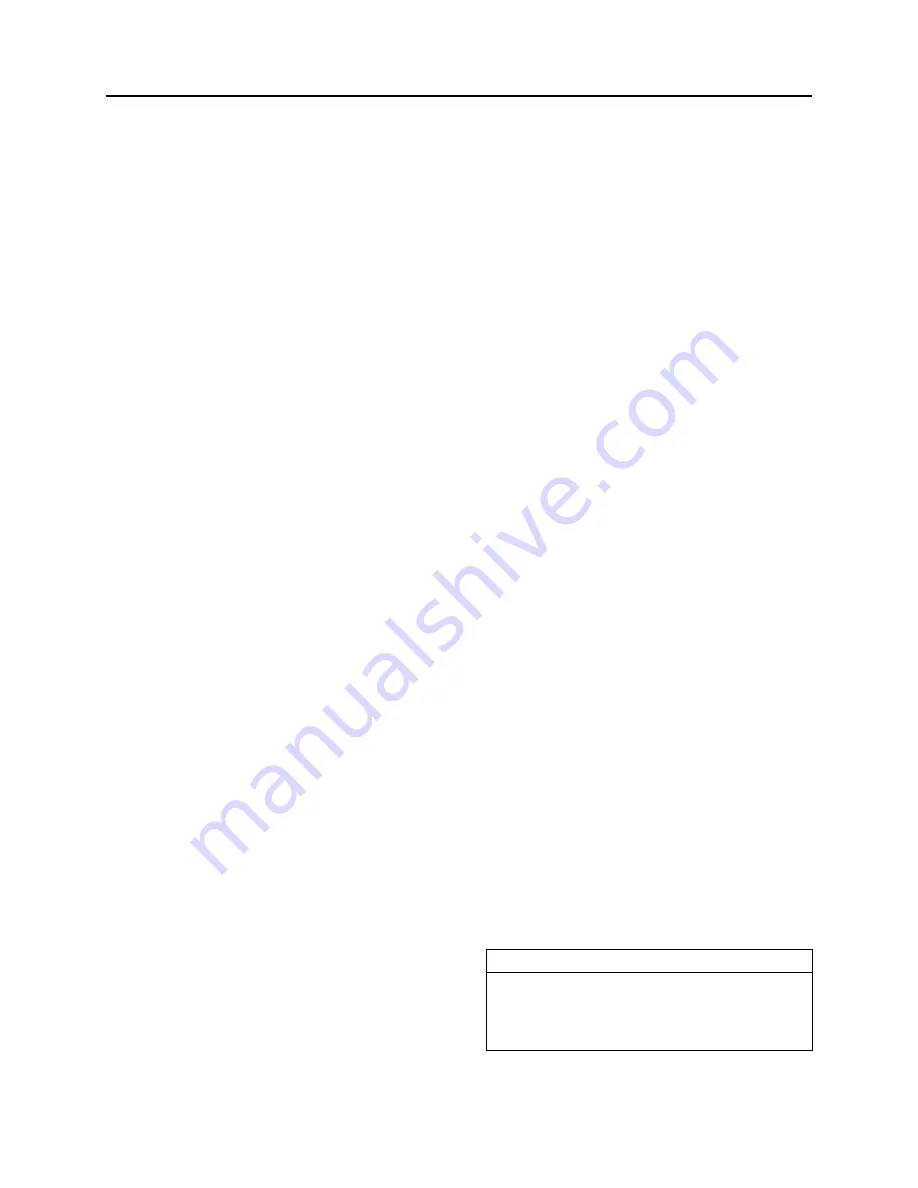
Section 22: HEATING AND AIR CONDITIONING
PA1564
17
8. Wait until pressure gauge reaches 1 to 2 psi
(7 to 14 kPa). To accelerate procedure,
lightly open compressor suction valve until
pressure reaches this value.
8.4
ADDING REFRIGERANT (VAPOR
STATE)
Use the suction service valve on the compressor
to add a small quantity of refrigerant to the
system. Backseat the valve and connect a
charging line from the refrigerant cylinder to the
valve. Tighten connection at level of refrigerant
cylinder and open tank end slightly to purge air
from the charging line. Tighten the charging line
at the compressor. Screw in the stem of suction
valve approximately two turns. Start the engine
and run at fast idle. Add sufficient refrigerant to
bring the level in lower sight glass of receiver
tank to mid-point. Always charge the system
with the cylinder upright and the valve on top to
avoid drawing liquid out of the cylinder.
8.5 EVACUATING
SYSTEM
1. Open both receiver valves by turning “out”
(normal position).
2. Remove the caps from the two 90° adapters
on the suction, discharge valves and
connect two hoses to the vacuum.
3. Place the two compressor valves, suction
and discharge, in neutral position by turning
each one 3 to 4 turns “in” from the “out”
position.
4. Open the solenoid valve by energizing or
manually bypass.
5. Start the vacuum pump. Open the large
(suction) shutoff valve and close the small
vacuum gauge valve.
6. The pressure will drop to approximately 29
inches vacuum (14.2 psi or 97,9 kPa) (the
dial gauge only gives a general idea of the
absolute system pressure.
7. Backseat the compressor valves by turning
“out” all the way.
8. Shut down the vacuum pump.
9. Remove the hoses.
10. Reinstall the caps at the suction valve take-
off points.
8.5.1 Double Sweep Evacuation Procedure
1. Remove any remaining refrigerant from the
system using a refrigerant recovery
machine.
2. Connect the evacuation manifold, vacuum
pump, hoses and micron gauge to the unit.
3. With the unit service valves closed (back
seated) and the vacuum pump and the
thermistor valves open, start the pump and
draw the manifold and hoses into a very
deep vacuum. Shut the vacuum pump off
and see if the vacuum holds. This is to
check the setup for leaks.
4. Midseat the system service valves.
5. Open the vacuum pump and the thermistor
valves. Start the pump and evacuate to a
system pressure of 2000 microns.
6. Close the vacuum pump and the thermistor
valves, turn off the vacuum pump (closing
the thermistor valve protect the valve from
damage).
7. Break the vacuum with clean refrigerant (or
dry nitrogen) and raise the pressure to
approximately 2 PSIG. Monitor the pressure
with the compound gauge.
8. Remove the refrigerant with the recovery
machine.
9. Repeat steps #5 – 8 one time.
10. After the second “sweep”, change the filter
drier (if you have not done so) and
evacuate to 500 microns.
11. Evacuating the system below 500 microns
on systems using the Carrier 05G
compressor may risk drawing air into the
system past the carbon shaft seal.
12. Check to insure that vacuum holds. (If the
pressure continues to rise, it indicates a
leak or moisture in the system).
13. Charge the system with the proper amount
of refrigerant using recommended charging
procedures.
NOTE
This method will aid in preventing
unnecessary system failures by ensuring that
the refrigeration system is free of
contaminants.
Summary of Contents for LE MIRAGE XLII BUS SHELLS
Page 1: ...COACH MANUFACTURER MAINTENANCE MANUAL LE MIRAGE XLII BUS SHELLS PA1564 1ST EDITION...
Page 12: ...Section 00 GENERAL INFORMATION 10 PA1564 FIGURE 13 METRIC US STANDARD CONVERSION TABLE 00005...
Page 13: ...Section 00 GENERAL INFORMATION PA1564 11 FIGURE 14 CONVERSION CHART 00006...
Page 14: ......
Page 30: ......
Page 63: ...SECTION 01 ENGINE PA1564 33 FIGURE 13 POWER PLANT CRADLE INSTALLATION 01140...
Page 108: ......
Page 160: ......
Page 210: ......
Page 229: ...FAULT CODE MANUAL Created on 00 04 25 15 30 1 FAULT CODE MANUAL B7L B7TL B12...
Page 254: ......
Page 281: ......
Page 282: ......
Page 283: ......
Page 284: ......
Page 285: ......
Page 286: ......
Page 287: ......
Page 288: ......
Page 289: ......
Page 290: ......
Page 291: ......
Page 292: ......
Page 309: ......
Page 379: ...Section 12 BRAKE AND AIR SYSTEM PA1564 21 FIGURE 38 AIR OPERATED BRAKING SYSTEM WE...
Page 380: ...Section 12 BRAKE AND AIR SYSTEM PA1564 22 FIGURE 39 AIR OPERATED BRAKING SYSTEM W5...
Page 387: ...Section 12 BRAKE AND AIR SYSTEM PA1564 29 FIGURE 46 ABS 6S 5M CONFIGURATION...
Page 418: ...16 BW2158 Honeywell Commercial Vehicle Systems Company 4 2001 Printed in USA...
Page 422: ......
Page 430: ......
Page 438: ......
Page 445: ......
Page 458: ......
Page 534: ......
Page 540: ......
Page 543: ......
Page 660: ......
Page 661: ......
Page 662: ......
Page 663: ......
Page 664: ......
Page 665: ......
Page 666: ......
Page 667: ......
Page 668: ......
Page 669: ......
Page 670: ......
Page 671: ......
Page 672: ......
Page 673: ......
Page 674: ......
Page 675: ......
Page 676: ......
Page 677: ......
Page 678: ......
Page 679: ......
Page 680: ......
Page 681: ......
Page 682: ......
Page 683: ......
Page 684: ......
Page 685: ......
Page 686: ......
Page 687: ......
Page 688: ......
Page 689: ......
Page 690: ......
Page 691: ......
Page 692: ......
Page 693: ......
Page 694: ......
Page 695: ......
Page 696: ......
Page 697: ......
Page 698: ......
Page 699: ......
Page 700: ......
Page 701: ......
Page 702: ......
Page 703: ......
Page 704: ......
Page 705: ......
Page 706: ......
Page 707: ......
Page 708: ......
Page 709: ......
Page 710: ......
Page 711: ......
Page 712: ......
Page 713: ......
Page 714: ......
Page 715: ......
Page 716: ......
Page 717: ......
Page 718: ......
Page 719: ......
Page 720: ......
Page 721: ......
Page 722: ......
Page 723: ......
Page 724: ......
Page 725: ......
Page 726: ......
Page 727: ......
Page 728: ......
Page 729: ......
Page 730: ......
Page 731: ......
Page 732: ......
Page 733: ......
Page 734: ......
Page 735: ......
Page 736: ......
Page 737: ......
Page 738: ......
Page 739: ......
Page 740: ......
Page 741: ......
Page 742: ......
Page 743: ......
Page 744: ......
Page 745: ......
Page 746: ......
Page 747: ......
Page 748: ......
Page 749: ......
Page 750: ......
Page 751: ......
Page 752: ......
Page 753: ......
Page 754: ......
Page 755: ......
Page 756: ......
Page 757: ......
Page 758: ......
Page 759: ......
Page 760: ......
Page 798: ......
Page 886: ......
Page 900: ......
Page 902: ......
Page 904: ......
Page 910: ......
Page 916: ......
Page 920: ......
Page 924: ......
Page 926: ...PROCEDURE NO SAV00044 REVISION 00 Page 2 of 2 Slide out...
Page 930: ......
Page 932: ......
Page 934: ......
Page 940: ......
Page 944: ......
Page 946: ......
Page 954: ......
Page 976: ......
Page 988: ......
Page 992: ......
Page 996: ......
Page 1032: ......
Page 1038: ......
Page 1044: ......
Page 1064: ......
Page 1086: ...Section 22 HEATING AND AIR CONDITIONING PA1564 18 FIGURE 17 DOUBLE SWEEP EVACUATION SET UP...
Page 1118: ...Section 22 HEATING AND AIR CONDITIONING PA1564 50 FIGURE 54 HEATER LINE SHUTOFF VALVES WE...
Page 1124: ......
Page 1125: ...Compressor 62 11052 Rev A WORKSHOP MANUAL for MODEL 05G TWIN PORT COMPRESSOR R...
Page 1126: ...WORKSHOP MANUAL COMPRESSOR MODEL 05G TWIN PORT...
Page 1149: ...Compressor 62 11053 Rev B SERVICE PARTS LIST for MODEL 05G TWIN PORT COMPRESSOR 1 2 3 4 5 6 R...
Page 1177: ......
Page 1178: ......
Page 1179: ...1...
Page 1180: ...2...
Page 1181: ...3...
Page 1182: ...4...
Page 1183: ...5...
Page 1184: ...6...
Page 1185: ...7...
Page 1186: ...8...
Page 1187: ...9...
Page 1188: ......
Page 1212: ......
Page 1223: ...Section 26 XLII SLIDE OUT PA1564 11...
Page 1224: ...Section 26 XLII SLIDE OUT PA1564 12 FIGURE 16 KEYLESS BUSHING INSTALLATION INSTRUCTION...