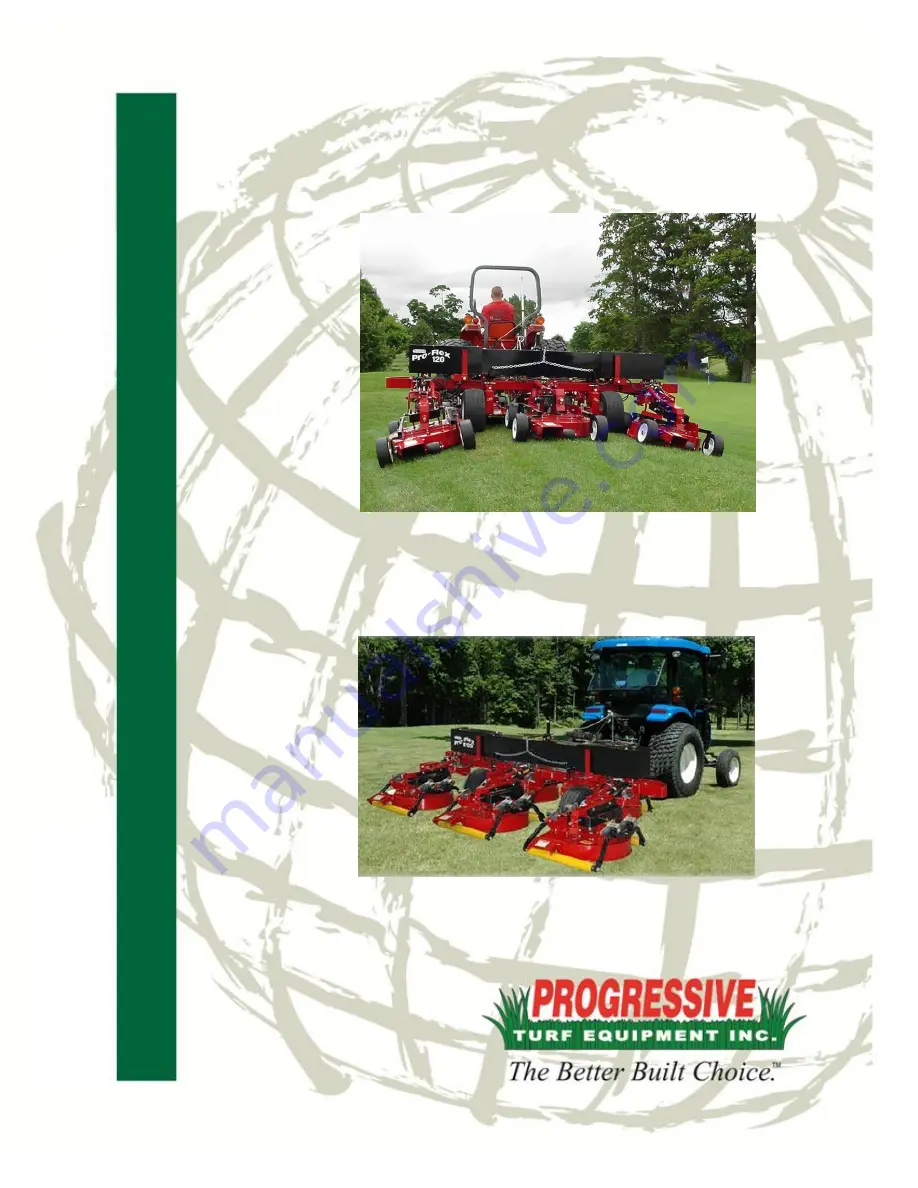
O
perator’s Manual & Parts List
Pro-Flex 120
Serial No. 14272040 to 15272164
Pro-Flex Roller 120
Serial No. 15101019 and up
PROGRESSIVE TURF EQUIPMENT INC.
137 WEST WILLIAM STREET
SEAFORTH, ONTARIO
CANADA N0K 1WO
TOLL FREE: 800 668-8873
ISSUE DATE: November, 2014
P.N. 120534
www.progressiveturfequip.com
Summary of Contents for Pro-Flex 120
Page 2: ......
Page 4: ......
Page 50: ...Pro Flex 120 Series Parts List ...
Page 52: ...Pro Flex 120 Series Parts List 48 ...
Page 56: ...Pro Flex 120 Series Parts List 52 1 2 BLADE OPTIONS 05 2016 ...
Page 58: ...Pro Flex 120 Series Parts List 54 1 4 DECK ARM ASSEMBLIES 11 2014 11 2014 ...
Page 59: ...Pro Flex 120 Series Parts List 55 1 5 DRIVE BELTS 11 2014 ...
Page 60: ...Pro Flex 120 Series Parts List 56 1 6 BELT DRIVE ASSEMBLY LEFT 11 2014 ...
Page 61: ...Pro Flex 120 Series Parts List 57 1 7 BELT DRIVE ASSEMBLY RIGHT 11 2014 ...
Page 65: ...Pro Flex 120 Series Parts List 61 3 HYDRAULICS 11 2014 ...
Page 66: ...Pro Flex 120 Series Parts List 62 4 DRIVELINE 4 1 INPUT DRIVELINE 01 2015 ...
Page 67: ...Pro Flex 120 Series Parts List 63 4 2 DRIVELINE GUARDING 11 2014 ...
Page 68: ...Pro Flex 120 Series Parts List 64 4 3 INPUT PTO SHAFT 11 2014 ...
Page 69: ...Pro Flex 120 Series Parts List 65 4 4 INTERMEDIATE PTO SHAFT 11 2014 ...
Page 70: ...Pro Flex 120 Series Parts List 66 4 5 GEARBOX 11 2014 ...
Page 71: ...Pro Flex 120 Series Parts List 67 5 WHEEL ASSEMBLIES 5 1 WHEEL ASSEMBLIES 05 2015 ...