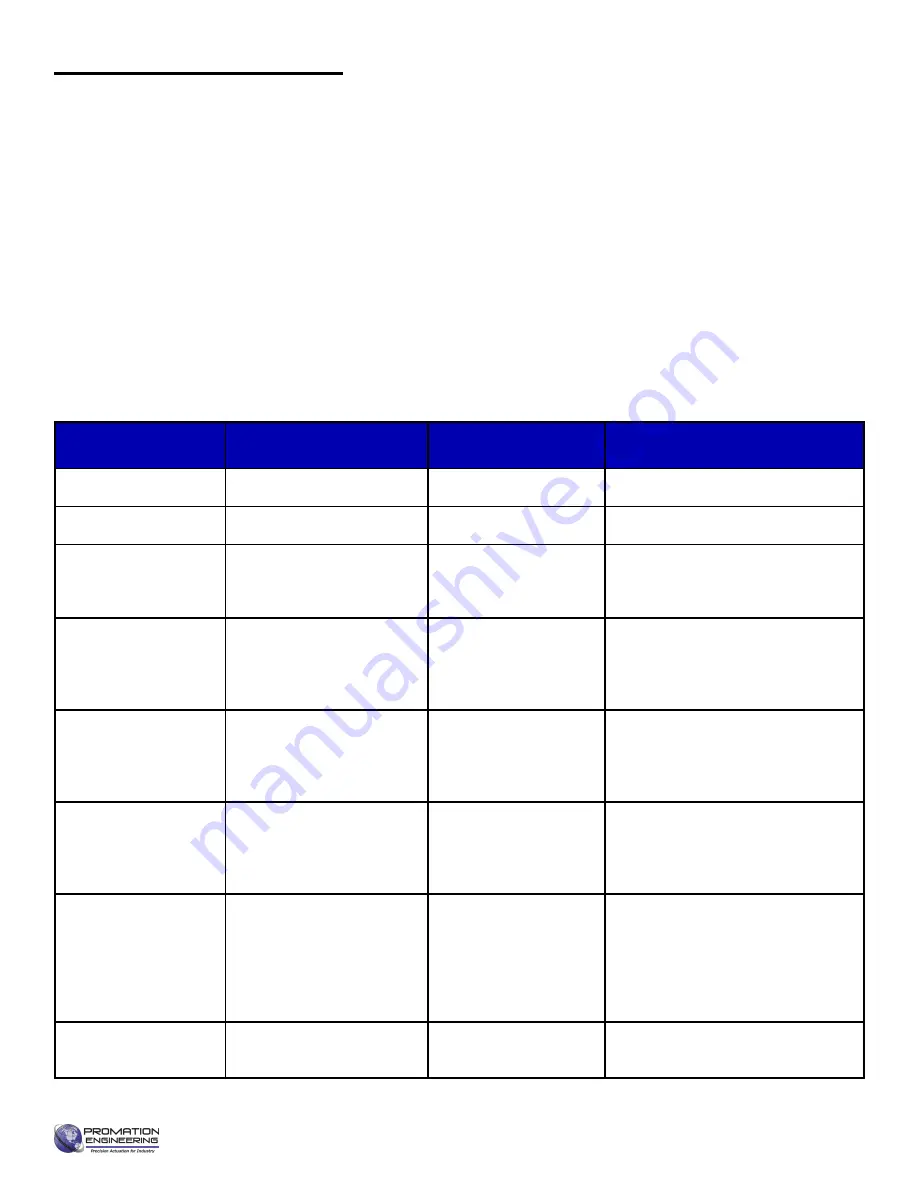
Condition
Control Card
Indicator
Status
Description
Power On (DIP 5 on)
Yellow LED On Steady
Normal Operation
Board has power
Power On (DIP 5 on)
Blue LED Blinking at 1 Hz
Normal Operation
Control Signal received at terminal
Power On (DIP 5 on)
Blue LED Flashes 3 times
rapidly followed by a one
second pause
Invalid Control
Signal
No or Low Control signal.
Check incoming control signal.
Power On (DIP 5 on)
Blue LED Flashes 3 times
rapidly followed by a one
second pause AND
Orange LED On
Invalid Control
Signal
Control (4-20mA) input wires
reversed (minimum 12mA signal
needed). Reverse Control Leads.
Power On (DIP 5 on)
No Motor Movement
Blue LED Flashes 4 times
rapidly followed by a one
second pause
Motor Stall
Feedback Potentiometer does not
sense movement. Check for Motor
problem. Inspect for loose gears,
potentiometer, wiring, etc
Power On (DIP 5 on)
Blue LED Flashes 5 times
rapidly followed by a one
second pause
Potentiometer Fault
Incorrect potentiometer adjustment
prior to running AutoCalibration.
Adjust Feedback Potentiometer
values to be in range.
Power On (DIP 5 on)
Blue LED Flashes 5 times
rapidly followed by a one
second pause
Travel Fault
Potentiometer Fault during
Calibrate Feedback step of
AutoCalibration. Adjustments to
End of Travel cams have set the
rotation for >90° travel. Reset to
90° travel and AutoCalibrate.
Power On (DIP 5 on)
No Motor Movement
Red or Green Motor
Direction LEDs Flash
Low Power
Incoming Power too low
The actuators are tested, calibrated and shipped in the Full CW position in the Direct Acting mode (CW is 4mA, CCW is
20mA). End of Travel cams are set at 90 degrees from each other.
A. Set the control device (valve or damper) to the closed position.
B. Mount the actuator to the device to be controlled (valve or damper).
C. Insure that the CW End of Travel cam trips the CW End of Travel switch at the correct CW point.
C.1. If the switch does not change state at the correct CW position, adjust Cam #2 per instructions on page 7.
D. Manually move (see Manual Override on page 8) the actuator so the valve or damper is in the fully CCW position. This
must be ≤ 90° of the full CW position.
E. Insure that the CCW End of Travel cam trips the CCW End of Travel switch at the correct CCW point.
E.1. If the switch does not change state at the correct CCW position, adjust Cam #1 per instructions on page 7.
If the End of Travel cams are adjusted at all, the actuator must be recalibrated.
F. Test actuator and device with a control input signal to insure that control signal corresponds to correct actuator and
device position.
Check End of Travel Settings
FM14_P1A
L
V VN4 V
er J 101614
Page 6 of 14 P1.A LV AdVanced Proportional Series
Check End of Travel Settings