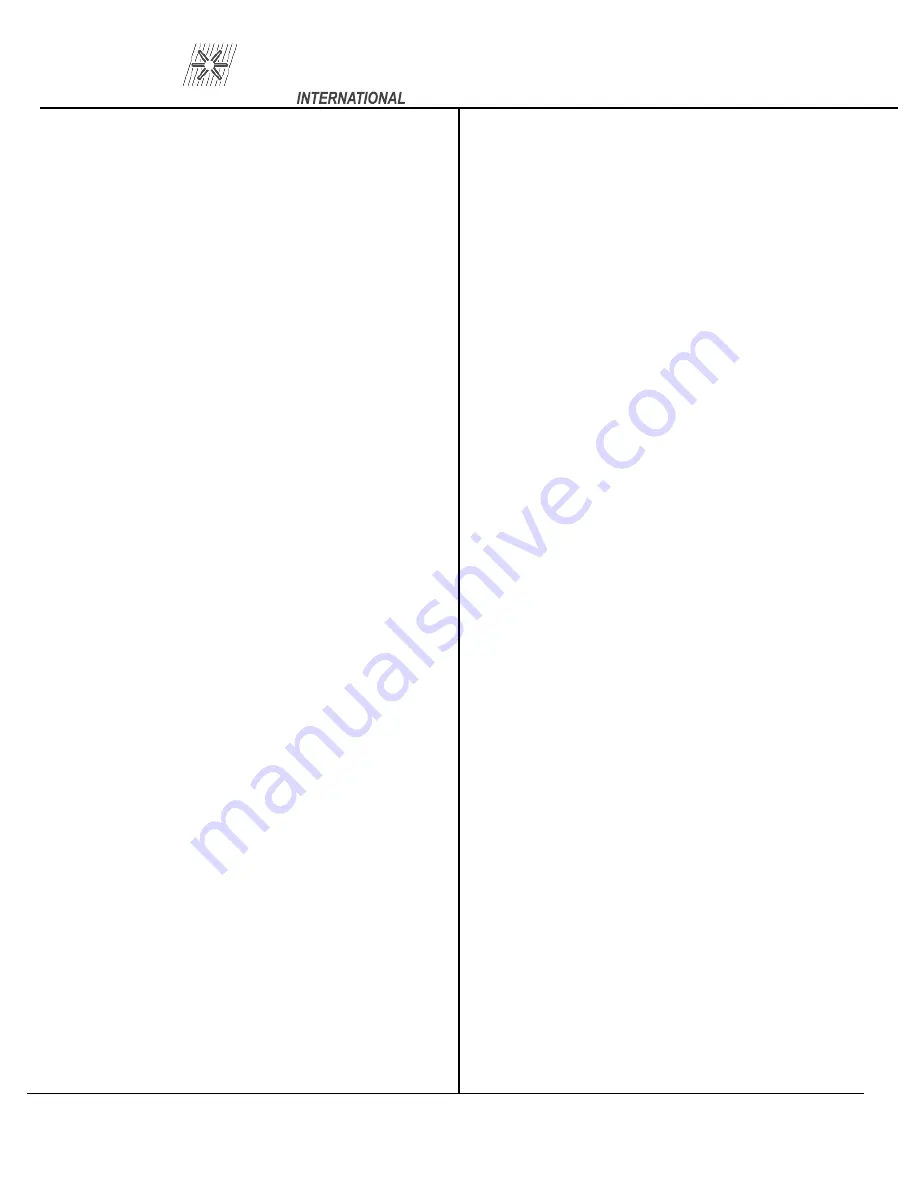
CD -2 1 2 P
PRO WEL D
1.0 INTRODUCTION
Your new stud welding equipment is carefully
constructed of the finest components and materials
available. Used properly, this equipment will give
you years of profitable, efficient service.
The system incorporates the latest in engineer-
ing advances, for completely reliable end welding of
mild steel, stainless steel, aluminum and lead free
copper and brass fasteners.
A careful study of this manual will enable you
to understand how the welder operates to insure
proper performance under all operating conditions.
2.0 WARRANTY
The electrical and mechanical components of
the stud welder are thoroughly performance in-
spected prior to assembly in the welder. The assem-
bled welder is completely performance checked. The
welder is delivered to you in functional electro-
mechanical condition.
All parts used in the assembly of the welder
and its accessories are fully warranted for a period of
1 YEAR from the date of delivery. In addition, the
welding capacitors are warranted for a period of 1
YEAR from the date of delivery. The printed circuit
boards used in all proweld equipment are warranted
for a period of 3 years.
Under the warranty, the manufacturer reserves
the right to repair or replace, at their option, defec-
tive parts which fail during the guarantee period.
Notice of any claim for warranty repair or replace-
ment must be furnished to the manufacturer by the
purchaser within ten (10) days after the defect is first
discovered. The manufacturer does not assume any
liability for paying shipping cost or any labor or ma-
terials furnished where such cost are not expressly
authorized in writing.
The manufacturer does not warrant any parts or
accessories against failures resulting from misuse,
abuse, improper installation, maladjustment, or use
not in accordance with the operating instructions fur-
nished by the manufacturer. The warranty is valid
only when studs are purchased from sources ap-
proved by the manufacturer or are of identical speci-
fications to the manufacturer’s
3.0 UNPACKING YOUR UNIT
Upon receipt of your unit, place it as close as
possible to the point of installation before unpacking
it. Do not operate the unit from an extension power
cord if possible. Once the unit is unpacked it is recom-
mended that you inspect it for any physical damage.
Your unit has been completely assembled and
inspected at the factory. Upon receipt, the unit must be
hooked up to the recommended incoming power be-
fore welding. We recommend that you check that you
have received all the items listed on the shipping
check list. (see SECTION 18 or 19)
Place the unit in a large enough area to provide
adequate ventilation. Do not restrict the air flow
through the side louvers. Do not allow water to enter
the control housing.
4.0 SUGGESTED SAFETY PRECAU-
TIONS
In any welding operation, it is the responsibil-
ity of the welder to observe certain safety rules to in-
sure his personal safety and to protect those working
near him.
Reference is directed, without endorsement or
recommendation, to ANSI Z49.1, Safety in Welding
and Cutting, and to AWG Publication A6,1-66, Rec-
ommended Safety Practices for Gas-Shield Arc Weld-
ing.
1. Always treat electricity with respect. Under
open circuit conditions, the welding machine
output voltage may be dangerous.
2. Don’t work on live circuits or conductors.
Disconnect the main power line before check-
ing the machine or performing any mainte-
nance operations.
3. Be sure the welding machine cabinet is
properly grounded to a good electrical ground.
4. Don’t stand in water or on a damp floor
while welding or weld in the rain. Avoid wear-
ing wet sweaty cloths when welding.
PAGE 1
Summary of Contents for CD-212P
Page 1: ...OPERATION MAINTENANCE MANUAL...
Page 2: ......
Page 5: ...CD 212P PRO WELD...
Page 6: ...CD 212P PRO WELD...
Page 7: ...CD 212P PRO WELD...
Page 8: ...CD 212P PRO WELD...
Page 19: ...CD 212P PRO WELD PAGE INTENTIONALLY LEFT BLANK...
Page 20: ...CD 212P PRO WELD Figure 10 Light Duty CD Gun PAGE 11...
Page 31: ......