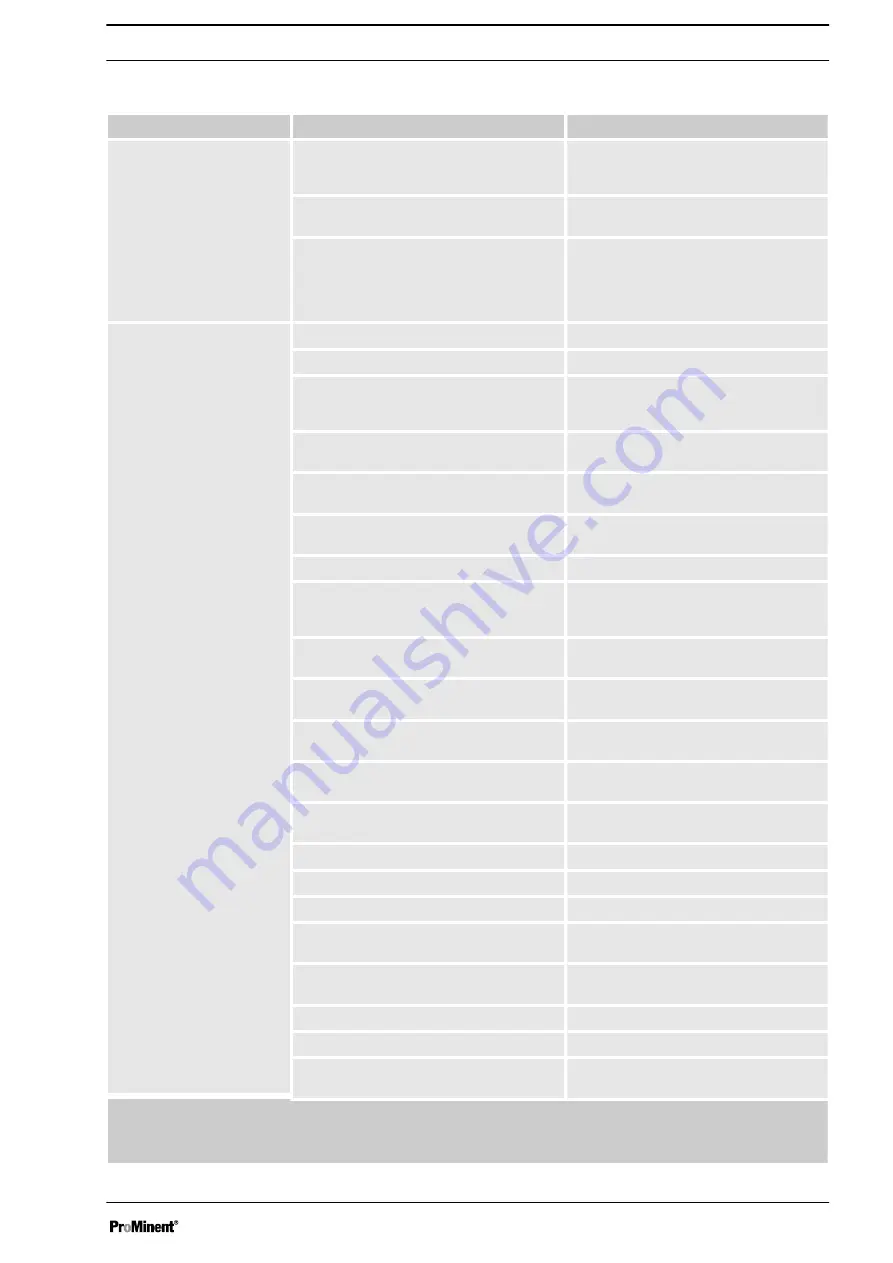
7.2 Troubleshooting
Fault
Possible cause
Remedy
Suction line contains gas
bubbles
Priming lift too high, operating conditions
too close to the vapour pressure of the
medium
Reduce priming lift, use automatic gas
release, reduce temperature
Suction line leaks and is drawing air
Check negative pressure tightness and
connections, bleed line
Medium tends to be gaseous
Automatic gas release at the highest point
and in the dosing head, always lay suc‐
tion lines at a continuous incline, avoid
higher temperatures and UV radiation,
flush suction connector
Metering pump is not
pumping or indicates
decreased capacity
Suction line contains gas bubbles
See separate fault indication
Suction line is blocked
Remove blockage / dirt
Suction pressure required is too high
Modify suction line, use a wider cross-
section and/or use a priming pulsation
damper
Suction line contains gas bubbles
Bleed at the highest point, lay suction line
with a continuous incline
Flushing or drain open on the suction side
Close flushing or drain tap on the suction
side
Shut-off valve on the evacuation tank not
closed
Close fitting and, if required, re-evacuate
the suction line
Tank and/or priming lift too high
Use priming aid
Empty alert and/or low flow contact trig‐
gered
Top up chemicals into the storage tank:
make sure that the level sensor is
immersed in the medium
Ball jammed/stuck in the metering pump
suction or discharge valve
Dismantle, clean and, if required, replace
valve
Ball dissolved in the suction or discharge
valve
Replace valve and check resistance
Diaphragm tear / diaphragm rupture sensor
activated
Replace diaphragm and sealing set
Opening pressure of the relief valve / safety
valve too low
Correctly set the opening pressure
Open flushing and drainage connection on
the discharge side
Close flushing and drainage connection
Air in the discharge line
Bleed metering line at the highest points
Metering line ruptured
Correctly repair the metering line
Shut-off valve closed (discharge side)
Open shut-off valve
Metering line blocked
Rectify blockage, check opening pressure
of the relief valve and/or safety valve
Back pressure too high at the injection point Reduce back pressure or replace pump
with a higher capacity
Injection point blocked
Clean injection point
Voltage drop or failure
Reconnect the power supply
Cable for power supply is not correctly con‐
nected
Ensure correct power supply through
measurement
The table does not claim to be complete.
Further reasons for failure and detailed information on the causes of faults can be found in the operating instructions
for the individual components.
Maintenance and Troubleshooting
37