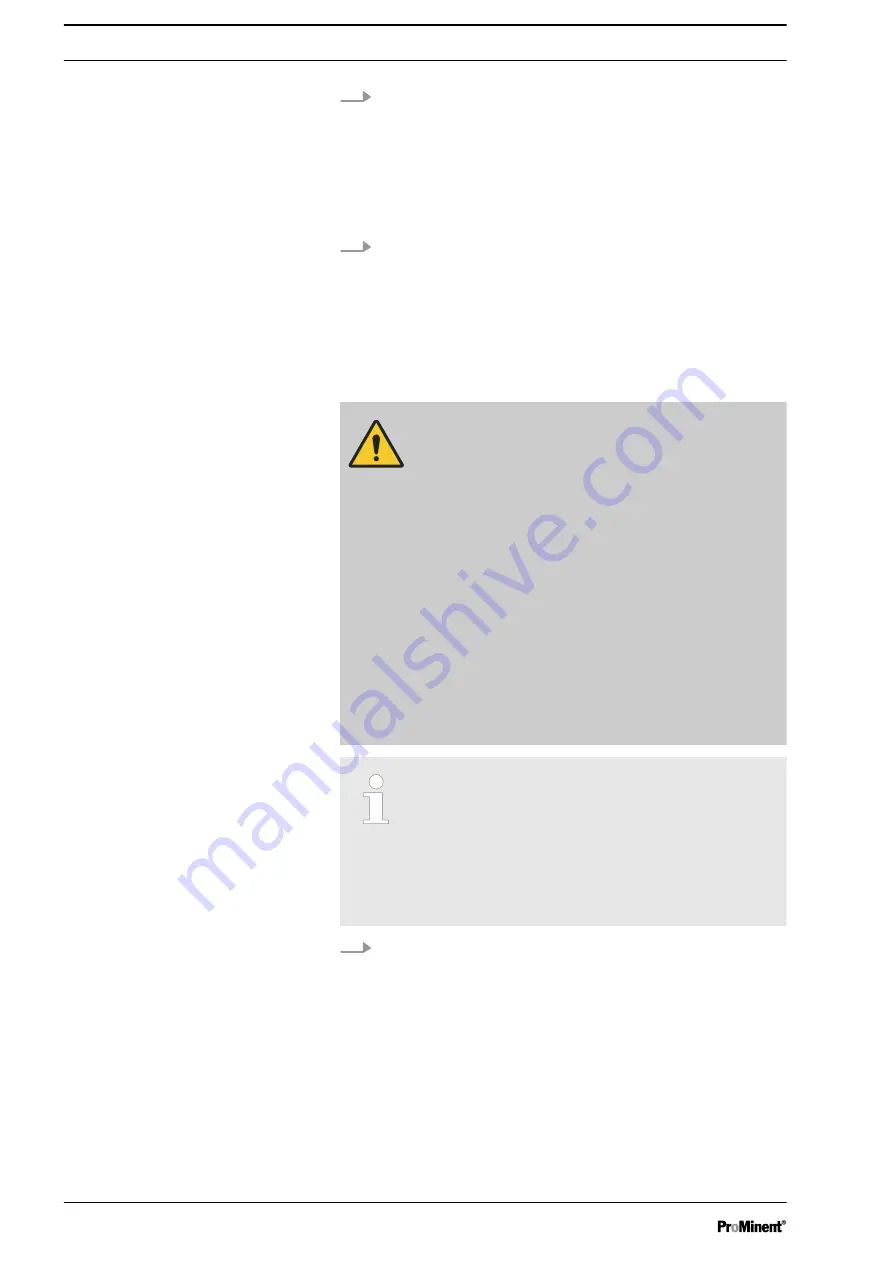
6.
Run the metering pump for a few minutes to allow all air bub‐
bles to escape from the metering system. Set the pump to
the required metering volume. You can adjust the pump
output by changing the stroke rate and stroke length.
ð
If the discharge line is routed into a collecting tank, you
can measure the metered volume to determine a
metering volume. Switch off the metering pump again
afterwards.
7.
Drain the metering system and fully remove water and con‐
taminants from the metering system. The metering system
can be drained by blowing compressed air through the lines.
Do not allow the air pressure to exceed the metering sys‐
tem's permissible operating pressure.
5.4 Connecting the Chemical Tank for Commissioning
WARNING!
Danger from hazardous substances!
Possible consequence: Fatal or very serious inju‐
ries.
Please ensure when handling hazardous sub‐
stances that you have read the latest safety data
sheets provided by the manufacture of the haz‐
ardous substance. The actions required are
described in the safety data sheet. Check the
safety data sheet regularly and replace, if neces‐
sary, as the hazard potential of a substance can be
re-evaluated at any time based on new findings.
The system operator is responsible for ensuring
that these safety data sheets are available and that
they are kept up to date, as well as for producing
an associated hazard assessment for the worksta‐
tions affected.
Pay attention to the information in the operating
instructions for the respective metering pumps.
The metering pumps are self-priming and prime
the feed chemical into the metering line on the dis‐
charge side.
Fully bleed the metering line for trouble-free
metering and fill with feed chemical.
Following a successful test run with distilled water, reinstall
all connectors as they need to be for normal operation. Fully
remove any temporary installations, if any are fitted. Set up
the installations for proper operation.
Draining the metering system
Commissioning
26