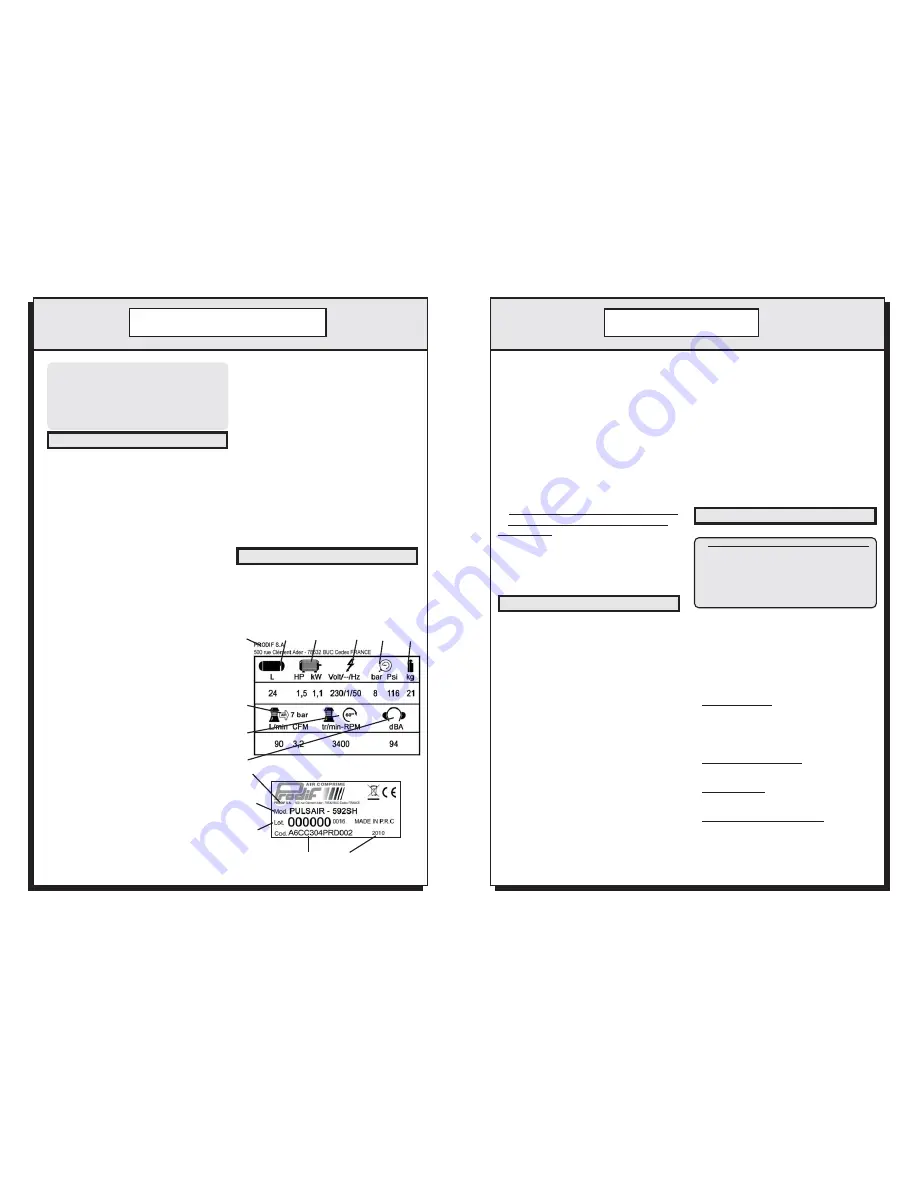
5
2
4 - MAINTENANCE
Before any intervention on the compressor:
- Disconnect electrical cable.
- Empty the tank.
- Let cool the compressor.
A regular maintenance ensures working
without problem and increases the longevity
of the compressor.
FOR HANDLING: do not carry the compressor,
use the wheels (not the handles).
See table of the programmed maintenance(page 3)
Purge condensates: Advised after each use:
Purge to avoid the corrosion of the tank, .see (fig. 3).
These condensates contain oil , so you must recover
the condensates in a suitable container not to reject
into the sewers.
Clean or change the air filter: To guarantee the flow
of the compressor.( Fig. 7)
controls checking: By the tank pressure gauge,
check maximum value of the compressor.
Electric connector blocks checking: Tighten
correctly electric wires to have a good engine power.
3 - FOR YOUR SECURITY
The air delivered by your compressor allows you
to use many tools, follow conditions, advice and in
certain cases RESTRICTIONS OF USE for air tools
using compressed air.
Avoid any degradation of the electric cable and
move away from heat sources higher than 70°C.
At the end of work, unplug the cable and roll up it
around the handle of the compressor.
Do not use the compressor with bare or wet feet.
Do not to touch the compressor with wet hands.
Do not pull the cord to move the compressor or
to remove the plug.
Do not allow children to use the compressor.
Do not leave the compressor without monitoring
when it is connected; it can become source of
dangers.
Never introduce objects into the protection of the
transmission system.
- AFTER USING:
Never stop by disconnecting the electrical cable.
Never leave the compressor power connected
under pressure.
Switch the interruptor in "Off" position . (Fig. 2)
Empty the tank
Drain the tank (Fig.3)
Disconnect the electrical cable.
Ordinary maintenance does not require
specialized personnel.
The servicing of the group of compression as
well as other more complex bodies, must be
carried out by specialized personnel: Call for your
retailer.
The compressor does not start:
No electrical supply.
The compressor is already in pressure, empty
the tank.
The pressure switch is defective.
The compressor starts with difficulty, and
thermal protection sometimes operates:
The electric tension is insufficient. (210V
Minimum).
Electrical supply cord is too long, or wire section
too small. (electric cable coil)
Engine overload by cold weather.
Electrical supply cord is cut or disconnected.
You stopped your compressor by disconnecting
the cable and decompression did not take place.
Decompression defect, the tank is full, the
decompression did not take place.
(Check: Correct restarting with empty tank).
High resistance of the group: after removing air
filter, pour 4 to 5 drops of engine lubricating oil at
the air entry of the compressor and make the
compressor working during one minute, in order to
deposit an oil film in the mechanism.
Thermal protection is out of order, needs to be
regulated or changed according to the type.
Abnormal noises, vibrations:
Loosened or worned parts.
Worn group (mechanical noises).
Bad chocking of the compressor.
Tension of the belt to be checked.
Air leakage in the pneumatic circuit.
Opening of the safety valve:
Bad adjustment of the pressure controller, you
need to check that pressure gauge A ( Fig. 4) does
not exceed the pressure indicated on the identifica-
tion plate, this must be regulated by a specialist.
The safety valve is badly regulated or is
defective, to be replaced by an approved
equivalent model.
5 - FAULTS / SOLUTIONS
Air leaking from the valve of air pressure switch :
- defective valve of the pressure switch, change it.
No return valve blocked by an impurity or worn,
clean or change the no return valve or the internal
rubber valve with its spring. ( Fig. 9)
Low flow rate, pressure does not increase:
air filter is dirty, you must clean it.(Fig. 7)
air pressured is leaking by the connections, check
the connections.
Cylinder valves are broken or valve seat gasket
torn, you must check the pump.
Excessive consumption by the segmentation,
gasket leakages, you must check the pump.
Impossible adjustment of the output air pressure:
The internal diaphragm of the pressure reducer is
torn (fig.4) replace it.
Please follow the advice below for the mainte-
nance of your compressor:
FAULTS / SOLUTIONS
COMMUNICATION- TRACKING PRODUCT
SECURITY
MAINTENANCE
To use your compressor correctly, only use it
intermittently, i.e. 60% of use for 40% of downtime.
Beyond this limit, the engine risks overheating
problems.
- PRECAUTIONS TO PAINT:
If the electric motor and the interior of the pump are
dirty, your compressor life expectancy will be
reduced:
In order to avoid this problem, only move away
the compressor by lengthening the tube of your tool.
The electric safety of this machine is assured only
when it is correctly connected with an efficient
grounding connection , as recommended in the rules
of electric safety requirements.
The responsibility for the manufacturer will not be
committed if grounding connection of the installation
is incorrect.
To avoid burns, during the work and a few minutes
after working, never touch the pipes of connection of
the cylinder head, the non-return valve nor the parts
of the compressor subjected to heating.
- OPERATING TIME:
For any communication with the distributor, please
indicate the identification sticker data of the
product [fig.1] The sticker is applied on the side of
the compressor.
IDENTIFICATION STICKER OF THE PRODUCT
[fig.1]
6 - COMMUNICATION- TRACKING PRODUCT
1 2 3 4 5 6
7
8
9
1
12
10
11 13