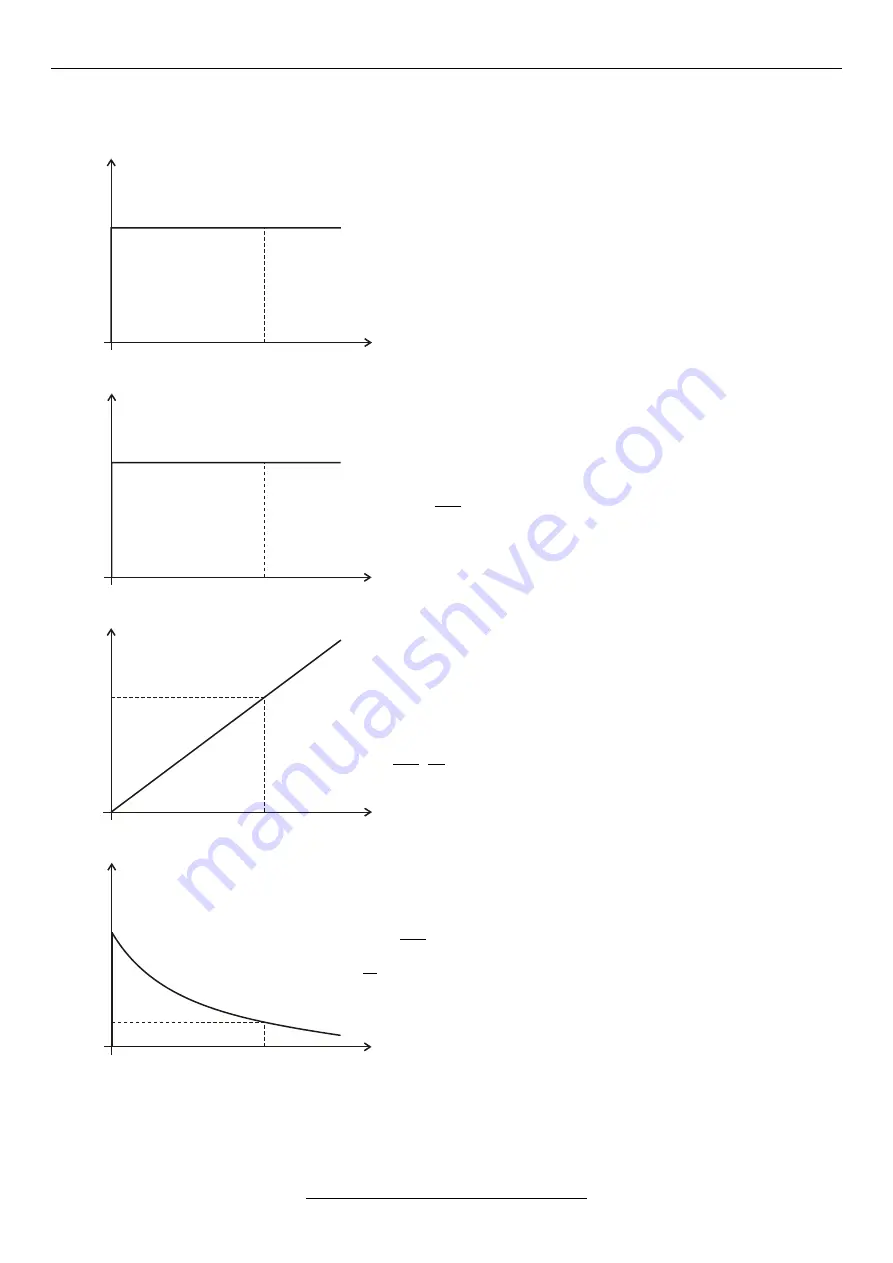
H - I - J
PROGRAMMER’S MANUAL
V8.94.11-
- 24 -
An example for the regulation
At setting the PID parameters be very careful,
because the quality of the regulation depends on
this setting!
Prior to setting the parameters, clarify if the job
needs proportional regulation, PI regulation or really
a PID regulation?
The absolute limitation of the output frequency (f) is
built into the regulator therefore at reaching the limit
the I element will not be integrated off!
The limitation of the acceleration and deceleration
slopes of the output frequency (f) is independent of
the regulator. Setting wrong parameters (e.g. too
large deceleration time and short integration time)
may cause the regulator to be integrated off thus the
system to swing over.
Some hints
P (proportional): For simple regulations (e g. fluid
level regulation) it is practical to use proportional
regulation.
Thus, the set-in process is the fastest and there is
no tendency to swinging.
The regulation works with the minimum error (due
to the regulation being proportional to the error
signal) but this is not essential at these kinds of
applications. (Ti=N, Ad=0)
The PI regulation can be used at regulation tasks of
relatively high time constant.
(e g. pressure regulation with pumps or temperature
regulation with blowers etc.) (Ad=0)
PID regulation has to be used for fast regulations.
(e g. regulation of the rotation speed)
At adjusting Ad and Td special care has to be taken
to avoid swingings but maintain the speed of the
regulation!
Error signal
h
1
t1
t
f
p
t1
t
f 1
p
P
f
i
t1
t
I
f 1
i
f
d
t1
t
D
f 0
d
f 1
d
(
)
P
min
max
min
P
A
100
1
h
f
f
f
1
f
−
+
=
(
)
D
min
max
D
A
100
1
h
f
f
0
f
−
=
D
T
1
t
D
D
e
0
f
1
f
−
=
(
)
1
T
1
t
100
1
h
f
f
1
f
min
max
I
−
=
Summary of Contents for V3D Series
Page 2: ......
Page 85: ...H I J PROGRAMMER S MANUAL V8 94 11 85 User settings Submenu Explanation Setting Unit...
Page 86: ...H I J PROGRAMMER S MANUAL V8 94 11 86 Notes...
Page 87: ......