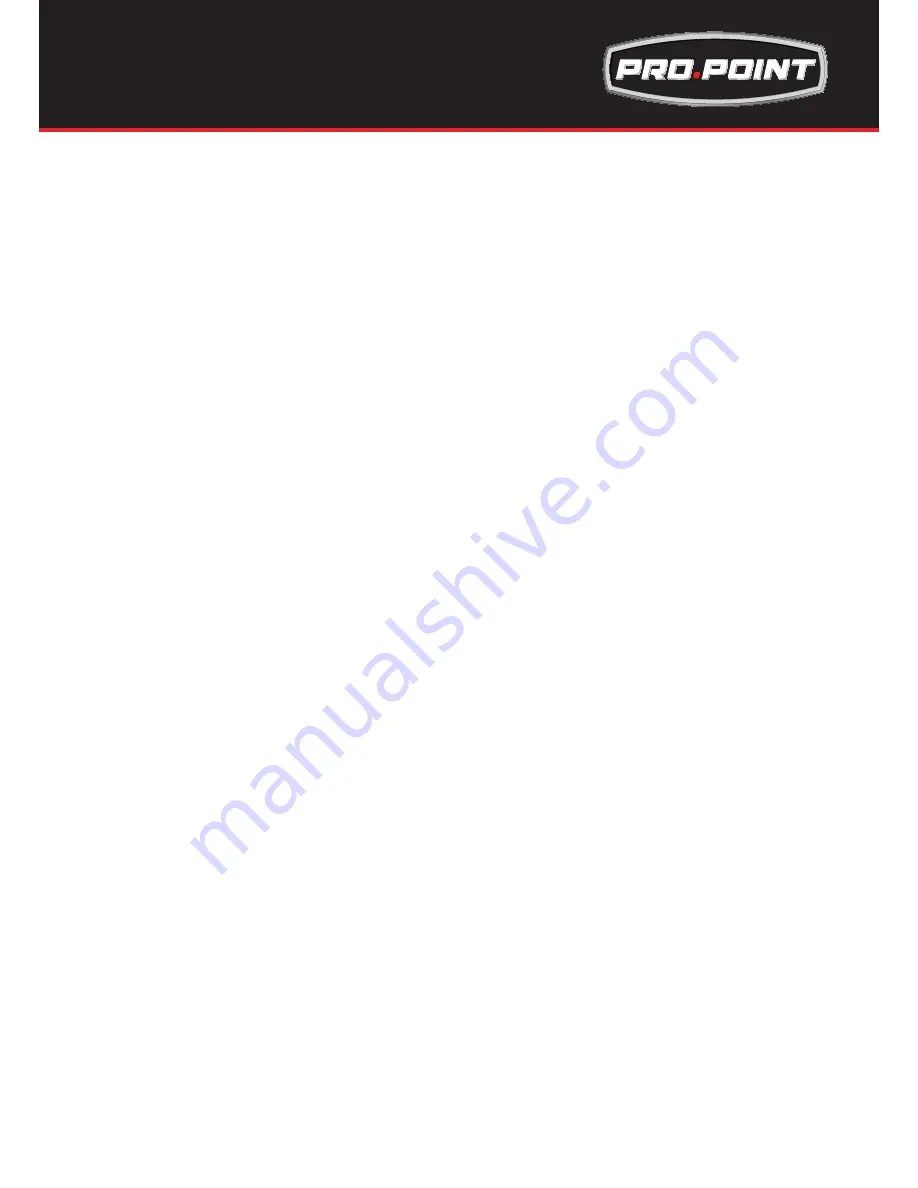
3
CONTENTS PAGE
Warranty
2, 47
Safety - Cautions
4-6
Technical Data, Product Information for Pro.Point 145
7
Technical Data, Product Information for Pro.Point 180
8
Machine Pro. Point 145/180 Layout
9
Installation & Operation for Pro.Point 145/180 ARC (stick) Welding
10
ARC (Stick) Welding Information
11-12
Installation & Operation for Pro.Point 145/180 MIG Welding with Gas
13-14
Wire Feed Drive Roller Selection
15
Wire Installation for Pro.Point 145/180 Set up Guide
16
Installation & Operation for Gasless MIG Welding for Pro.Point 145/180
17-18
MIG Torch Liner Installation
19
MIG Torch and Wire Feeder Set Up Guide for Aluminum Wire
20-21
Installation & Operation for MIG Welding with Spool Gun
22-23
Basic MIG Welding Guide
24-29
Installation & Operation for DC TIG Welding
30-31
TIG Fusion Technique
32
Tungsten Electrodes & Preparation
33-34
TWECO
®
2 MIG Welding Torch Parts Breakdown & Spare Parts
35-36
200 AMP Spool Gun Torch Parts Breakdown & Spare Parts
37-38
TIG Torch Parts Breakdown & Spare Parts
39-40
Welding Trouble Shooting Guide
41-45
Spare Parts Identification
46
Warranty/Warranty Exclusions
47
Summary of Contents for 8619470
Page 48: ...48 NOTES ...
Page 49: ...49 NOTES ...
Page 50: ...50 PRINCESS AUTO LTD Phone 1 800 665 8685 WWW PRINCESSAUTO COM MADE IN CHINA ...