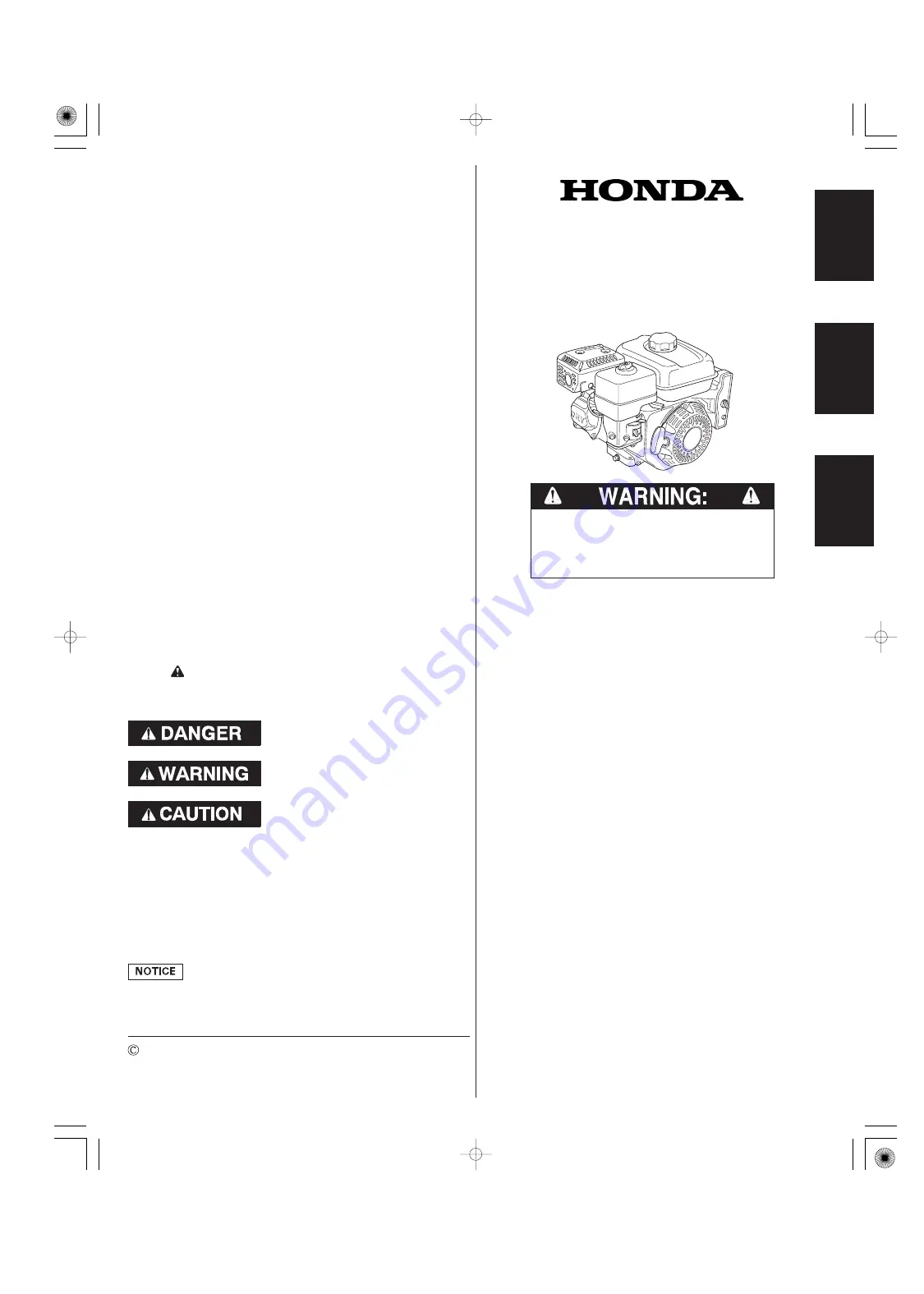
−
INTRODUCTION
SAFETY MESSAGES
CONTENTS
ENGLISH
FR
ANÇ
A
IS
ESPAÑOL
ENGLISH
OWNER’S MANUAL
MANUEL DE L’UTILISATEUR
MANUAL DEL PROPIETARIO
DAMAGE PREVENTION MESSAGES
GX120 · GX160 · GX200
1
Thank you for purchasing a Honda engine. We want to help you to
get the best results from your new engine and to operate it safely.
This manual contains information on how to do that; please read it
carefully before operating the engine. If a problem should arise, or
if you have any questions about your engine, consult an
authorized Honda servicing dealer.
All information in this publication is based on the latest product
information available at the time of printing. Honda Motor Co., Ltd.
reserves the right to make changes at any time without notice and
without incurring any obligation. No part of this publication may
be reproduced without written permission.
This manual should be considered a permanent part of the engine
and should remain with the engine if resold.
The engine exhaust from this product
contains chemicals known to the State of
California to cause cancer, birth defects
or other reproductive harm.
The purpose of these messages is to help prevent damage to your
engine, other property, or the environment.
Your engine or other property can be damaged if you
don’t follow instructions.
This word means:
You will also see other important messages that are preceded by
the word NOTICE.
Each message tells you what the hazard is, what can happen, and
what you can do to avoid or reduce injury.
You CAN be HURT if you don’t follow
instructions.
You CAN be KILLED or SERIOUSLY
HURT if you don’t follow instructions.
You WILL be KILLED or SERIOUSLY
HURT if you don’t follow instructions.
These signal words mean:
A safety message alerts you to potential hazards that could hurt
you or others. Each safety message is preceded by a safety alert
symbol
and one of three words, DANGER, WARNING, or
CAUTION.
Your safety and the safety of others are very important. We have
provided important safety messages in this manual and on the
engine. Please read these messages carefully.
Review the instructions provided with the equipment powered by
this engine for any additional information regarding engine
startup, shutdown, operation, adjustments or any special
maintenance instructions.
We suggest you read the warranty policy to fully understand its
coverage and your responsibilities of ownership. The warranty
policy is a separate document that should have been given to you
by your dealer.
United States, Puerto Rico, and U.S. Virgin Islands:
.......................
INTRODUCTION
.1
................
SAFETY MESSAGES
.1
..........
SAFETY INFORMATION
.2
...
SAFETY LABEL LOCATIONS
.2
COMPONENT & CONTROL
..............................
LOCATIONS
.3
................................
FEATURES
.3
BEFORE OPERATION
....................................
CHECKS
.4
..............................
OPERATION
.4
SAFE OPERATING
.....................
PRECAUTIONS
.4
......
STARTING THE ENGINE
.4
......
STOPPING THE ENGINE
.6
.....
SETTING ENGINE SPEED
.6
.....
SERVICING YOUR ENGINE
.7
THE IMPORTANCE OF
....................
MAINTENANCE
.7
......
MAINTENANCE SAFETY
.7
.......
SAFETY PRECAUTIONS
.7
MAINTENANCE
............................
SCHEDULE
.7
...........................
REFUELING
.8
...........................
ENGINE OIL
.8
............
Recommended Oil
.8
..................
Oil Level Check
.9
.........................
Oil Change
.9
.........
REDUCTION CASE OIL
.9
............
Recommended Oil
.9
..................
Oil Level Check
.9
.......................
Oil Change
.10
......................
AIR CLEANER
.10
........................
Inspection
.10
..........................
Cleaning
.11
2011 Honda Motor Co., Ltd.
All Rights Reserved
..................
SEDIMENT CUP
.12
......................
SPARK PLUG
.12
.............
SPARK ARRESTER
.13
.........................
IDLE SPEED
.13
HELPFUL TIPS &
......................
SUGGESTIONS
.13
...
STORING YOUR ENGINE .13
................
TRANSPORTING
.14
TAKING CARE OF
....
UNEXPECTED PROBLEMS
.15
........
FUSE REPLACEMENT
.15
..
TECHNICAL INFORMATION .16
.....
Serial Number Location
.16
Battery Connections for
....................
Electric Starter
.16
.....
Remote Control Linkage
.16
Carburetor Modifications for
.....
High Altitude Operation
.17
Emission Control System
.........................
Information
.17
..............................
Air Index
.18
.....................
Specifications
.18
........
Tuneup Specifications
.19
Quick Reference
.........................
Information
.19
................
Wiring Diagrams
.19
.
CONSUMER INFORMATION .20
Warranty and Distributor/
Dealer Locator
.........................
Information
.20
Customer Service
.........................
Information
.20
37Z4M600
00X37-Z4M-6001
GX120UT2·GX160UT2·GX200UT2
·GX120RT2·GX160RT2·GX200RT2
11/07/04 17:14:33 32Z4M600_001
Summary of Contents for 51700004
Page 30: ......
Page 53: ...2 A B G H E D C F 3 7 7 8 17 16 14 ...